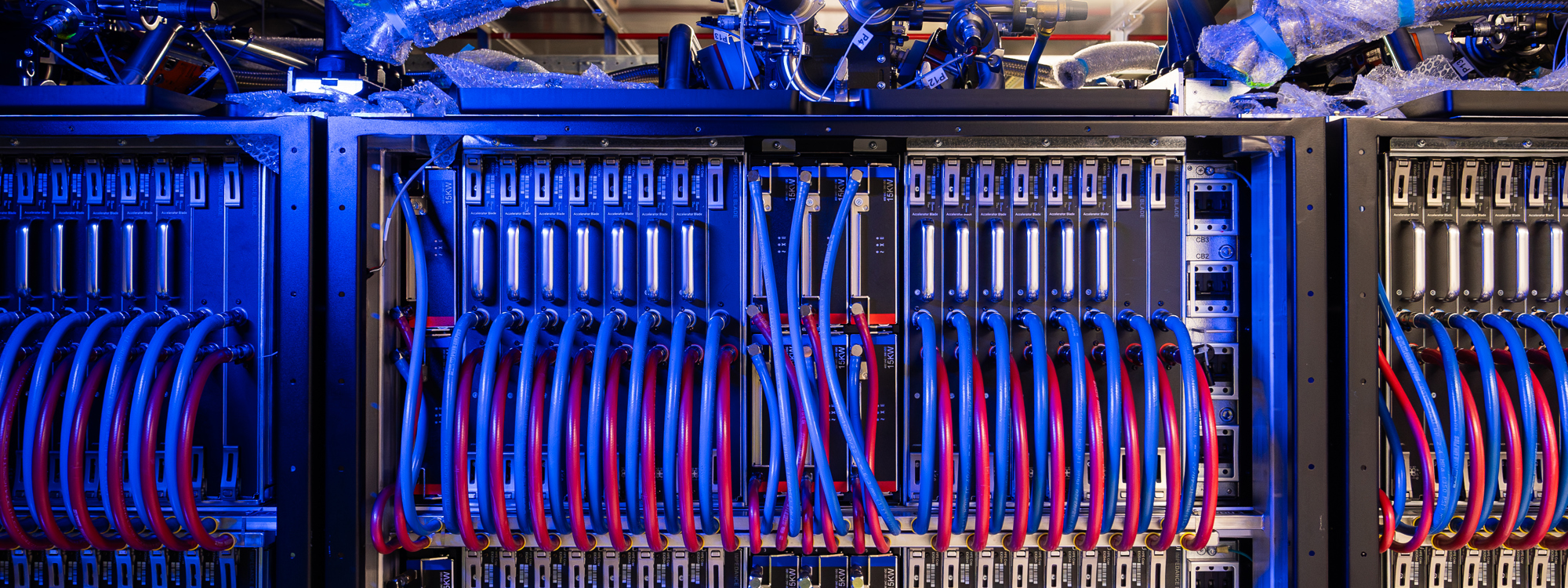
As business and industry across the country digest the UK’s Modern Industrial Strategy, Eoin Simon, Chief Technologist for Compute and Manufacture at NCC in Bristol, delves into the role that AI is playing in the acceleration of advanced manufacturing capability.
With the UK setting its sights on a smarter, cleaner, and more resilient and productive industrial future, artificial intelligence is no longer on the horizon — it’s here and transforming the way we make things.
And with safety and sovereignty on the top of Government priorities in an internationally more competitive and uncertain world, NCC has been exploring how to reshape manufacturing by embedding AI capability in design, production and quality assurance.
NCC, based in Bristol and part of the UK’s High Value Manufacturing Catapult, operates at the intersection of digital engineering, composite materials science, and applied industrial research. It brings together over 400 engineers, 14 years of manufacturing data, and now hosts the UK’s most powerful supercomputer, Isambard-AI, developed in collaboration with the University of Bristol and powered-up by the Secretary of State for Science, Innovation and Technology just last week.
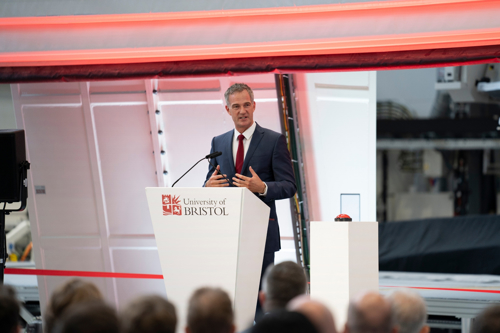
This unique convergence of infrastructure, expertise, and cross-sector collaboration provides a platform to develop and deploy Large Reasoning Models (LRMs) and other AI architectures in ways that respond to real-world constraints, including safety, certification, and economic viability.
From Data-Rich Environments to Trustworthy AI
Manufacturing, particularly in sectors such as aerospace, defence, and energy, presents an environment rich in operational data but constrained by complex requirements. While AI models can be rapidly developed in silos, industrial applications demand models that are more explainable, certifiable - and above all robust - under a wide range of conditions.
At NCC, the emphasis is not on adopting new AI technologies, but on ensuring that these tools are embedded within established engineering workflows. Our goal is to augment — rather than replace — human and computational design processes, to increase efficiency while maintaining the high standards of performance and reliability required by industry.
The long-cited phrase from statistician George Box — “All models are wrong, but some are useful” — remains apt.
Our objective is to improve model utility continuously, with failure tolerances in the region of 1 in 10 billion for certain applications. This level of rigour places constraints on model development that are rarely encountered in other AI domains, such as consumer tech or social data science.
Cross-Sectoral Translation and Knowledge Transfer
Clusters of excellence, physical space and state-of-the-art equipment remain critical ingredients even in a world of open data.
One of the more innovative aspects of NCC’s approach lies in its ability to facilitate knowledge transfer between sectors. For example, in collaboration with Airbus, we have applied non-destructive evaluation (NDE) techniques originally developed for breast cancer screening to the manufacturing of aircraft wing components. By integrating in-process optical scanning, we can reduce or remove entire stages of verification, offering a potential step-change in productivity without compromising safety.

This form of translational research — where medical imaging methodologies inform aerospace quality assurance — illustrates how AI in manufacturing is not only about algorithm development but about creating the institutional and technological conditions that allow cross-disciplinary fertilisation.
Case Study: The TURBO Project and Sustainable Manufacturing
The TURBO project, in partnership with Siemens Gamesa Renewable Energy and funded through European research mechanisms, addresses a longstanding challenge in wind turbine blade production: the variability of resin infusion. Small inconsistencies at this stage can produce structural defects, which traditionally require time-intensive and resource-heavy rework procedures.
By integrating sensor data into a machine learning framework, TURBO allows for dynamic adjustment to the infusion process. Our early results suggest that rework, scrap, and repair can be reduced by up to 80%, which has both economic and sustainability implications. The system is also generating synthetic training data, improving the model with each iteration and creating a feedback loop that enhances reliability over time.
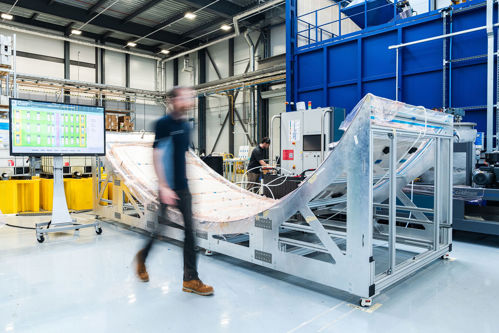
Such projects reflect a broader systems engineering perspective, where machine learning is embedded within process control, and a digital infrastructure is tightly integrated with physical manufacturing assets.
Implications for Policy and Capability Development
The development of trustworthy, scalable AI in manufacturing requires more than computational power. It requires institutional alignment, sectoral coordination, and human capital development. NCC works with the UK Government, the West of England Combined Authority and over 70 member organisations to create the conditions under which innovation can move from prototype to production.
This includes ensuring that companies — particularly SMEs — have access to state-of-the-art infrastructure such as secure compute environments, testing facilities, and upskilling opportunities for the next generation of engineers and data scientists.
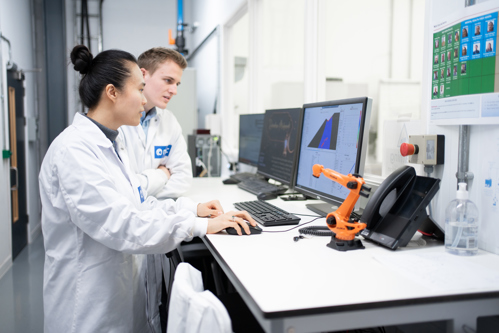
AI integration is not merely a technological challenge, but a socio-technical transition involving culture, skills, systems architecture, and trust. Only by designing for these interdependencies can AI contribute meaningfully to productivity, international competitiveness, sustainability, and sovereign resilience in UK manufacturing.
Conclusion
AI is often framed in the context of breakthrough technologies or disruptive innovation. However, in advanced manufacturing, its real value lies in systems-level integration — where insights from data, materials science, and domain-specific engineering are synthesised to improve how we make critical components and infrastructure.
At NCC, our work continues to demonstrate that with the right combination of process, collaboration, and applied engineering, AI can contribute to a more intelligent, adaptive, competitive and sustainable industrial base.
This is the reason we are a described as a ‘core partner’ for UK Government in the Industrial Strategy and is why the West of England remains a globally recognised hub for industrial innovation.