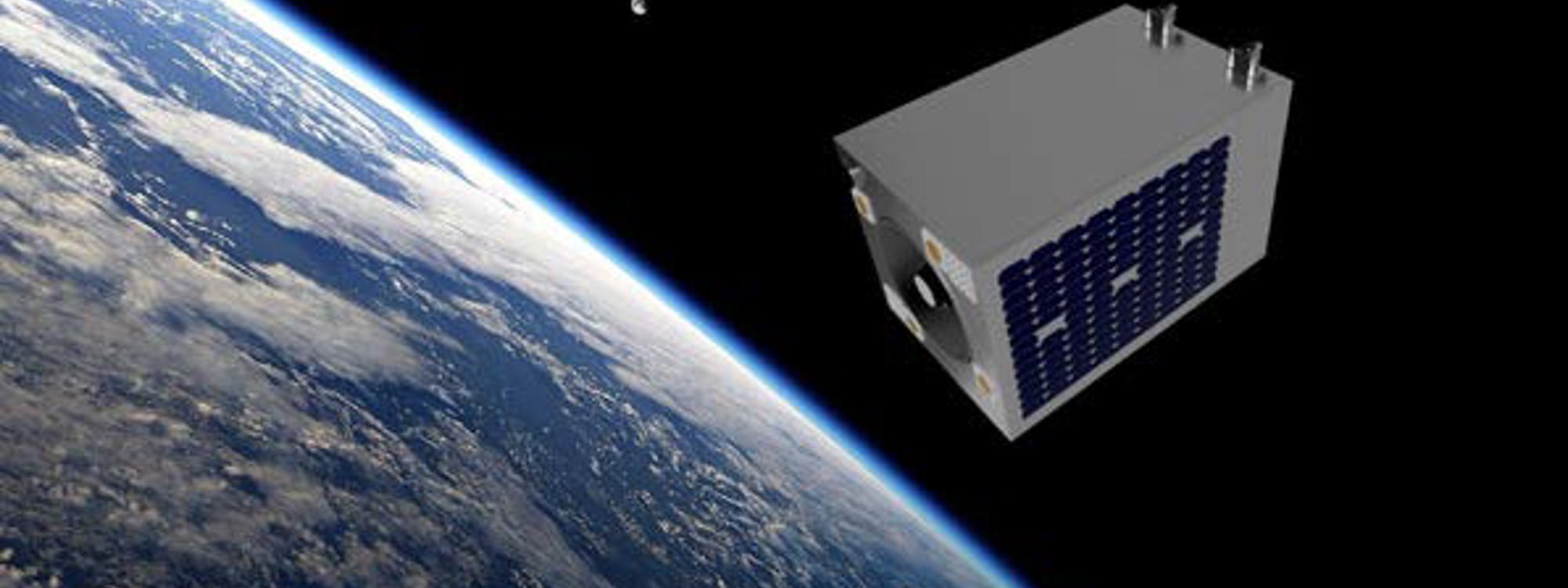
Optimising satellite design with digital engineering
Challenge
Digital engineering technologies and tools offer a new approach to the design process for complex, high value products from aerospace to automotive, defence and transport.
Offering opportunities to digitalise processes to reduce product development timelines and maintain engineering leadership, they provide the opportunity to review traditional design methods that require multiple design iterations and physical prototypes.
Satellite design has always been a lengthy and costly process. Traditional design methods require multiple design iterations and physical prototyping which can quickly become unaffordable for many companies. By using digital engineering there is a great opportunity to review and modify the traditional methods eliminating the need for individual build and test runs ultimately making the design process faster, more accessible and affordable.
Results and the digital opportunity
As part of its work with small to medium enterprises for DETI, CFMS has helped KISPE Space to examine and develop the methods using digital tools, applicable to the Open Source Satellite (OSSAT) structural design.
The aim of the project was to reduce a key driver in the cost of satellite production: the “touch time” or labour costs spent on designing, building and testing a satellite. KISPE Space is a programme execution and systems engineering company operating within the space sector.
KISPE Space’s vision is to use the same satellite structure on different missions and with different launch vehicles. The structure had to be optimised to avoid adding unnecessary mass to the satellite, which would increase the launch cost.
With such a variety of often conflicting requirements, conventional design methods require physical prototypes and repeated design iterations. As a result, the traditional design process is lengthy, consumes materials and resources, and demands significant funding.
To address the challenge, CFMS generated a range of solutions using a generative design optimisation approach. This used digital engineering tools and methods to create multiple designs, virtually tested against performance criteria. By automating this process using Multi-Objective Optimisation (MOO), coupled with high performance computing, an optimised satellite structure is created faster. The process starts with the creation of an inventory of satellite components and their key parameters (size, mass etc).
With these components, a model of the satellite is constructed in an automated way and with minimum input requirements from a human operator. This allows for a dramatic reduction of design time for any future mission requirements. The process of optimisation is conducted algorithmically by varying the geometry (thickness, positions) of the structural elements, the manufacturing methods and materials used to make the structure, and the overall layout of components within the satellite.
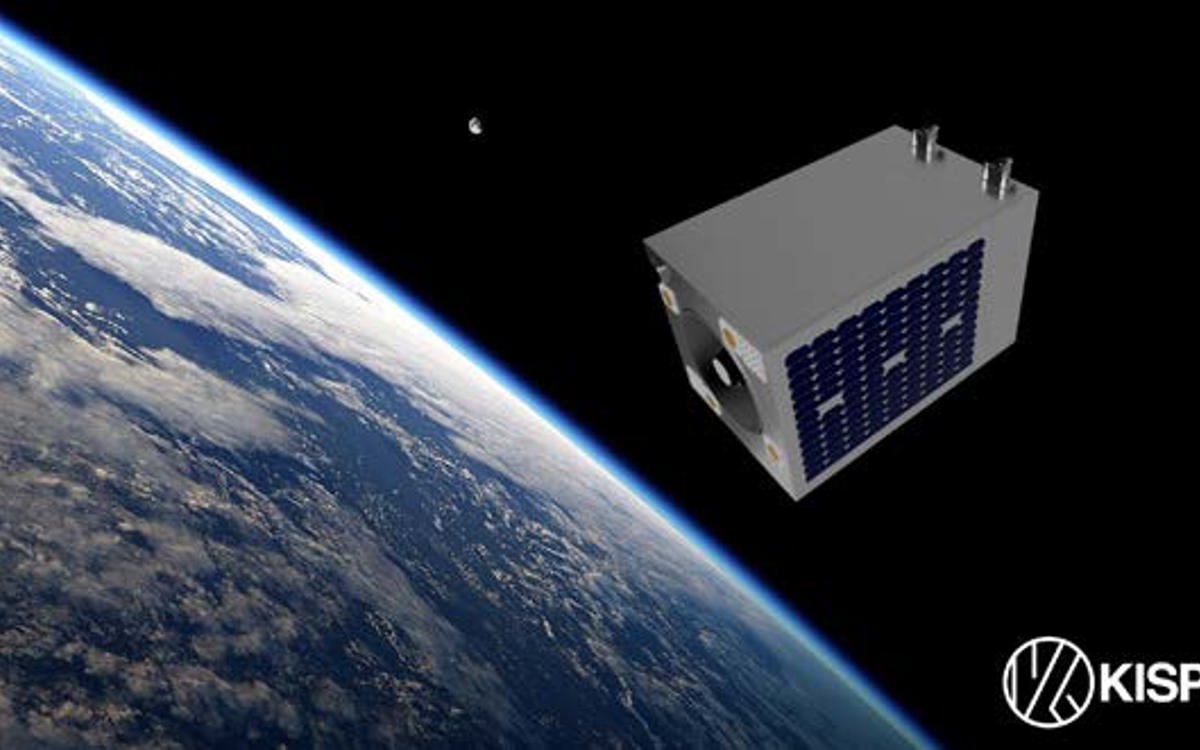
The vast array of models created were tested against key environmental conditions, such as vibration and the forces experienced during launch, restrictions applied to centre of gravity and total mass, etc. The end result was a structural design that achieved the mission requirements.
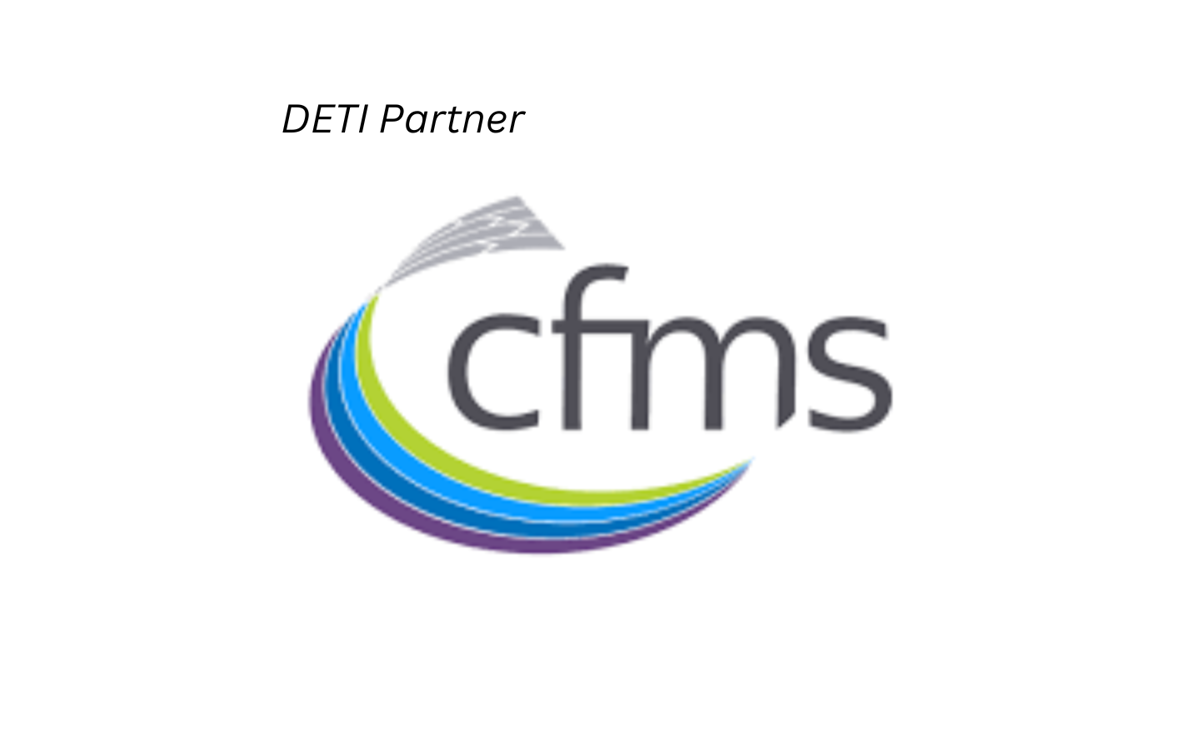