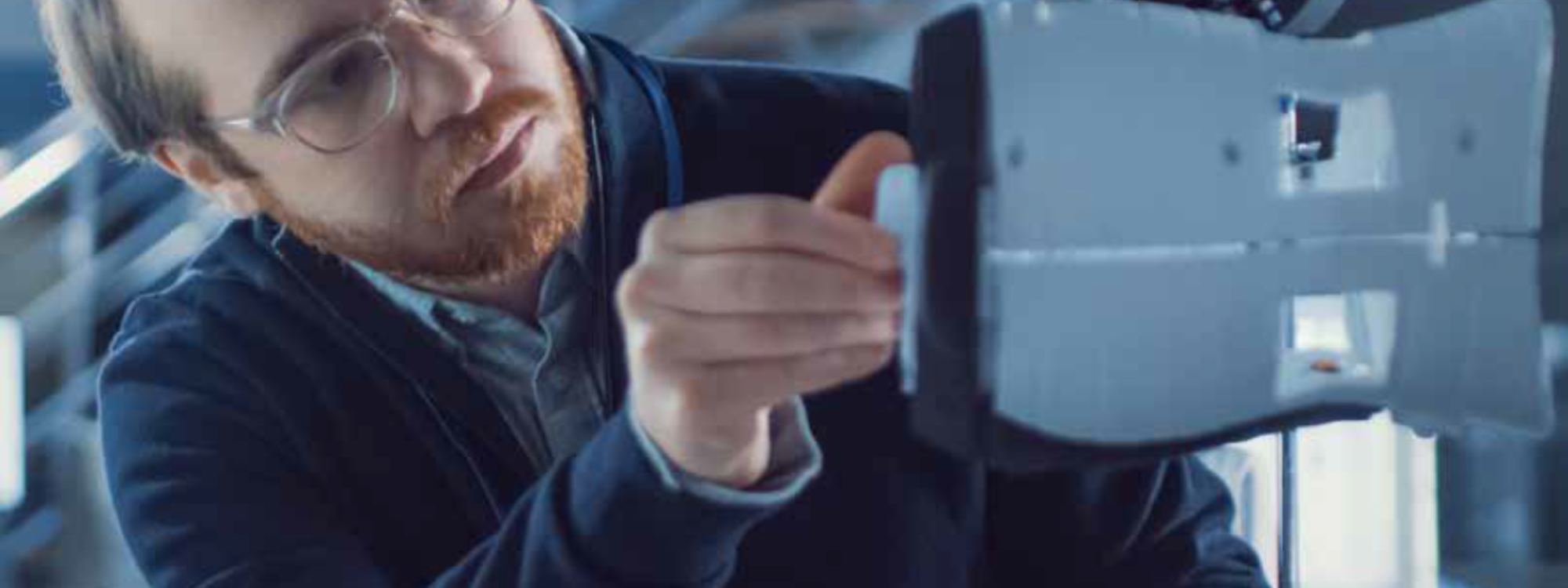
Exploring how servitisation could unlock profits for South West manufacturers
Servitisation has huge profit potential for sectors like manufacturing. It can involve a transformation of the manufacturer from a business which is focused on building revenues around the production and sale of products, to one where a significant, sustainable revenue stream comes from services that focus on the outcome from the use of its products.
Challenge
In the face of changes in consumer behaviour and an increasingly volatile socio-economic climate, the UK manufacturing industry has witnessed a rise in servitisation-based business models, with a 2020 report stating that 78% of manufacturers were either developing, or are already offering, services as an alternate revenue stream. However, uptake in the UK is not as widespread as it could be, meaning viable opportunities to accelerate economic growth are not being grasped. In particular, servitisation could be key to unlocking regional growth, such as in the South West of England and Wales – an area rich in manufacturing sub-sectors including aerospace and defence.
Results and the digital opportunity
As part of DETI, Digital Catapult produced a report exploring the business case for servitisation to UK industry - particularly in the West of England - as well as unpicking the current challenges preventing manufacturers from reaping the benefits.
The report looks at how servitisation could play an important role in the post-COVID-19 regional economy, and how it has already shown potential for industries including aerospace, rail, heavy equipment and car rental.
Looking at a real-life example: an organisation called AE Aerospace in Birmingham – which specialises in the manufacture of precision machine components – has been assessing how a ‘manufacturing-by-the-hour’ service could help to differentiate from competitors. Since AE’s core activity revolves around traditional machining, they have integrated services on machine metal components into their offering. As a result of this new service, turnover has moved from £2.8m to £5m since 2016.
Elsewhere, the report examines skills gaps as a barrier to servitisation taking full-flight, looking at how manufacturers can look at upskilling existing employees – amongst whom a knowledge gap is likely to exist in the area of digital and programming skills, alongside hesitancy to work with unfamiliar technologies such as high-tech machines and automation.
Applying valuable learnings from the Advanced Services Group, the report looks at the benefits of targeted, regional interventions. Following servitisation successes in the West Midlands – a region with a proud industrial history – the South West of England and South Wales could stand to benefit significantly, given its specialism in transport and aerospace. Potential interventions examined in the report include the option of a ‘best-practice’, physical centre of excellence for servitisation.
Underpinning the report, a servitisation Proof of Concept (PoC) has also been produced to demonstrate the key digital components that can bring a servitisation business model to life. Through a rapid prototyping approach, the PoC demystifies the range of technology options available, by showcasing a best practice approach to developing ‘connected’ products.
It also explores the provision of the ‘manufacturing cell’ as a service. This will open up opportunities for new, servitisation-based digital business models, by providing visibility of carbon cost across the supply chain. In the long-term, this could mean a boiler manufacturer monitoring the energy efficiency of a boiler and providing this information, as well as any services linked to this, direct to the customer.
The five key takeaways from the report:
- Servitisation could play a significant role in propelling regional growth, with a notable presence from manufacturing and high value engineering businesses
- Servitisation could help manufacturers build stronger long-term relationships with customers, from a one-time, completed transaction, to a series of regular interactions
- Digitisation and IoT will play a significant role because servitisation of a product or service requires precise sensing of certain indices, including around usage and asset condition
- Skills gaps are getting in the way, and are a major barrier to servitisation in the UK manufacturing sector. This is because the process of transforming to a product-service system requires both organisational and management capacities in a different manner to those required for product-oriented logic
- Targeted, regional interventions could play a crucial role in helping organisations respond to increased societal appetite for services by adopting servitisation business models
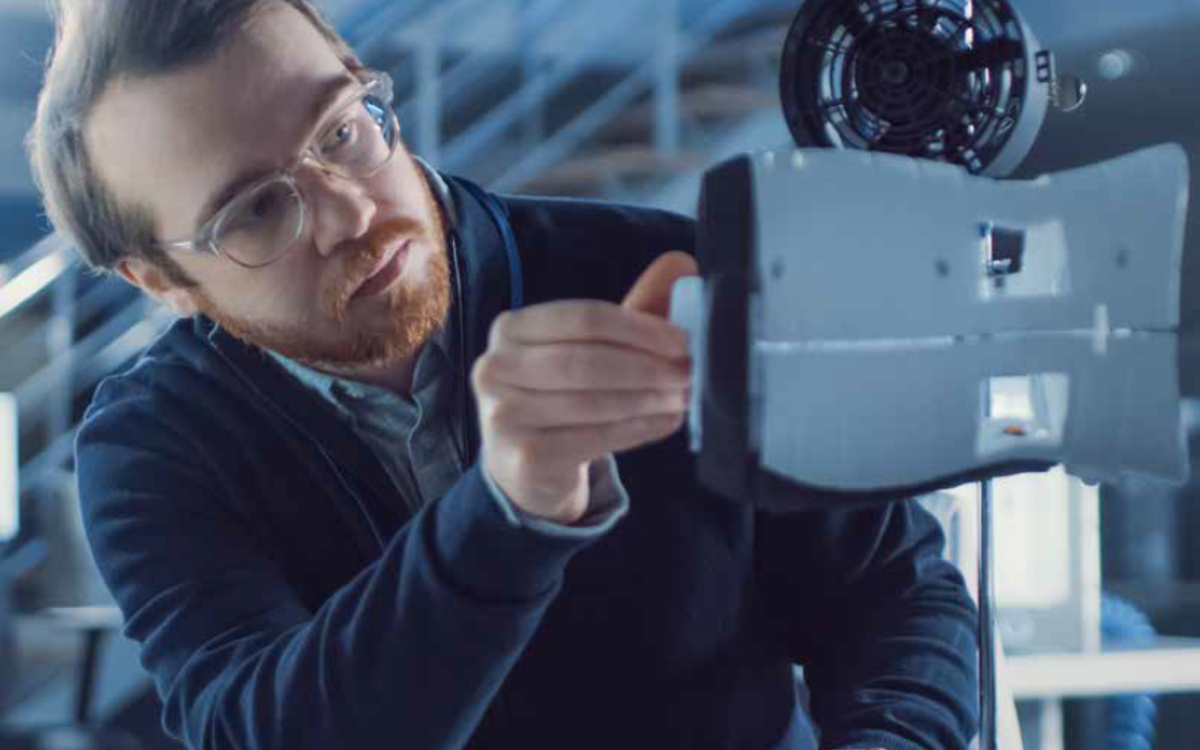
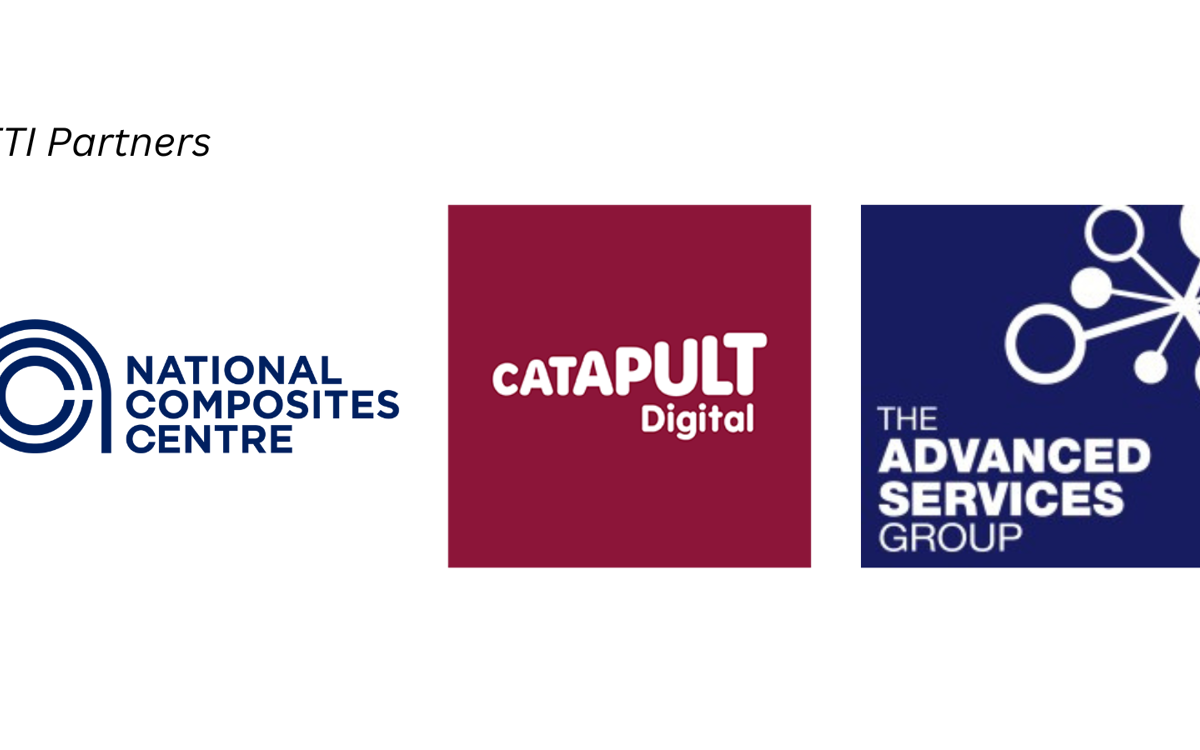