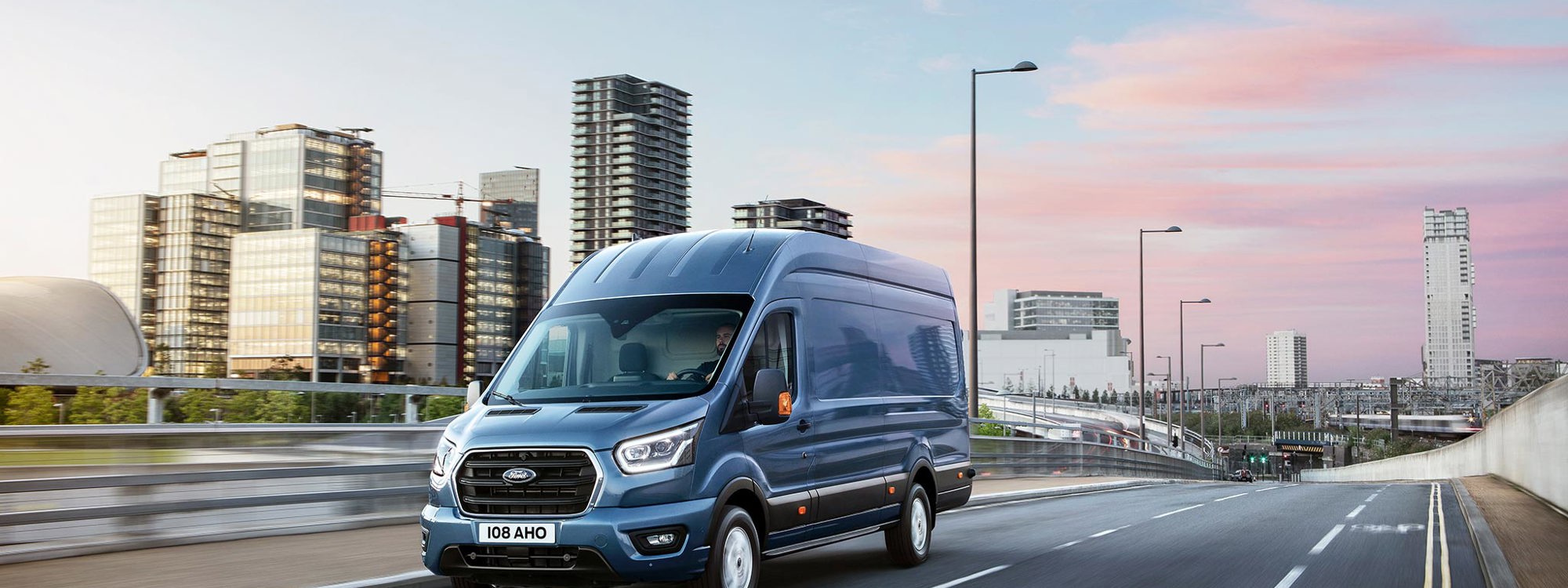
Lightening the load: composites innovation for a cleaner, greener Ford Transit
To stay competitive, the Ford Transit van has continued to evolve – delivering ever greater payload capacity and lower fuel consumption. As the 2030 net zero emission target for new cars and vans draws closer, this challenge is even more pressing.
Engineering innovation needs to deliver more efficient commercial vehicles that are ‘clean and green’ and affordable to own and run.
Challenge
To meet the 2030 target, the industry is shifting to alternative power sources, such as electric and hydrogen based powertrains. Each of these pose a weight gain issue for vehicles, setting the challenge to manufacturers to deliver performance whilst maintaining carrying capacity. Any loss in capacity impacts fleet size and for fleet owners, more vehicles means additional costs of manpower, fuel and maintenance. Being able to switch to EV without impacting fleet size, ultimately strengthens their business case for electrification.
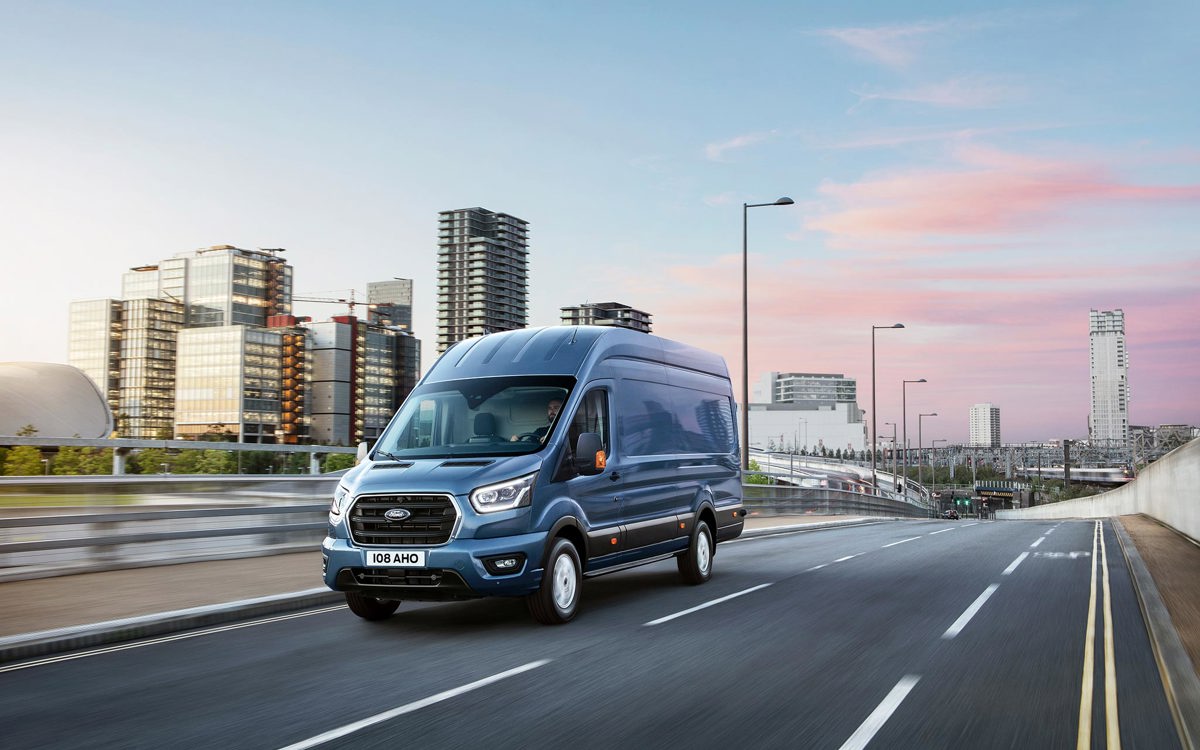
The weight of the vehicle base is critical to optimising its performance. Fully loaded, the current Ford Transit van has up to a two-and-a-half-ton payload capacity in a five-ton GVM configuration. Provided it did not compromise on strength or durability, reducing the mass of this base would increase the amount of cargo weight the Transit van could carry. It would also improve the fuel economy and reduce impact on the environment. Using alternative powertrains such as electric vehicles also enables operators to access clean air zones within inner city areas. This means they can complete their journeys without having to switch to a different, cleaner vehicle that is permitted within those zones.
Ford set the challenge of reducing the weight of three suspension components by 40%, equivalent to 27kg, whilst also meeting the cost, production rate and performance characteristics of existing components. New designs, materials, and manufacturing processes would be needed to reach a full global production rate of around 500,000 vehicles per year and meet a sub five-minute cycle time.
The project
The CHASSIS project (Composite Hybrid Automotive Suspension System Innovative Structures) led by a team at Ford Motor Company, Dunton, in partnership with Gestamp Chassis, the National Composites Centre (NCC) and the University of Nottingham, set out to investigate and test hybrid composite solutions using metal, carbon fibre and glass fibre, assessing them for weight saving, reduced CO2 emissions and performance benefits. The three-year, £2.5m research and development project, part-funded by Innovate UK, also looked at how the total number of parts used across the full Transit van chassis might be reduced, simplifying the bill of materials for the vehicle and making it easier to schedule the parts to the manufacturing line. This reduces complexity, points of failure and the time required to assemble.
The team identified three components within the suspension system as ideal candidates for further weight reduction: the Front Subframe, the Front Lower Control Arm (FLCA) and the Rear Deadbeam Axle with a focus on harnessing the potential of advanced composites to deliver a considerable reduction in mass, whilst offering new design flexibility. The NCC team worked on the FLCA and Deadbeam components.
Composite design engineering innovation
New design-thinking was vital to delivering the required step-change. Led from Gestamp’s UK R&D Centre, computer-aided engineering (CAE) and topology techniques that had been used in existing chassis product development were utilised to re-design the three components. The optimisation approach was further
evolved as part of the project, determining the composite material lay-up, as well as the hybrid material selection and joining techniques. Simulations helped the team navigate the vast number of possible configurations of fibre orientations, material properties and structural adhesives, to enable predictive analysis of the design concepts to enable a safer and lighter vehicle.
Front Lower Control Arm (FLCA)
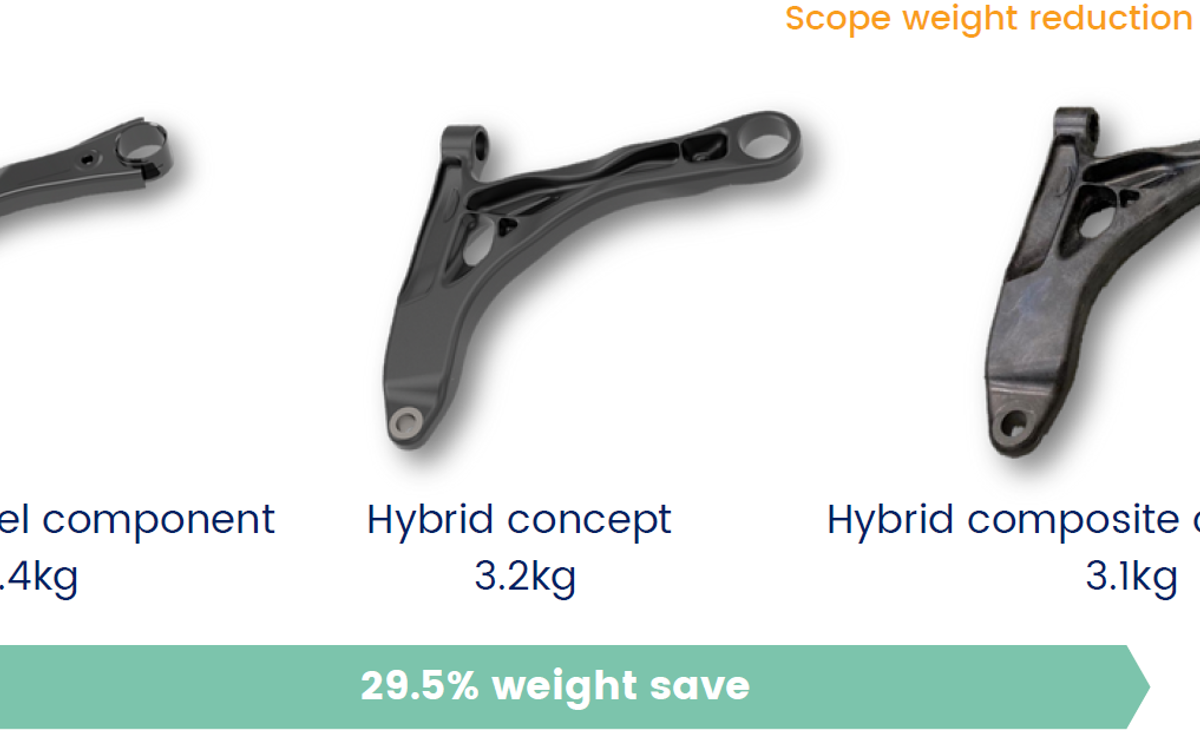
The FLCA component was designed by Gestamp, with input from the NCC for composite and production guidance and manufactured at the NCC’s Bristol site.
The new design, patented by Gestamp, was based on a two-step manufacturing process that would achieve the wall thickness required by the mechanical performance of the component. As a first step, the NCC team manufactured a long, glass-fibre reinforced thermoplastic core with a forged steel insert. In the second step, this moulded core was over-moulded with a carbon fibre shell to create the finished piece.
NCC specialists used digital process simulation to enable virtual manufacturing. This, in turn, informed the tool design as well as de-risking and optimising the manufacturing process and manufacturing trials provided further opportunities to check and refine the approach.
To design and manufacture the two injection mould tools, the NCC worked with Advanced Tooling Systems. To ensure the bonding at the polymer and metal interface, the metallic inserts were coated by Evonik using their Vestamelt Hylink adhesion promoter. All the materials for injection moulding were supplied by EMS-Grivory in Stafford.
Rear Deadbeam Axle
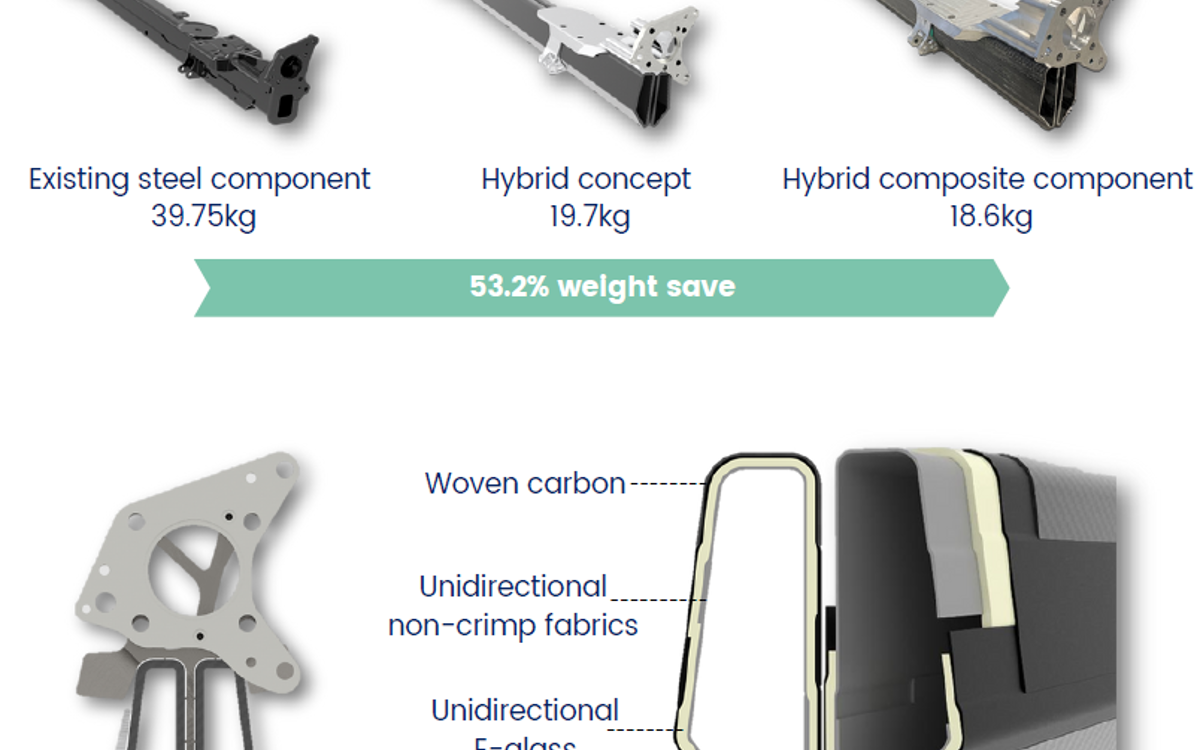
Gestamp’s patented design concept utilised a composite beam supporting extruded aluminium wheel mount and the NCC worked with Gestamp to ensure the composite design was achievable, manufacturable and could be delivered on time. It also collaborated on the design while being responsible for materials selection, sourcing and supply.
The new Deadbeam was made using a pultrusion process, a manufacturing technique never attempted before on a component of this kind: glass roving fibre, carbon fibre non-crimp fabrics and woven fabrics were simultaneously pulled through a resin bath to create a new material, which was then automatically cured in a die-cast tool. The composite fibre materials were provided by Cristex Composite Materials and the tool was developed by Pultrex, which also manufactured the beams with support from the NCC. The complete Deadbeam assembly was then built-up at the University of Nottingham.
Results
All three demonstrator components were tested at the Gestamp Chassis R&D Centre, using Ford’s full design verification plan. In addition, the front subframe and rear deadbeam were also sent for vehicle testing on a Ford transit at the Lommel proving ground.
Whilst the FLCA component is ground-breaking in design, the team decided that the manufacturing processes needed further investigation to meet performance requirements. The Deadbeam was successfully vehicle and rig tested and the team is looking at the cost-weight ratio scenario to continuously improve manufacturability.
Overall, the team proved that using a composite design can enable part consolidation (a reduction in the number of component elements), reducing this by 56%, and, in turn reduce manufacturing and assembly operations, with their associated cost, to deliver sub five-minute manufacturing cycle times for both components.
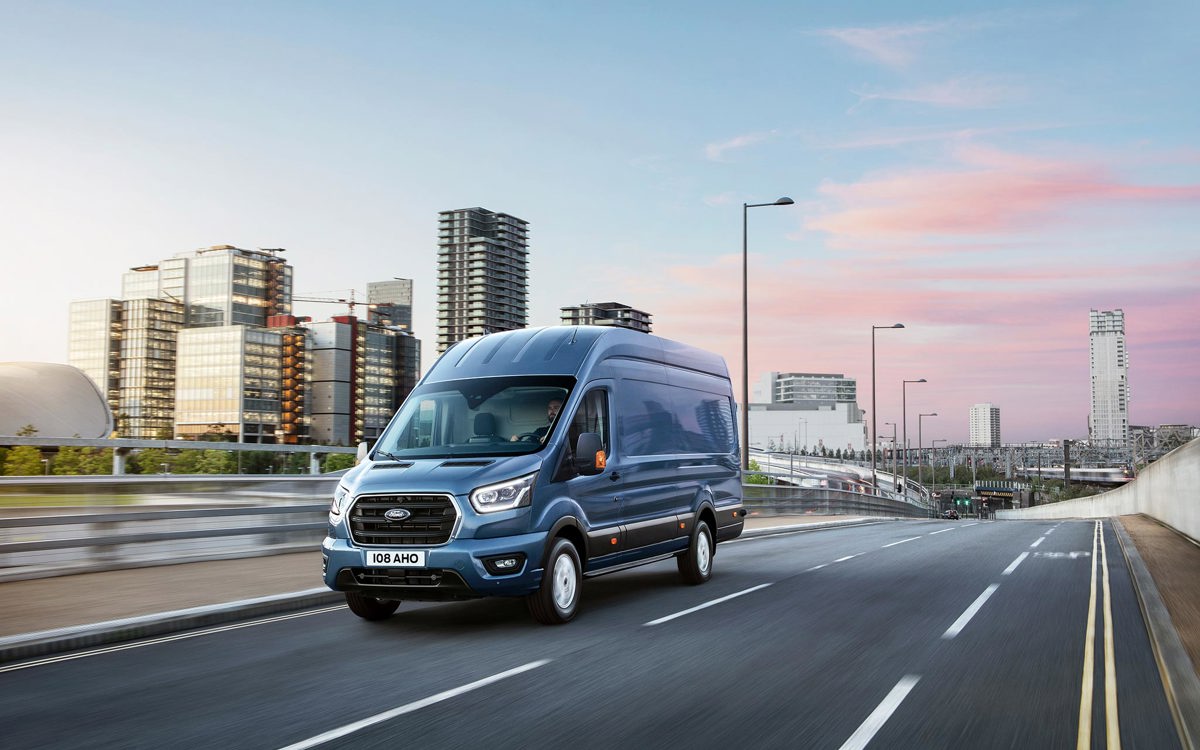
Sustainability integral to the design
The new components were put through life cycle analysis, based on a hypothetical five-year period and an annual mileage of 17,000. The results showed that the weight reduction would deliver a cumulative CO2 saving breakeven time of just 1.76 years for CO2 output; with the subframe, lower control arm and deadbeam breaking even in 3.35 years, 1.3 years and 0.65 years respectively.
There are concerns over the use of composites in vehicle manufacture, in particular, their end of life ‘recyclability’. The team wanted to address this as part of the CHASSIS project activities so looked at using technologies such as disbondable adhesives. The resin and fibres used in the Deadbeam could be reclaimed using the B&M Longworth DEECOM® process, providing a route to recycling and reuse to help meet vehicle recycling targets and legislation.
Industrial relevance
The CHASSIS project demonstrated that composite and hybrid multi-material components can be used to realise significant weight savings, while meeting the rate and performance requirements of Ford’s Transit, and at affordable cost. A part weight reduction of 32.3kg or 46% on a long-established product model is significant.
During the project, the consortium also developed significant experience in the design and manufacture of long fibre-injection moulded and over-moulded thermoplastic components, which can be applied to future projects. The National Composites Centre continues to develop its Overmoulding and Pultrusion technology offering through its capability development work.
The patented designs from Gestamp Chassis won the project consortium team the Composites UK – Innovation in Composite Design award in 2020 and the project was a finalist in the JEC innovation awards 2021.