06 July 2023
University of Bristol (UoB) spin-out LMAT Ltd provides design and compensation of tools for composite production. They work closely with the aerospace, wind energy and automotive industries to improve composite production methods and overall product quality.
Challenge
As a small enterprise, LMAT pride themselves in offering a fast turnaround service from receipt of customer materials through to delivery of a comprehensive material card and report. Importantly, LMAT’s thorough process simulation aims to identify any potential issues that may arise during the manufacturing process of composites. Insights, be it potential distortion in lenses or cracks in ignition components during a simulated curing process, can help customers improve targeted product design elements, prior to costly mass production.
A particular business opportunity involved a highly complex tooling material. To enable further work in-house, LMAT required a moulded panel to be cut into smaller samples, with a very tight tolerance.
LMAT leveraged their SME Affiliate status for urgent support from the National Composites Centre (NCC) to achieve their high precision cutting on time.
Solution and Result
NCC Connect’s dedicated SME support team worked quickly with the Filton-based enterprise to understand their exact requirements, as well as propose a viable and affordable solution that met LMAT’s tight timeline: a material laboratory saw to grip and machine ten precise 25mm-wide specimens to a specific diagram.
As a result, from quote to specimen collection, NCC Connect facilitated a rapid 12-work hour turnaround – significantly quicker than if LMAT had approached a commercial material laboratory.
Impact
According to Tomasz Garstka, CEO of LMAT, ‘Customers opting for a small business service instead of a larger organisation typically have higher expectations on service delivery, and a zero tolerance for delays. As an SME Affiliate member, I find the NCC Connect’s familiarity with the work that we do translates to a much-needed shorthand when communicating our specific requirements. This contributes to a confidence that the end result by the NCC will always be delivered right the first time, and in turn, helps us deliver reliably on our own customer promise.’
Tim Woodhouse, Head of SME Delivery at the National Composites Centre says, “As an open-access technology centre delivering world-class research and development in the future of composites, sustainability and digital innovations, the NCC prides itself on being agile enough to support businesses of all sizes. Our dedicated SME team strips out the complexity of working with a large organisation and facilitates access to affordable solutions that helps businesses overcome barriers and accelerate their growth.”
For more information on how the NCC can help your business, reach out to [email protected]
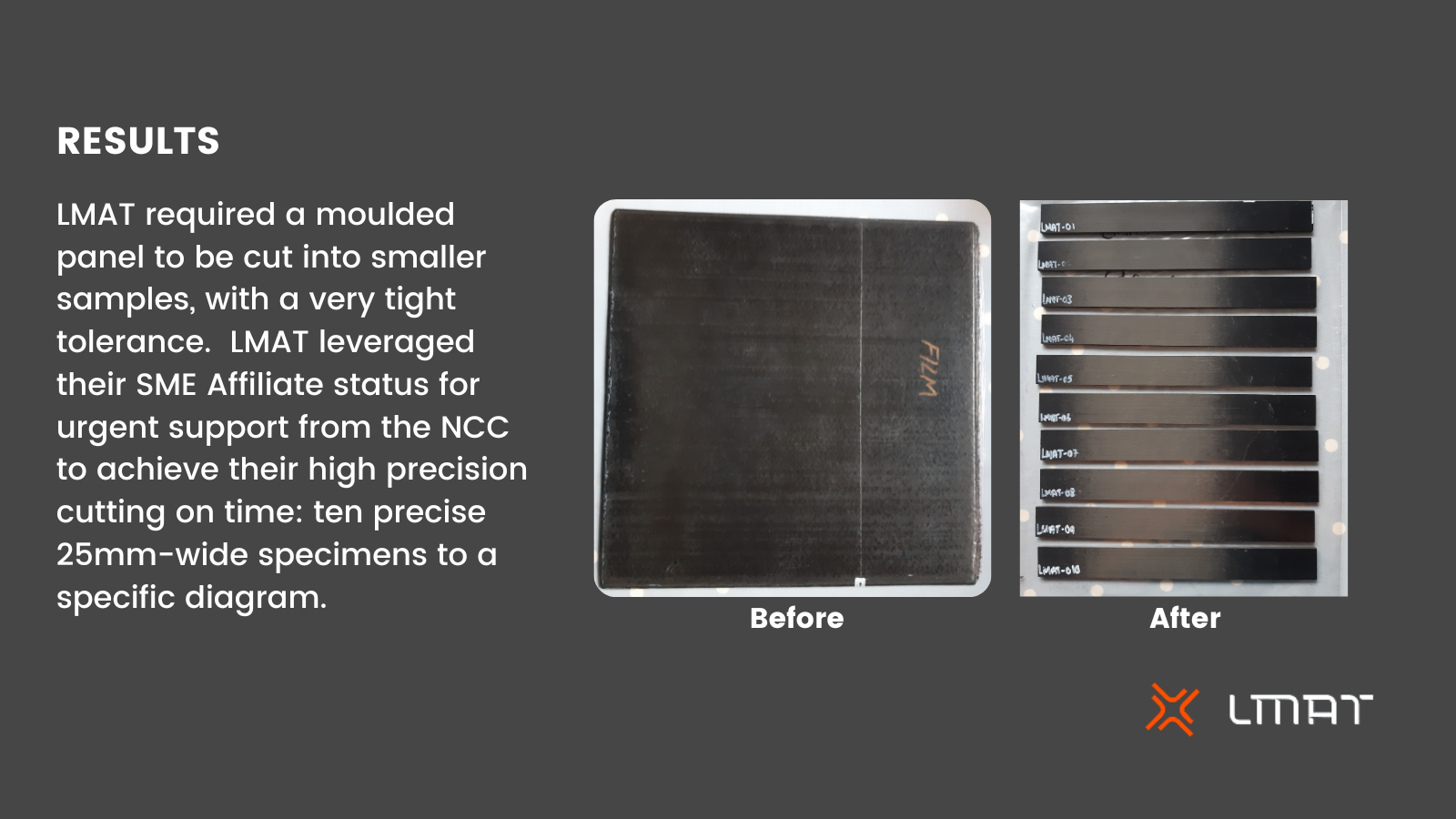