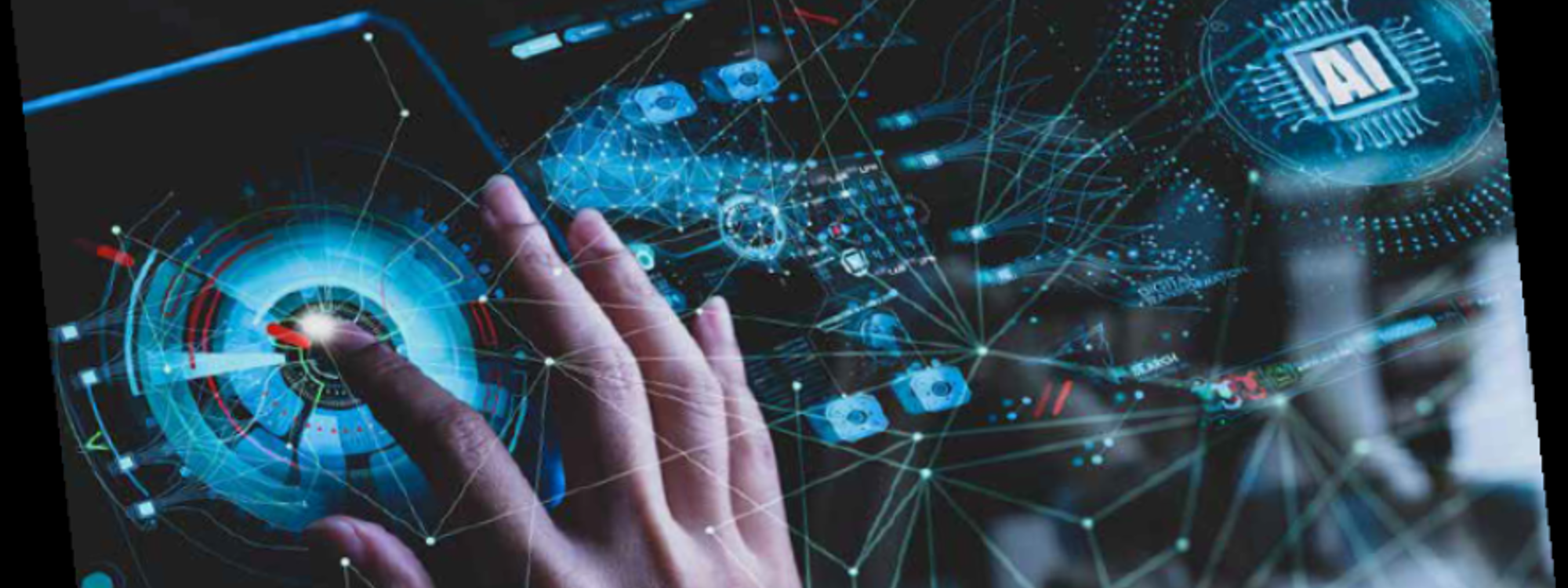
Developing an immersive operations environment for manual tasks
For companies that are starting out on their digital transformation journey, a lack of automation can appear a barrier. Integrating and automating technologies to undertake manual tasks and processes offers many benefits. Supporting manufacturing workforces to use advanced digital technologies in these scenarios enables agility, flexibility and a competitive lead.
Challenge
Visualisation and immersive technologies provide new opportunities to present data on design and manufacturing processes, maintenance, and in training scenarios to users in manufacturing.
They will enable industry to create better sustainable products in safer and more efficient environments, requiring less prototypes, developed in a shorter timescale, with reduced cost and waste.
Results and the digital opportunity
Visualisation technologies such as AR and VR, make it possible to realistically re-create natural or real environments that occur in industrial processes, such as those used in composites.
The ability to move seamlessly from different ‘realities’ or technologies enables a design, build, maintain and decommission, end-to-end process.
- Augmented Reality (AR) is the integration of digital information with the user's real environment in real time. Unlike virtual reality, which creates a totally artificial environment, augmented reality uses the existing environment (the real world) and overlays new information on top of it
- Virtual reality (VR) is an artificial environment that is created with software and presented to the user in such a way that the user suspends belief and accepts it as a real environment
The National Composites Centre (NCC) has produced systems to support operators who undertake manual, flexible tasks in the manufacture of composite parts. These systems focus on the physical process of layup, bagging and cure preparation for composites. This enables an increase in part consistency, a reduction in the volume of parts needing rework and the ability to predict failures earlier in the process, reducing the cost impact of errors. The systems consist of:
- An Augmented Reality (AR) solution to inform, guide and provide feedback to an operator during manual manufacturing processes
- Artificial Intelligence (AI) – Machine Learning (ML) verification systems that validate and check the processes undertaken by the operator meet the required standards
The systems are setup as a deployable test bed and can demonstrate a range of use cases and specific customer case studies within composites manufacturing:
- A software framework hub manages operator guidance, verification and tool/part/device position referencing. It interacts with and gathers data from existing data sources using the latest Model Based Systems methodology
- Includes a built-in capability to deploy immersive output on to multiple device types like workbenches, wearable headsets and tablets
- Offers a verification capability to ensure the process operations are executed within the tolerance values required for task delivery
- Operator validation will oversee the starting and completion of tasks, to ensure the process operation is being followed
- Interacts with existing systems to gather data required to instruct and guide an operator during composite layup
Organisations interested in accessing the test bed can contact the NCC to arrange a demonstration via [email protected]
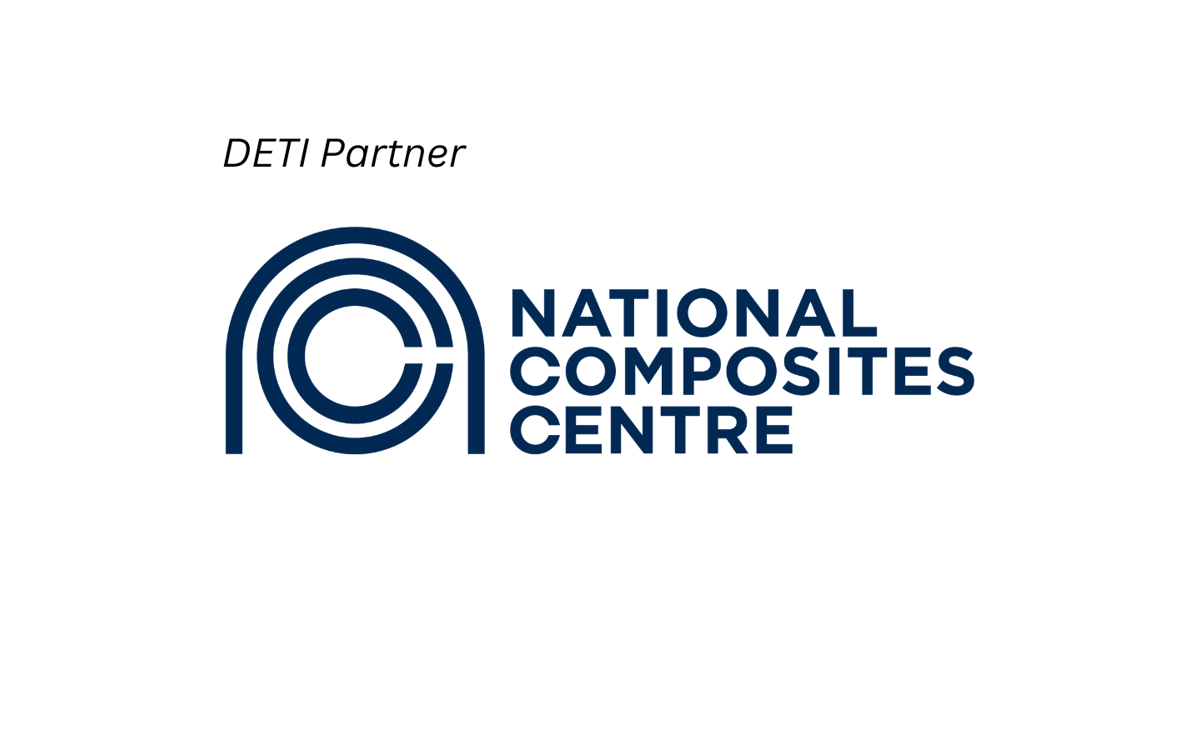