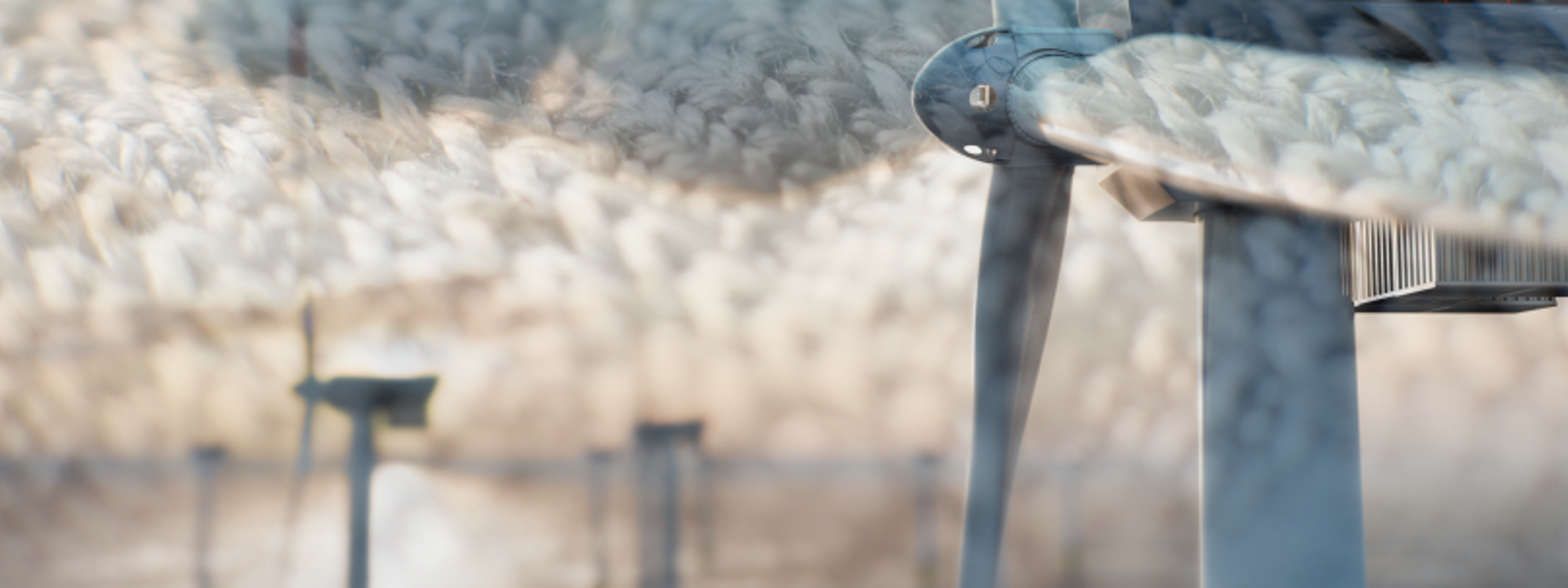
‘Knitting’ smarter wind turbines for a more sustainable renewable energy source
The National Composites Centre helps UK smart textile innovator Footfalls & Heartbeats develop a revolutionary new knitted composite sensor with the potential to optimise the value retention of wind turbines in support of more sustainable renewable energy sources.
Wind energy has a critical role to play in delivering global net zero ambitions. The European Commission offshore energy strategy calls for installed capacity across Europe to be 20 times that of today by 2050. Meeting this requires a quadrupling of Europe’s operational turbines by 2030. To deliver a circular wind economy, asset owners will need access to data-driven models for systems and materials that optimise value retention through a turbine’s service and end-of-life pathways. Innovations in new, sustainable composite wind turbines can make this a reality.
Background
Nottingham-based small enterprise Footfalls & Heartbeats has developed a revolutionary and proprietary process for manufacturing smart fabric which uses nano-scale interactions within the textile to make the fabric itself the sensor, avoiding the need for excessive wiring or miniature electronics. Already working with commercial partners to track environmental changes in application areas such as pressure sensing in wheelchairs and performance monitoring for top athletes, the UK SME was keen to explore their technology’s capability within composite textile applications. Through a recommendation from ACT| The App Association and £12,000 in funding support from Innovate UK EDGE, Footfalls & Heartbeats turned to the National Composites Centre (NCC), part of the High Value Manufacturing Catapult, for guidance to transform their new knitted glass fibre sensor into a commercially viable intelligent composite textile.
Challenge
Footfalls & Heartbeats’ patented technique combines mathematically determined textile structures using electrically conductive yarn to form a repeatable and sensitive sensor network. This sensor network allows for the precise monitoring of physical properties such as temperature or pressure. The potential to extend this capability to measure the mechanical stress in large glass fibre reinforced plastic (GFRP) composite structures could significantly optimise value retention across the wind turbine industry and reduce waste. Real time data would allow for significant savings to be made by preventing equipment downtime due to detecting wind blade wear and damage in situ, and the use of predictive maintenance systems.
Tracking the wear of parts, such as using temperature changes to gauge the rate of erosion, can potentially provide sufficient data to enable a digital twin – a live digital coupling of the state of a physical asset or process to a virtual representation with a functional output that helps operators and engineers study the impact of variables during the design, manufacture or service life of a product. Digital twin technology can reduce development time and the need for physical prototypes. It can improve product quality and performance, cutting waste and lowering costs while enabling predictive maintenance.
With no technical knowledge or expertise of composites, the SME’s challenge was to design their smart fabric to be applicable for large structures. As embedded sensors are usually extremely difficult to achieve within composites, NCC’s task was to resin-infuse Footfalls & Heartbeat’s prototype non-crimp fabric (NCF) glass fibre – complete with embedded metallic yarns – and explore options for connecting the conductive knitted yarns to wiring and acquisition systems that optimised its capability to monitor temperature fluctuations (thermocouple).
Innovation
The comparable results across various samples and baseline thermocouples demonstrated the SME’s technology to be capable of detecting accurate temperature variation throughout the resin infusion process and subsequent testing, which validates the SME’s knitted glass fibre material as a viable novel solution for structural health monitoring and non-destructive testing (NDT). The NCC's findings also determined that Footfalls & Heartbeats’ sensor was already knitted into a fabric ideal for infusion, showcasing its potential in manufacturing environments where it is critical to monitor the resin infusion process.
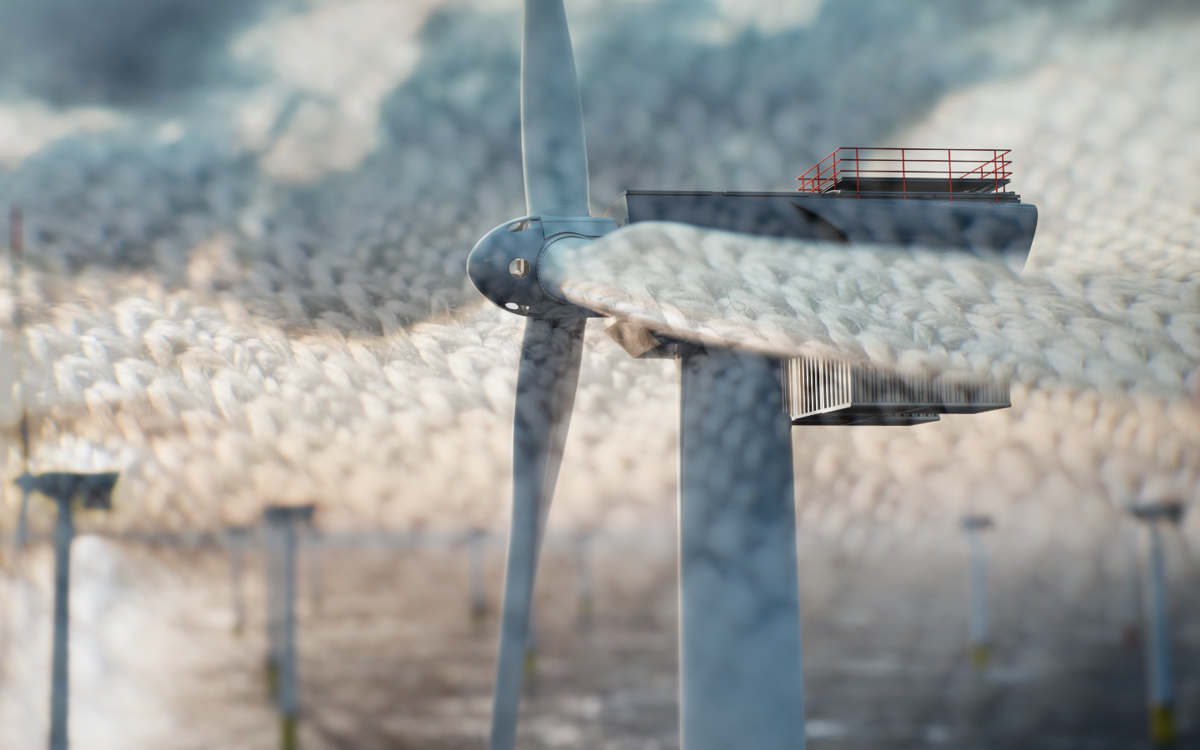
Impact and next steps
The relatively small investment of £12,000 has given Footfalls & Heartbeats a significant ROI, most importantly being the confidence to take the next steps into innovating their technology for a new industry, with the potential to capitalise on the massive scale of UK’s renewable wind energy opportunity.
With support from the NCC, next steps include further exploration into connectivity methods in larger samples and the ability to test strain configurations for more comprehensive structural health capabilities. The SME is also looking into developing a demonstrator to enable engagement with wind energy manufacturers.
Simon McMaster, Founder and Chief Scientific Officer for Footfalls & Heartbeats says:
“The expertise of the National Composites Centre has enabled Footfalls & Heartbeats to turn our proof-of-concept into an accurate thermal sensor integrated into a composite material. This can now be used to demonstrate the sensor to potential clients in a recognised form that also illustrates how easily the knitted sensor can be incorporated into the current manufacturing process. In the future, the NCC’s expertise will also be able to validate the same knitting technique for integrated strain sensors that might be retrofitted to wind turbines for structural health monitoring.”
Adding to this, Tim Woodhouse, Head of SME Delivery at the National Composites Centre says:
“At the National Composites Centre, our dedicated NCC Connect team is focused on supporting businesses of any size explore how innovations could unlock the potential of their business that help bring their ideas into reality. With access to over 350 specialist engineers, designers, and technicians, we work across all sectors, providing a de-risked environment to design, develop, test, and manufacture innovations to deliver solutions that meet your time and cost requirements.
“The NCC is at the forefront of work to capitalise on the scale of the renewable wind energy opportunity. This novel composite application demonstrates the potential to deliver increased commercial returns to developers and asset owners at the same time as driving a future circular economy.”
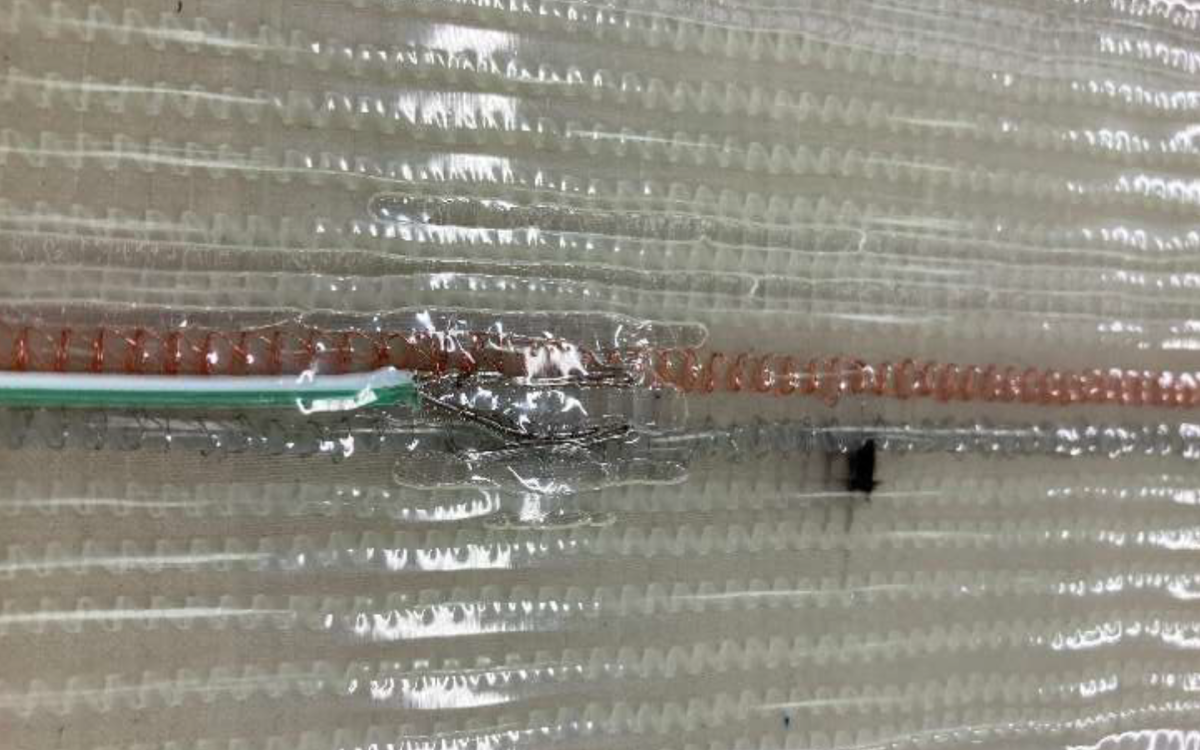
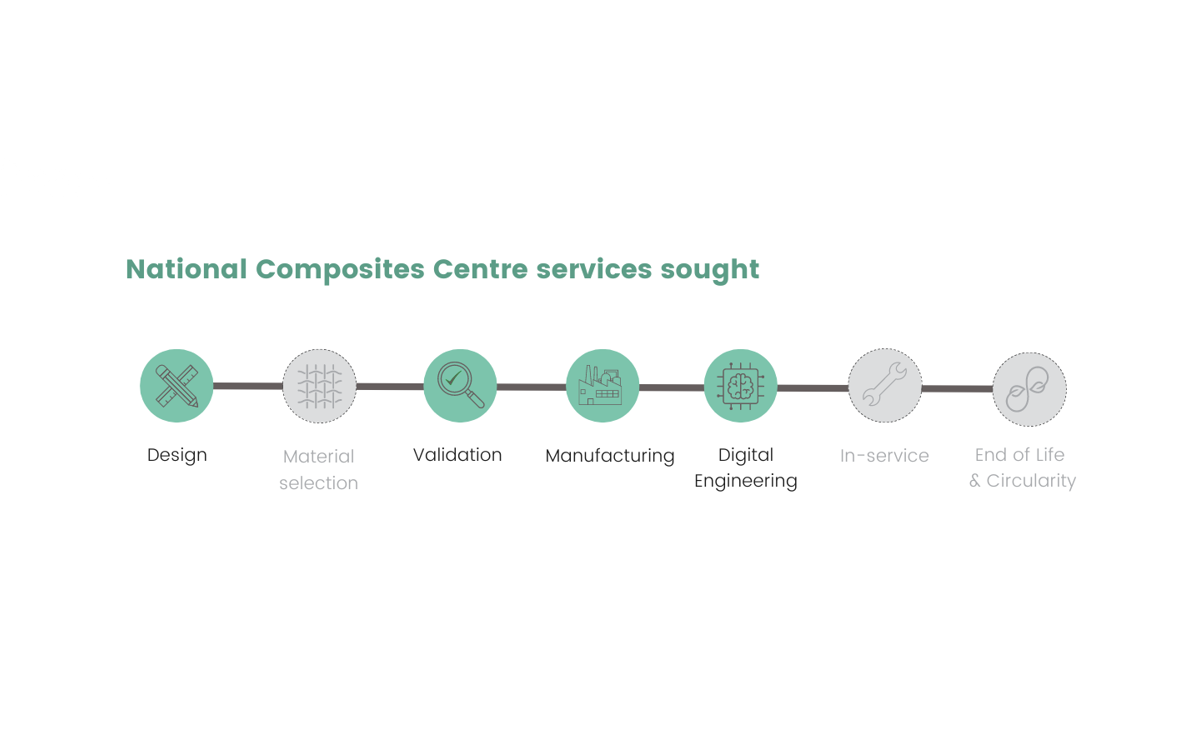