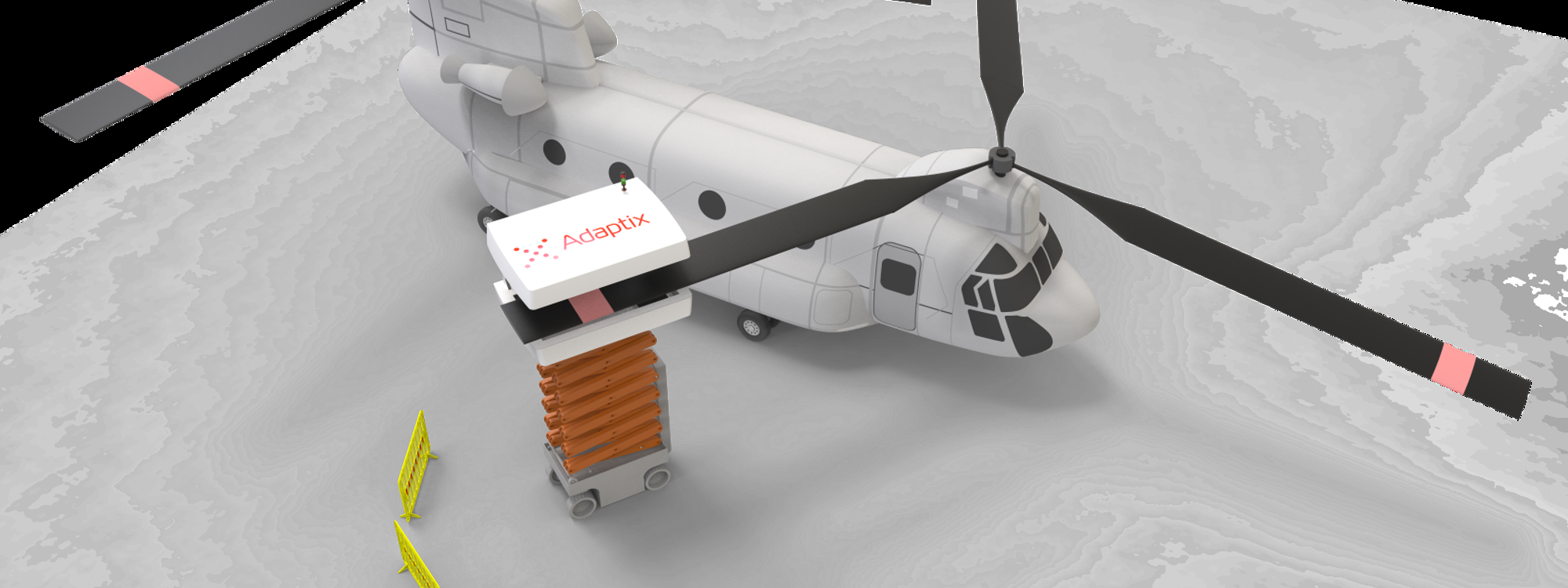
UK SME's affordable non-destructive testing solution to meet emerging challenges in the aerospace sector
NCC helps UK SME Adaptix Ltd extend medical imaging expertise into non-destructive testing (NDT) for the aviation industry, with the potential to break into a market estimated at £1.5 billion annually.
Oxford-based Adaptix Ltd is a radiology specialist at the forefront of imaging technology. Already offering portable low-dose 3D imaging to veterinary, dentistry, and orthopaedic sectors, the medium-enterprise was keen to explore its deep-tech capabilities within the aerospace manufacturing process, particularly the growing preform inspection market. With funding support from the Aerospace Technology Institute (ATI) and the National Aerospace Technology Exploitation Programme (NATEP), the UK SME turned to NCC for help to adapt their existing technology to meet emerging challenges in the aerospace sector.
Challenge
Stricter compliance regulations amid rising operating costs in the aerospace industry calls for inspection methods that are precise yet affordable. However, the NDT options that promote consistency and reliability of composite aerostructures remain limited, costly, and time-consuming. The conventional gold-standard systems include:
- Computerized tomography (CT) scanners: Premium CT scanners require a shielded space. Such constraints often limit parts that can be scanned or require the aerostructure to be detached into parts, which breaks the production workflow.
- X-ray testing methods: While radiography delivers a complete image, present x-ray testing demand a wide exclusion zone when used unshielded. This usually means a hangar clearance, which can incur an overnight cost and coordination with other hanger users. This method also lacks 3D imaging capabilities.
- Ultrasonic testing: High frequency sound waves detect flaws inside a component as well as its surface. While one of the fastest options, this test only applies to cured composites which must sit in a resin matrix to support the propagation of ultrasonic waves. Unlike radiography, ultrasound requires an interpretation of the signals received to infer information about the quality of the component being tested.
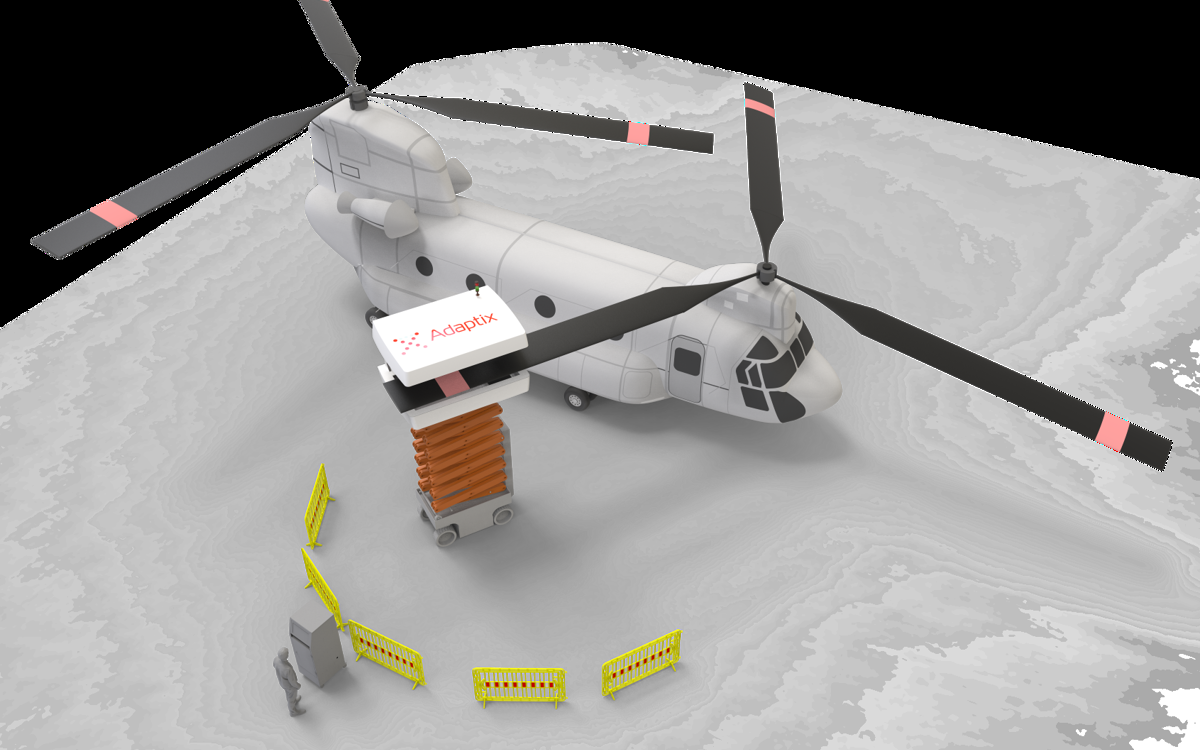
Results
To understand the current state of detectability and where Adaptix’s technology could potentially fit, the team of experts at NCC completed a market study.
NCC then manufactured and supplied an according sample of aerospace-type reference standards containing typical defects. These standards were run through conventional NDT systems to benchmark against the performance of the SME’s portable AdaptixNDE 3D X-ray, which was mounted on twin agile inspection robots.
The comparable results demonstrated the SME’s low-power solution to be capable of inspecting dry, and pre-cure fibre forms. Importantly, the technology proved well-suited to finding failure modes typical in complex composite structures, such as voids, variation in weave, inclusions, and needle porosity. In some respects, the 3D X-ray even performed better than the gold-standard NDT systems: for example, beating average CT scan times by up to 96% - from two hours to just five minutes, while still providing clear digitised output images. Due to its medical heritage, its low-flux X-ray also significantly reduced average exclusion zones, enabling the portable technology to be brought directly to an aerospace structure with minimal disruption to a busy hangar.
Innovation
The industry test lab environment at NCC also provided the opportunity to explore the ability to safely incorporate detectable integrated fingerprints within aerospace components. The results successfully showcased the capability of AdaptixNDE scanners and software to accurately detect and identify 3D fingerprints comprised of 200-micron diameter ceramic particles – characteristics that did not significantly knockdown key material properties of components.
Impact
Compared to conventional gold-standard systems, the AdaptixNDE 3D X-ray offers a potentially cheaper, quicker and more detailed NDT option to evaluating high-value and safety critical products for Composites and Metal Additive manufacturing. Its ability to evaluate the progress of complex composite aerostructures throughout the manufacturing process also extends to monitoring product performance throughout service.
Key benefits include:
- Earlier use in manufacturing: Assessment during manual or automated manufacture - and particaulrly to dry-fibre preform prior to infusion - provides 3D internal visualisation which helps identify items requiring immediate re-work, thereby reducing economic and environmental cost of waste. For example, if the UK’s annual market for aerospace and defence composites is estimated at £1.5 billion, the impact of rework and scrapping parts at even an optimistic 10% defect rate would be considerable. As defect rates tend to correspond with the complexity of components, early detection before cure presents a powerful tool towards tackling the cost of non-quality across the industry.
- Maintenance: The ability to monitor parts through life helps flag any potential wear-and-tear issue down to the specific part, thereby optimising service life and reducing industry waste. Tracking the wear of parts also provides sufficient data to enable a digital twin – a high-fidelity simulation and modelling, data analytics and machine learning that helps operators study the impact of variables, such as changes to the design, manufacturing processes, environmental conditions and materials. Digital twin technology can reduce development time without the need for a physical prototype; improve product quality and performance; cut waste and lower costs while enabling predictive maintenance.
- Counterfeit protection: Ongoing work with NCC is looking into embedding a 3D fingerprint or Physically Unclonable Feature (PUF) to enable life-long proof of authenticity to flag substandard counterfeit parts that may compromise safety and impact revenues.
- Configurable: Intended to be accessible across the supply chain, including Maintenance, Repair and Operations (MRO), the technology can be configured for static, automated inspection in a factory setting or while attached to an aircraft without the need for coupling fluids or interference with painted surfaces.
For the SME, the scope of opportunity from this project not only supported the safeguarding of two jobs at Adaptix, but the creation of two new roles supporting business development.
Next steps
With follow-on grants from ATI and NATEP, Adaptix’s growing team continues to work with NCC to further develop their technology for testing real-world components, and scaling-up a prototype for larger (and denser) aerostructure parts. Ongoing engagement with aerospace primes, original equipment manufacturers (OEMs), ATI, and the supply chain is helping the SME understand the requirements for a viable commercial launch, and the unique opportunity to be involved in the development of inspection strategies for new aerospace products that may have otherwise been lost to non-UK companies.
Andy Barnes, Commercial Director NDE for Adaptix says:
"Since venturing into this new market, NCC has proven a great ally through relevant industry connections, comparable trials to other inspection modalities, and sharing their general expertise to improve the integrity of our product. This promotes our confidence that we’ll be delivering a competitive new solution to the NDT space. Already, the support in demonstrating our capabilities has enabled Adaptix to engage and develop relationships with a number of aerospace OEMs."
Adding to this, Andrew Limmack, Chief Engineer for Aero Propulsion, NCC says:
"The National Composites Centre already offers aerospace customers a 'beyond' state-of-the-art manufacturing testbed to trial new process innovations. As such, we were in the perfect position to provide AdaptixNDE the same de-risked environment to design, develop, test, and adapt their existing technology, with the next step being to help them get to market."
If you are a start-up, scale-up or SME, reach out to NCC's dedicated SME team for support to fast-track your innovation and overcome any potential barriers to business growth.