30 March 2023
In the 18-months since taking up residence at the National Composite Centre (NCC), courtesy of Innovate UK funding and private investment, University of Bristol spin-out and micro-enterprise Actuation Lab has been working on developing the world’s first industrial-grade origami-inspired actuator.
The single moving part mechanism helps address the problems of high servicing requirements and poor longevity of current actuators in the energy, marine and processing industries, while significantly reducing safety risks even in the most hostile of environments.
Challenge
Actuators are components that make machines move. Pneumatic actuators, which convert compressed air to generate movement, are used to open and close valves or control the operation of heating, ventilation, and air conditioning (HVAC) dampers. These actuators are traditionally made up of a complex assembly of metal components and sliding seals.
In corrosive environments such as aboard ships, in desalination facilities, and in factories that use harsh wash-down chemicals, these components can become corroded which leads to degradation in machine performance. Due to the high costs associated with unplanned shutdown processes, these actuators may be left to degrade further until the next scheduled maintenance.
In extreme cases, this delay has led to catastrophic failures where actuator internals, such as metal springs, have been ejected at high speed. In addition to risks of injury, the potential risks include chemical release, property damage, power loss, and environmental contamination.
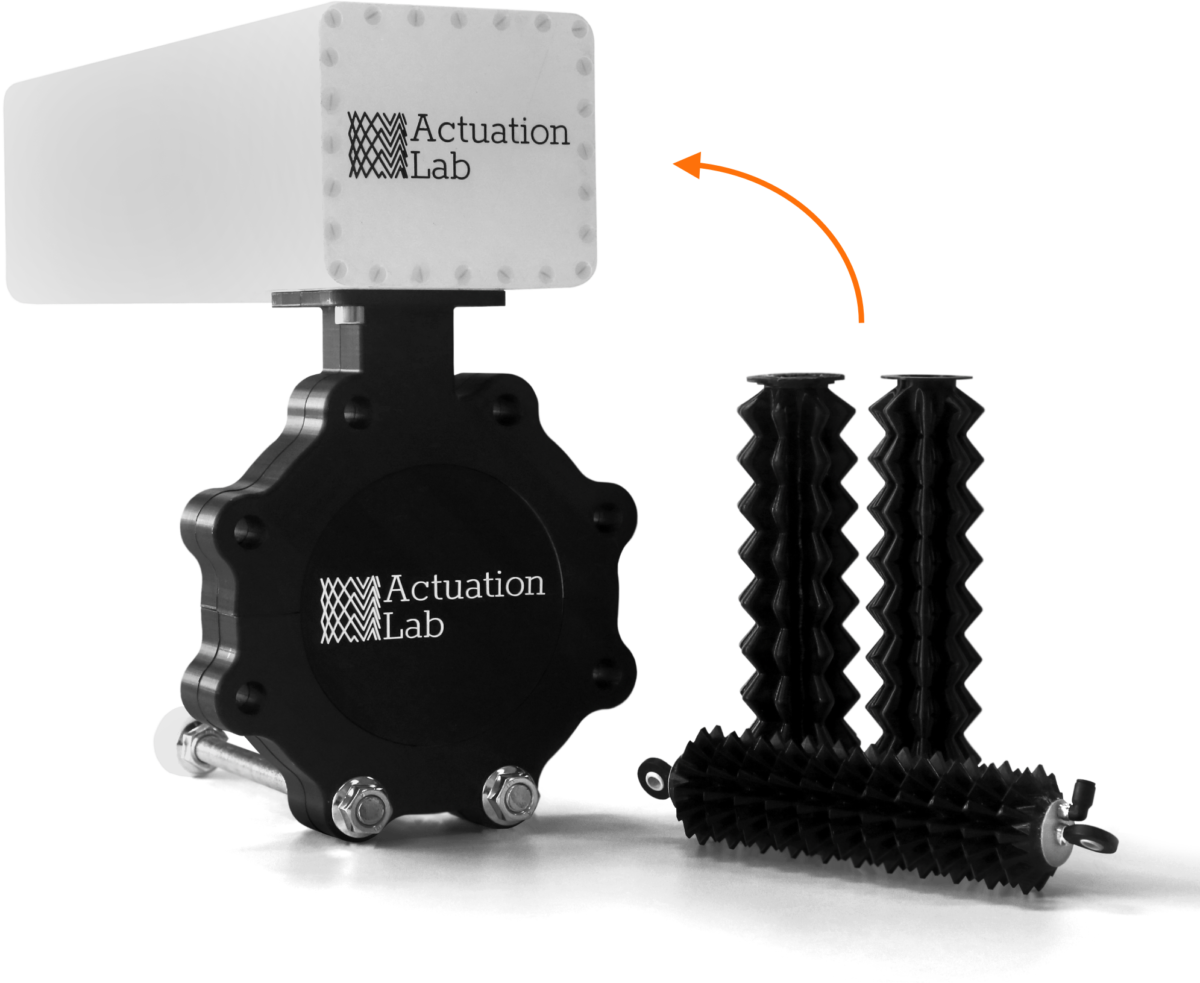
Innovation
Actuation Lab’s Callimorph Actuator takes the nuts, bolts, springs and shafts out of the traditional pneumatic actuator and replaces them with a single moving part built from 100 percent corrosion-resistant composite materials.
Inspired by origami structures that act like an artificial muscle, the flexible technology is made of tough fibres and polymer resin that is significantly lighter to its metal counterpart.
Benefits of the patent-pending design include:
- Reliability : As a simplified single moving component, the Callimorph has no sliding parts that would be subject to wear. This reduces the need for maintenance, and prevents the crippling costs associated with unplanned downtime.
- Withstands harsh environments : Engineered with non-metal components that resists corrosion, the product is designed to survive extreme weather climates.
- Runs on dirty air : The product’s wear-free design is optimised to survive when run for long periods on an air supply which may be contaminated with particulates or has a high moisture content. This helps double the average lifetime of traditional actuators predicted in aging facilities.
- Delivers extreme force : Harnessing the power of origami, the Callimorph contracts like a muscle when pressurised, with five times the force of a traditional pneumatic piston. Its spring-like structure means it has a two-way action, making it a versatile and powerful way of creating mechanical movement.
- Universal fit : The Callimorph is modular and designed to be retrofitted to valves currently in service, replacing failed actuators with minimal downtime. Being up to one third the weight of its metal counterpart also makes it easier to transport, handle and install.
Impact
The Callimorph Actuator has been designed as a drop-in replacement for actuators already operating in the millions worldwide. For the UK energy industry alone, this is estimated to relieve at least £368 million maintenance backlog of corroded and worn valve actuators, as well as reducing maintenance burdens
worldwide.
In current actuator designs, seals are easily damaged by contaminants and dirt in the air supply, leading to compressed air leaks around the O-ring. It is thought that compressed air leaking from pneumatic equipment accounts for 2% of industrial emissions globally. By eliminating leak paths, Actuation Lab’s technology is tackling this issue, as well as being designed to outlast current metallic actuators, reducing material consumption and waste.
Growing SME Capability
An Innovate UK funded ICURe project enabled the provision of a flexible workshop and office space at the NCC in the first two years of Actuation Lab’s operation. This provision played a significant role in helping the SME to focus resources into the development of their spin-out. For example, access to a secure lab space,
cutting-edge technology as well as some 350 specialist composite material engineers available helped Actuation Lab accelerate learning from proving an initial concept in 3D print, to progressing a trial product.
This included delivering the evidence required to prove their technology’s capability while enhancing
knowledge base regarding the potential of recyclable thermoplastic composite components in harsh climates. Such achievements contributed to the confidence to expand their award-winning three-person organisation to the ten-member strong team they have today.
According to Simon Bates, CEO of Actuation Lab:
"The access to dedicated composite manufacturing facilities and expertise that the NCC provides allowed us to iterate our technology rapidly and generate protectable intellectual property, which is key to our business. The NCC has provided a vital steppingstone for us, enabling us to progress from basic demonstrators developed at the University, to prototypes that are taken seriously by end users, enabling us to garner interest for trials."
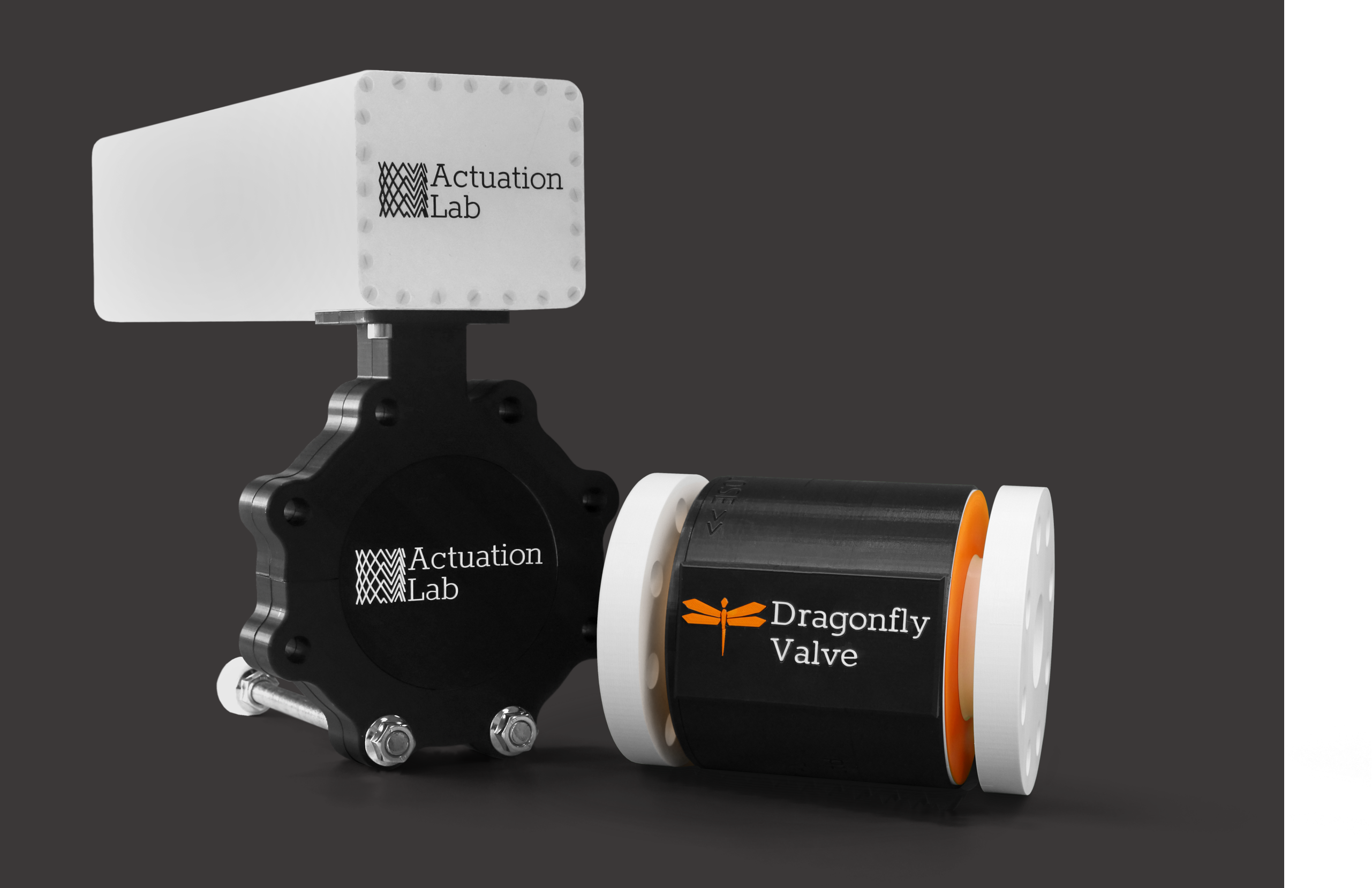
Next steps
The award-winning SME is currently working with industry trial partners to demonstrate the Callimorph’s technology in challenging or corrosive conditions before the product’s commercial launch later next year.
Supported by the UK’s Department of Business, Energy and Industrial Strategy, the SME’s second product in development is the Dragonfly valve. This electrically actuated origami inspired valve has been designed to have a leak-free, stemless operation and be built from hydrogen compatible materials. The valve is being developed to prevent an estimated 75,000 tonnes of potent greenhouse gas from escaping annually and allow hydrogen suppliers and users to operate in safety.
Tim Woodhouse, Head of SME Delivery at the National Composites Centre says:
"It is estimated that 80% of innovations fail in a ‘valley of death’ between academia and industry. This is why the right support in the first two years of operation is crucial. Understanding the importance of SMEs to the UK industry, our dedicated SME team helps tailor support to ensure enterprises of any size, including university spinouts, can capitalise on the best expertise, equipment and funding available in the country to accelerate development of their concepts and ideas into reality."
If you are an SME looking for help to fast-track your innovation and overcome the barriers to your business growth, contact the NCC Connect team to find out more about our capabilities and how we can support your business.