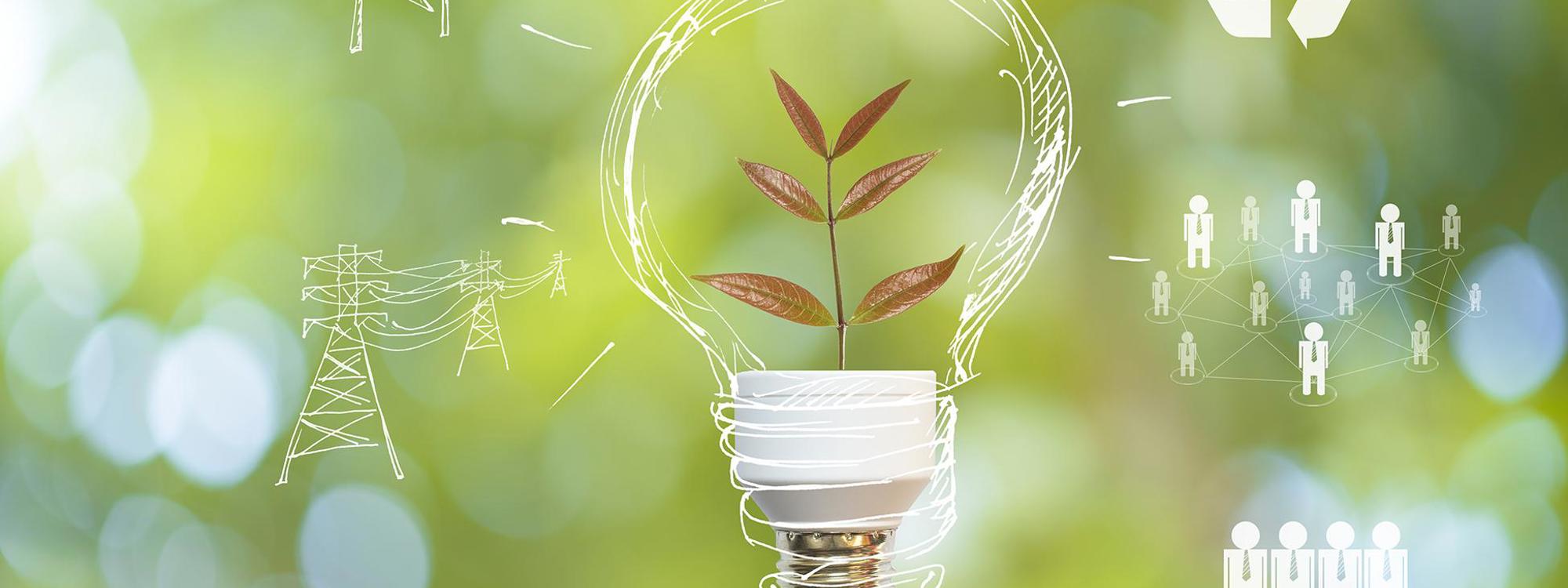
Can we achieve a functioning circular economy for wind AND meet net zero 2050?
The industry is aiming for Net Zero in 2050. The UK alone is targeting 50 GW of offshore wind by 2030, from ~10 GW today which will require a huge increase in resource usage. Where does circularity fit into this drive for emissions reduction and increased installed capacity?
Circularity is integral for emissions reduction and increased installed capacity, both in addressing the very real challenge posed by blades already in service and to avoid perpetuating those challenges in future. Circularity, industry growth and net zero cannot be seen as mutually exclusive. In fact, they should be considered complementary requirements of a sustainable system.
Many people might wonder if we can really achieve those huge growth targets while adhering to the core principles of the circular economy (reducing waste, increasing resource efficiency, and regenerating natural systems). It is possible; however, it will require a mindset shift throughout the value chain. This shift, though challenging, will improve competitiveness of project tenders long before it becomes a licence to operate in our industry.
What are we aiming for in SusWIND?
The SusWIND programme is working to support industry to minimise resource scarcity impacts and improve costs alongside the main goal of preparing for when legislation comes into force and tender criteria broaden beyond levelised cost of energy (LCOE).
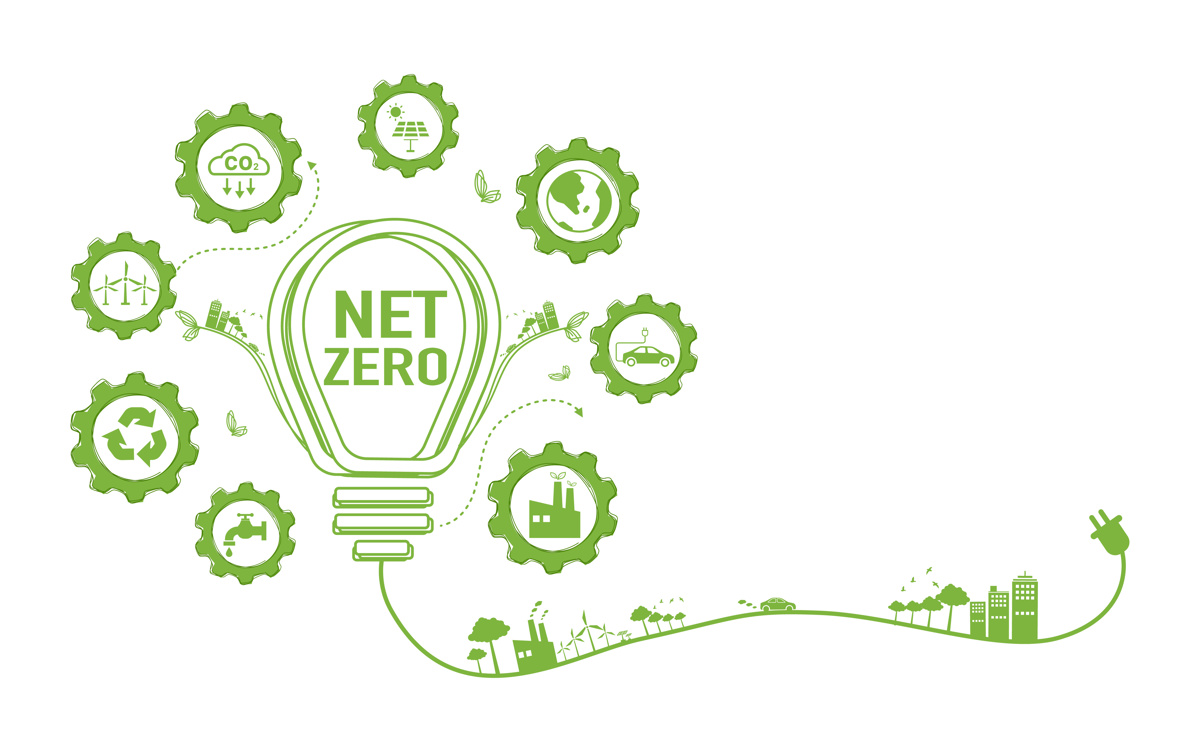
Every industry has the responsibility to take this opportunity for reinvention. To help the wind industry make this systemic change, we are applying our expertise to wind turbine blades and are working with our commercial partners on:
- Circular concepts for blade design
- Materials
- Supply chain for the blade waste
When it comes to design, it is important to think about what circularity means for blades. Using the waste hierarchy (Figure 1) can be a guide to consider how circular concepts could be applied to blade design.
Wind turbine blade design
Translating these to the blade life cycle, as shown in Figure 2, provides an indication of how they could each be incorporated into a design methodology.
Design for Repair for wind turbine blades, for example, needs to be thought about carefully. Blade manufacturers aim for zero repairs in the lifetime, as this maximises AEP and reduces cost of energy, but it is accepted that some repair will have to be carried out. As such, a strategy of design for low risk and low-cost repairs should be considered.
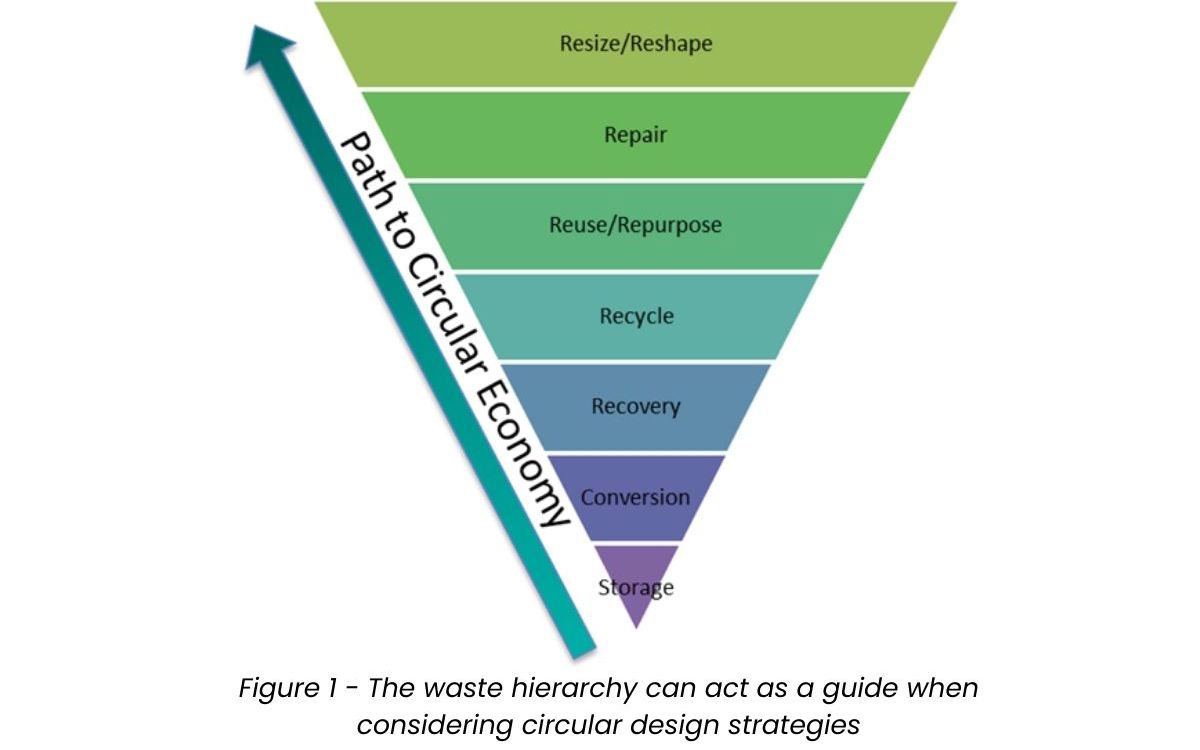
Design for Repurposing is also a difficult concept to apply to wind turbine blades. Planning for repurposing of the structure, or components thereof, is theoretically favourable, as it requires less energy than recycling, provides a new structure without the need for virgin resources and preserves value. In practice, however, the designer is required to know the probable application after decommissioning. Given the 25+ year service life, they are extremely unlikely to have this knowledge available to them.
If considering Design for Recycling, which should include a Design for Disassembly approach, the practicalities of doing so can be viewed in terms of the circularity of the approach. We have proposed this as: total and partial circular design, and spiral design. Where total means that the reclaimed materials can be used in subsequent blades of the same design with equivalent performance; partial refers to equivalent performance in a different design, and spiral is a blade of different design and performance. Using these concepts, it is then possible to start setting requirements for the reclamation of materials and how they can be utilised after recycling.
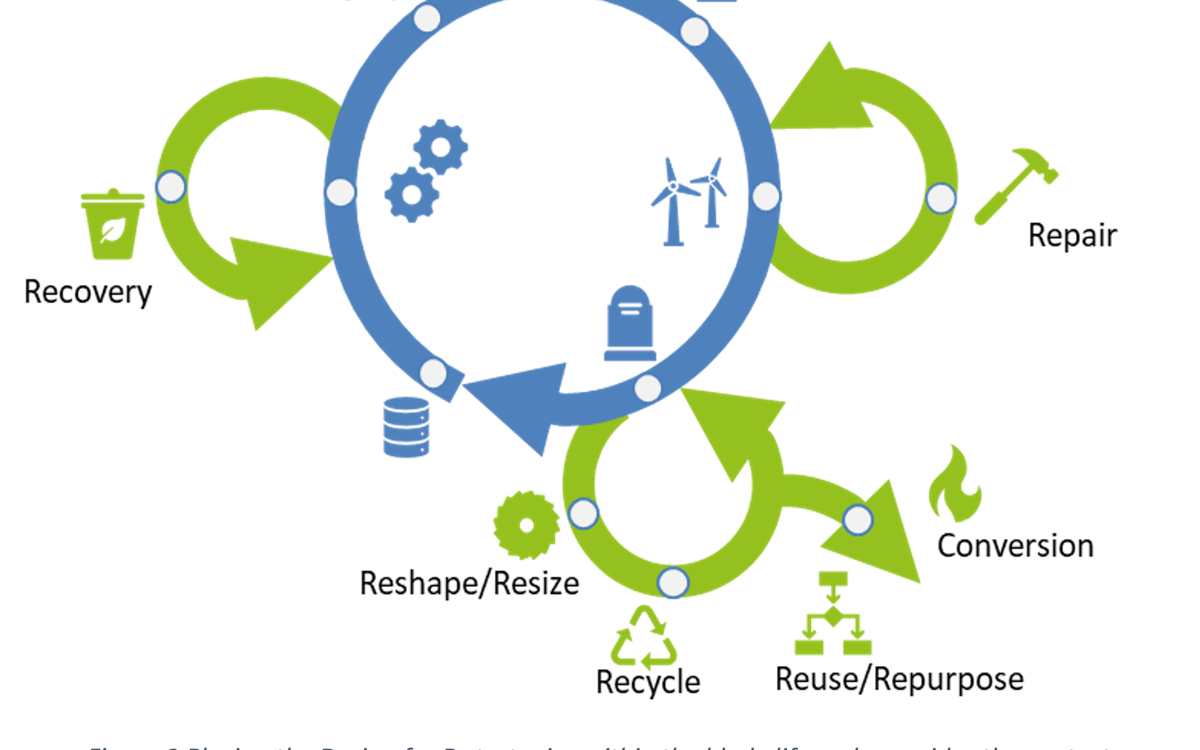
Environmental impact of materials
Intertwined with design is the use of materials. When materials contribute over 70% of the environmental impact of a blade from cradle-to-grave, it is vital to consider how they’re used, their provenance, and possible repair and EoL options. This can be done via life cycle assessment (LCA) and, once coupled with structural analysis, provides a robust measure of the impact that materials selection can have on the blade life cycle. Such a platform allows alternative materials to be introduced into the design and assessed on their potential to reduce carbon footprint whilst maintaining AEP, which is essential for any solution to be credible. Fortunately, credible alternative materials do exist and are set to usher in a shift in how materials for blades are selected and utilised, ultimately lowering the environmental impact through-life.
It is important to recognise that underpinning all these approaches should be the goal of eliminating, or designing out, waste itself. Focus tends to be on end-of-life, particularly recycling, but this is only one aspect. The amount of waste created in blade manufacture is significant (>20% of blade mass), which represents an enormous loss of resources, not to mention the financial burden. Thus, incorporating circularity into design, with sustainable materials, can move beyond the idea of recycling towards efficient resource management and preserving value.
This is why SusWIND is bringing together circular design, materials, manufacturing waste and the supply chain for end-of-life- to help reach Net Zero 2050 in the most sustainable way possible.
Jonathan Fuller, Research engineer for Energy at the National Composites Centre