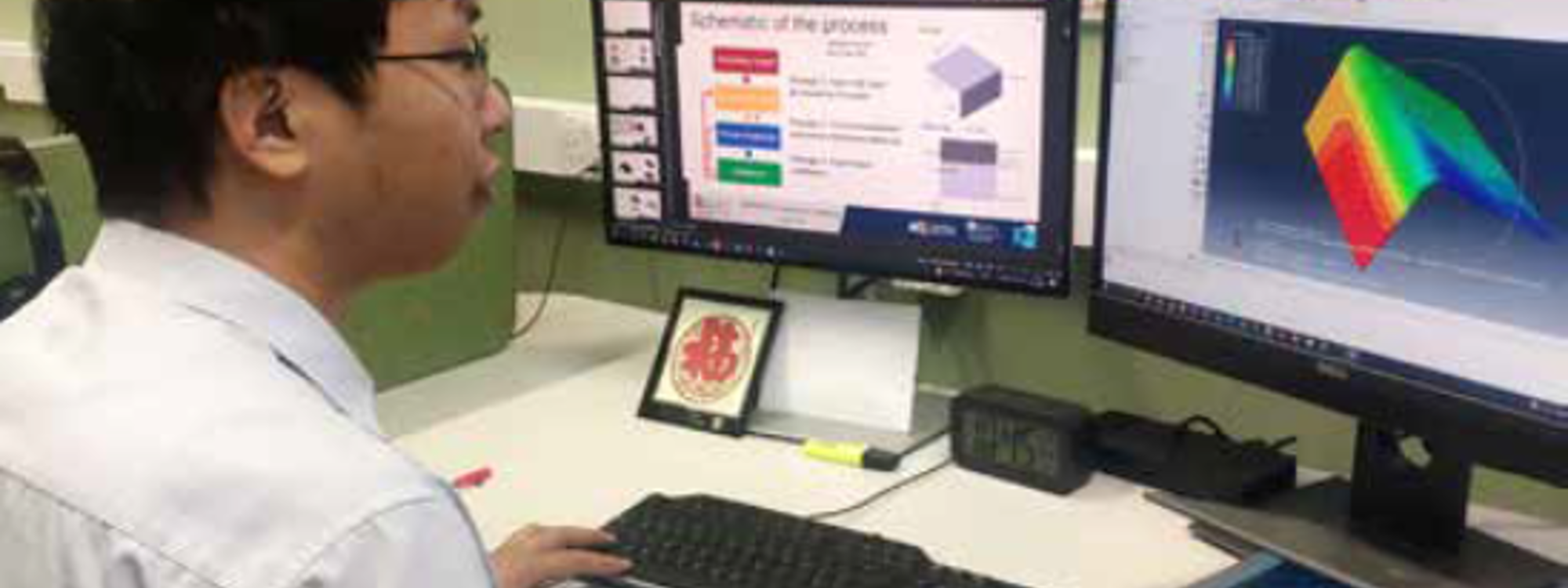
Developing efficient modelling of manufacturing capabilities
The deployment of manufacturing simulation tools within composites is critical in reducing composite parts costs and in helping a greater range of industries access composites products and utilise their engineering benefits. Accuracy of the predictions and speed of the simulations are the two main challenges for greater use of simulations in the design and manufacturing cycle of a composite part.
Challenge
Currently, design and manufacturing of composite components is expensive and time consuming. A major impediment of current practices is that very few simulations are used in manufacturing cycles, with extensive physical trials still being the state-of-the-art.
Results and the digital opportunity
The Bristol Composites Institute at the University of Bristol has developed a simulation tool that provides uniquely fast, and accurate simulations for the manufacturing of composite components. The simulation tool is able to give an accurate prediction of the final thickness of the part and the formation of defects from the production process at a laboratory scale, effectively reducing waste, energy and carbon emissions.
An automated piece of software for the prediction of thickness and production induced defects in composite parts has also been developed as part of the project. A physical demonstrator of industrial size and complexity was used to assess the accuracy of the software tool. Results highlighted the accuracy of the software tool in predicting the quality of the demonstrator part.
An automated tool allowing for optimisation of the tooling for increased part quality has also been developed.
The simulation model process is entirely automated, which allows users with only a cursory knowledge of the complex mathematical models behind the software to be able to use it. A completely automated workflow for composite tooling design has also been developed.
The automated simulation tools developed are available for industry use from the University of Bristol and the National Composites Centre, which results in significant cost savings per part by suppressing one full design cycle.
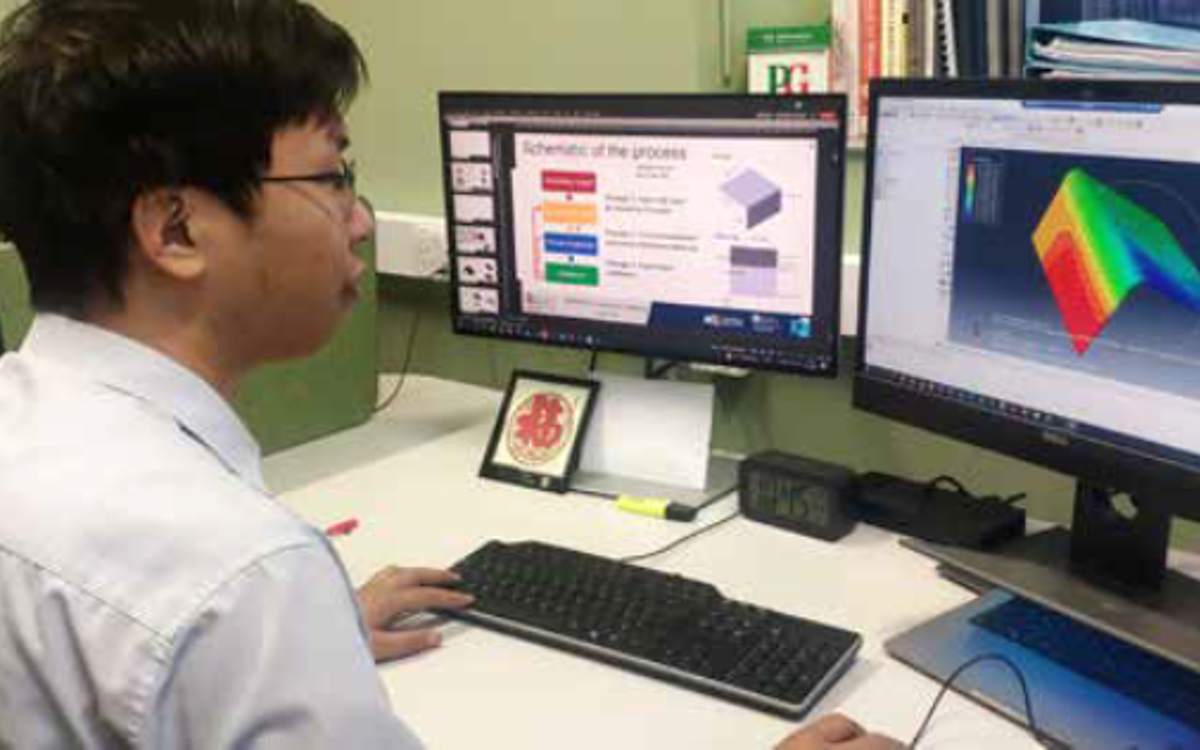
To access the simulation tools and discuss your requirements, email [email protected] or [email protected]
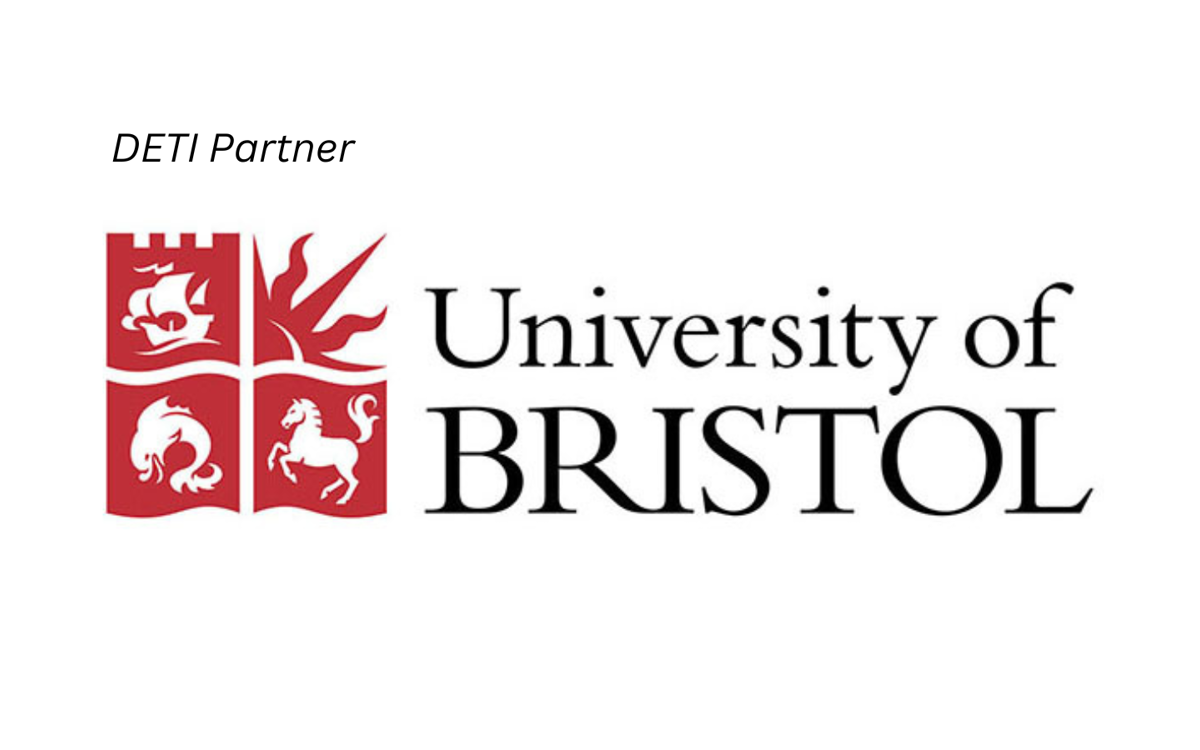