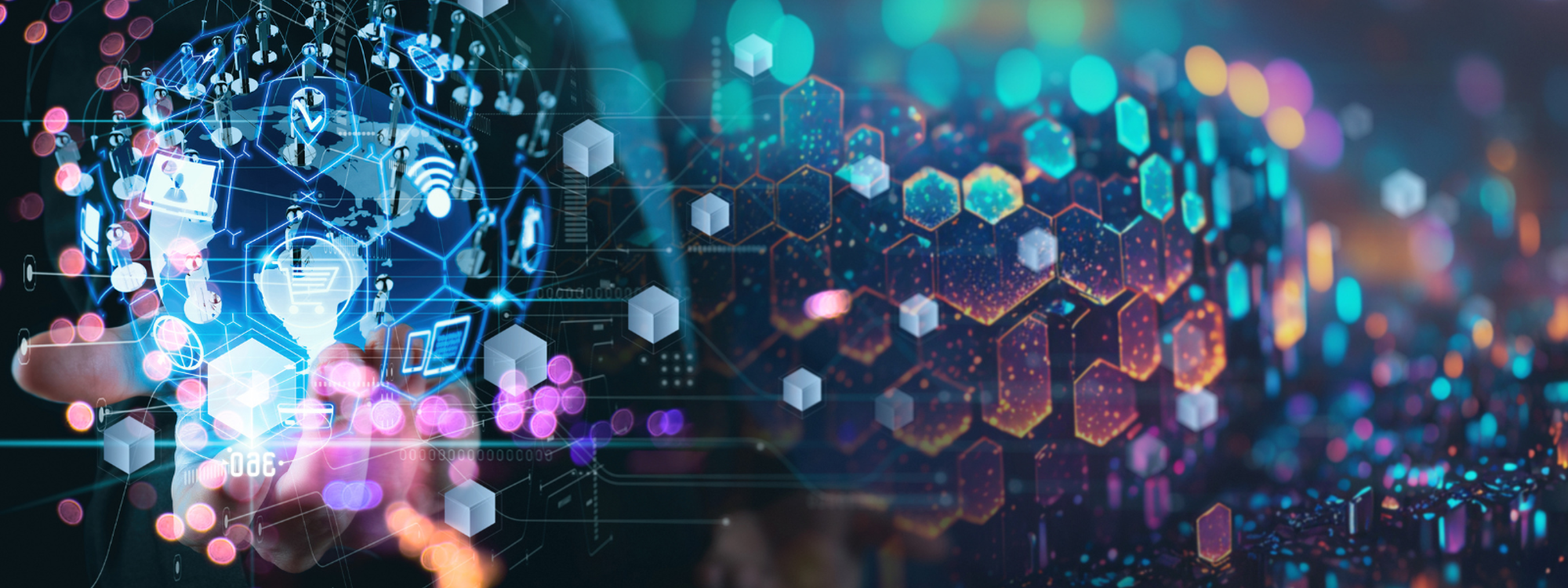
Optimising the design of a composite hydrogen pressure vessel
To gain competitive advantage in a global marketplace, it is crucial for companies to digitalise processes to reduce development timelines and maintain engineering leadership. For digital engineering, the use of Multi-Disciplinary Optimisation (MDO) techniques offer industry a new approach to product development, redesigning and remaking products with a focus on net-zero.
Challenge
Product design is the process of identifying and defining a combination of features that satisfies a set of requirements. These requirements often include competing objectives and constraints, and address different aspects of the product and its parts.
Traditional engineering tends to be sequential, but the complex nature of most products calls for a concurrent approach to be addressed which MDO can offer.
MDO is the process of finding the optimal solution to a set of design requirements that encompass multiple disciplines; from structures to manufacturing, operations, disposal, economic considerations, etc. The concept of MDO is particularly suited for products or systems made up of multiple coupled parts that cannot be designed and optimised in isolation.
Results and the digital opportunity
The advantage of MDO is that its goal is to address all design elements of a product at the same time, resulting in superior design, lower development costs, faster new product introduction, and the ability to refine specific features. It is a tool that could present a notable transformation in the competitive edge of British industry.
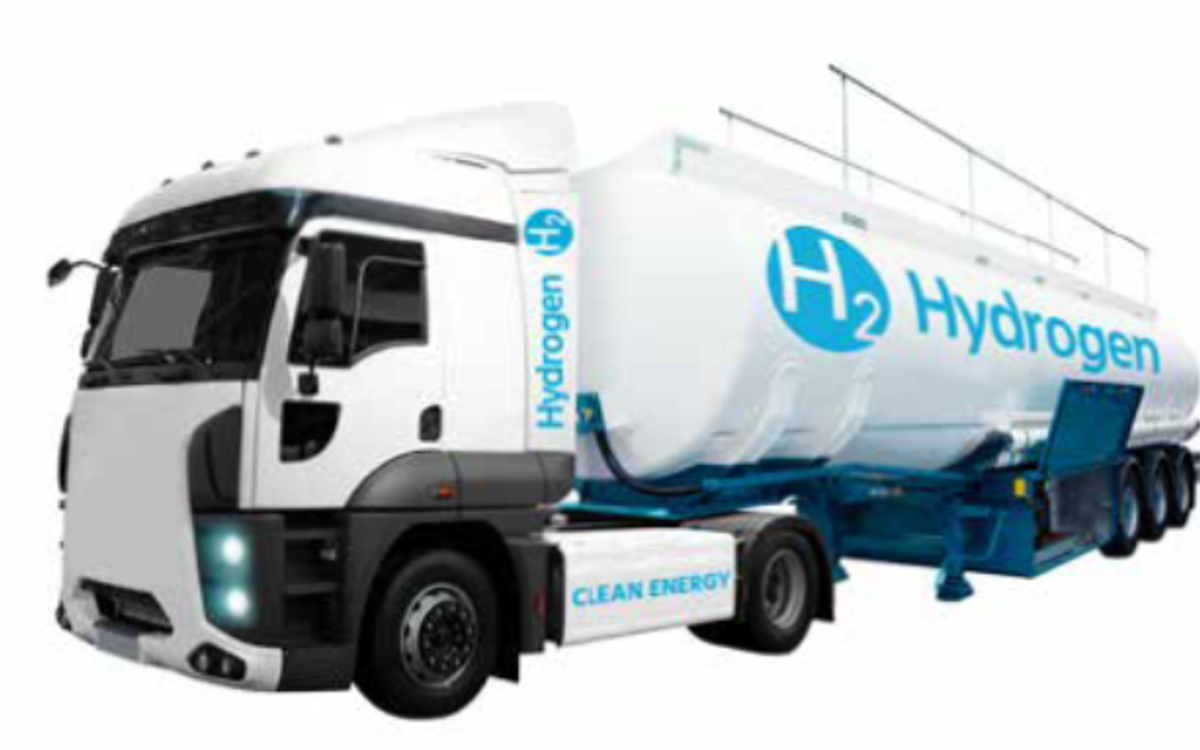
Case study
Background
As hydrogen has emerged as one of the most promising solutions for achieving net-zero carbon emissions by 2050, the design of pressure vessels for transport and storage has been drawing increasing interest within industry.
For this project, MDO has been applied to the design of a Type IV composite hydrogen pressure vessel, exploiting the benefits that digital design technologies can enable.
Challenge
The design of composite pressure vessels is based on four main aspects: structural performance, manufacturing, weight, and cost. Among the constraints, the design must meet a minimum burst pressure, a minimum fatigue life, and a maximum permeance rate, typically prescribed by regulatory codes. Design objectives include maximising the hydrogen to tank weight ratio and minimising the cost to make the product competitive in the marketplace. The sustainability potential of materials and manufacturing processes used should also be considered early in the design process.
Following an aspect-based review of the system, setup of the pressure vessel MDO involved the identification of the analysis modules and software tools required to evaluate the product performance against constraints and was used to map the relationship, or coupling, between the analysis modules and support the definition of a process flow for the optimisation of the pressure vessel.
Innovation
A design space optimisation platform which enables the exploration of different design alternatives was used to conduct the MDO exercise. Previous research undertaken within the DETI programme involved the assessment of a range of commercial industry software available. HEEDS™ MDO, a design space exploration and optimisation software from the Simcenter™ portfolio produced by Siemens Digital Industries Software, was the platform selected for the implementation of this MDO process.
Results
Fifty designs were evaluated in less than two hours and an optimal solution was discovered among twenty-three feasible designs. It is worth noting that a traditional design approach typically leads to a feasible design, which is not necessarily the optimum one. Further effort can be required to identify the optimum design. Finding the optimum design of a complex system such as a composite hydrogen pressure vessel was the goal of this proof-of-concept MDO study. Automating the design process identified the optimum design to be estimated at five times faster than a traditional approach. This achieved the goal and significantly reduced the risk of human error in the process of data transfer.
Impact
With the UK looking to position itself as a hub for agile, hightech manufacturing, MDO presents an enormous opportunity to substantially improve product design, development, and manufacturing time to market.
The National Composites Centre (NCC) is advancing the knowledge required to establish a dynamic UK supply chain, investing in hydrogen pressure vessel research and development to seed manufacture in the UK. This progression in technology will help it to remain competitive in the future. It is also part of the High Value Manufacturing (HVM) cross-Catapult Hydrogen Innovation Initiative (HII).
This collaboration brings together the strengths and capabilities of the Catapult innovation centres to support growth in the UK hydrogen supply chain, overcome technology and integration challenges, and to establish an effective UK hydrogen infrastructure.
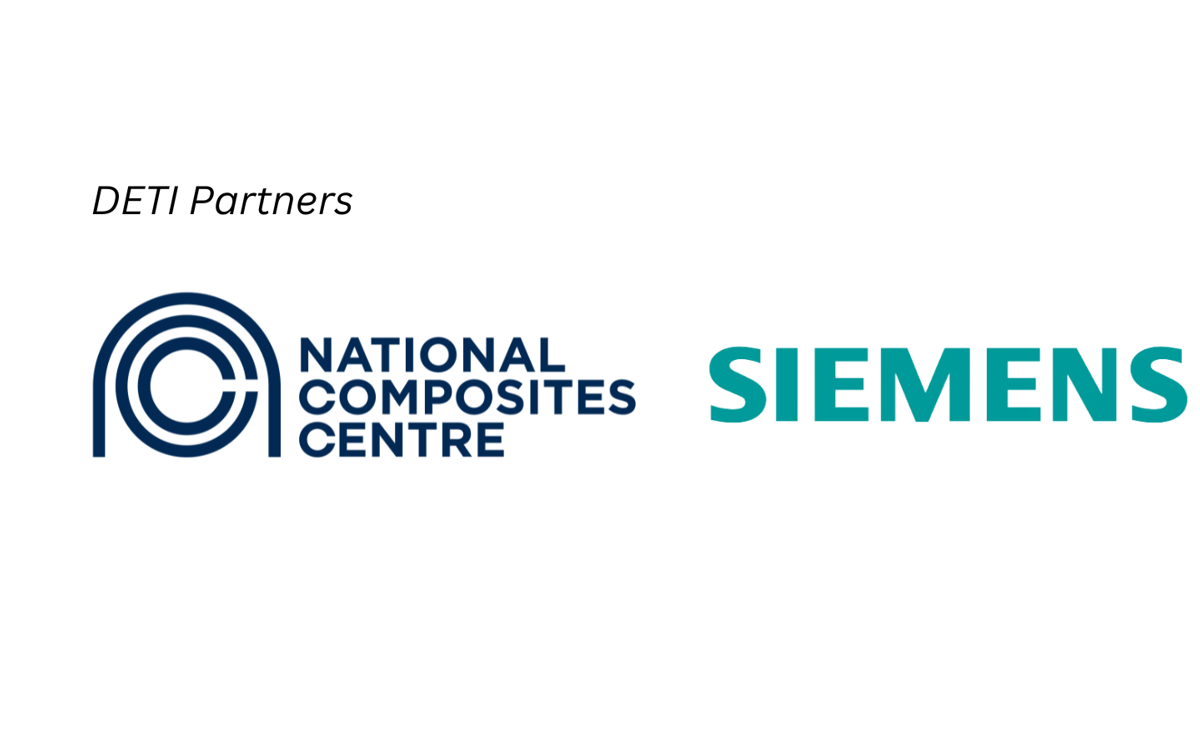