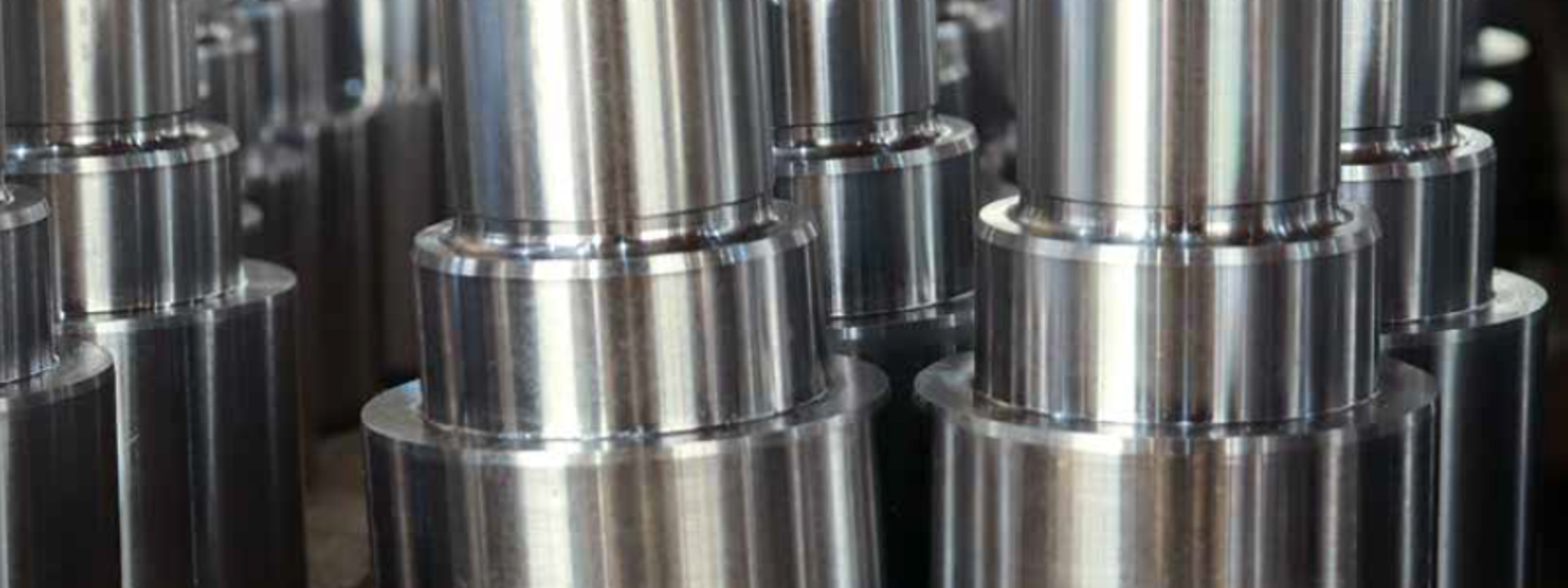
Transforming manufacturing using Self-Adaptive Manufacturing Processes (SAMP)
Manufacturing in the UK is seeing new and significant challenges, sustainability demands (captured by Net Zero initiatives), recovering from the COVID-19 pandemic, BREXIT, energy prices and the continuing rapidly evolving competitiveness from global markets.
Ultimately these challenges are applying new levels of pressure on the UK engineering and manufacturing sector, realised through ever increasing demands in the following areas:
- Cost per product challenges to remain competitive
- Efficiency of production to meet sustainability demands
- Efficient energy use, efficient use of raw materials (no or low waste), efficient use of the workforce
- Demand for new novel/higher performing products to remain ahead of competition
One of the ways to meet these demands is to develop higher-complexity manufacturing processes. With these types of processes becoming more prominent, ensuring manufacturing success is even more critical to avoid investment in producing parts that require rework or scrapping. In summary, there is a need to produce more right every-time manufacturing, on more challenging processes.
Results and the digital opportunity
What is SAMP?
Self-Adaptive Manufacturing Processes (SAMP) are processes that have been created to overcome manufacturing variation and deliver right every-time products. This is particularly pertinent to sustainability demands to reduce waste, energy and carbon emissions.
SAMP is a specific type of Digital Twin. The AMRC has completed significant work to clarify the definition of a digital twin: “A live digital coupling of the state of a physical asset or process to a virtual representation with a functional output."
How to enable SAMP
SAMP is enabled through the Digital Transformation of a given manufacturing process. For engineering and manufacturing, digitalisation means acquiring data from across the product development lifecycle, design to manufacture and through service to end of life, in order to make better product-related decisions and improvements and unlock new business-related opportunities. Digitalisation is now a viable route for a wide range of business improvements. Previously this wasn’t the case due to the expense and difficulty of deploying digital technologies. The growth of readily available digital technologies and an increase in collective understanding, and associated skills, means that these technologies can now be leveraged to achieve transformational changes in businesses.
To achieve SAMP, a traditional manufacturing process and its associated systems are:
- Digitally modified to provide the ability to acquire quality controlling process data in real-time
- Process data is used to assess whether the process is progressing/performing as it should be or not
- If the assessment raises a concern that the process isn’t progressing/performing as it should then the manufacturing process, automatically and in near real time, is sent commands to change its behaviour to steer the process to a successful outcome
The Benefits of SAMP
The ultimate benefit of SAMP is to produce right first-time manufacturing, and has the associated gains:
- Lower cost of production due to less scrap and rework
- Efficient production to meet sustainability demands
- All energy, raw materials and workforce effort is directed towards making products that go out the door first time rather than on scrap parts that do not see service
Case Study: Applying SAMP to Liquid Resin Infusion (LRI)
Liquid Resin Infusion (LRI) is a high value process used to create composite components and parts used in aerospace, marine and automotive sectors. A composite resin is injected into the manufacturing mould of a product or part. The technique is highly dependent on the skill of the operator, is very manual, and often produces high volumes of waste components when developing new parts. An energy intensive process, failures are not only expensive in terms of material, time, and cost but also emit higher carbon emissions.
As industry grows its use of LRI, there is a need to improve the process to enable parts to be made ‘right first time’ and ‘right every time’. In turn, this lowers the cost and time of developing new components and reduces the environmental impact of composite production by generating less waste. Improvements to LRI composite manufacturing can be achieved through data analysis and automation of the LRI process by the application of digital and 5G technologies.
Further utilising SAMP will reduce risk and dependency on operator skill of the LRI manufacturing process, developing a system that can automate elements of the process. In turn, process time and cost associated with developing new components, as well as their environmental impact, are minimised, enabling a number of key benefits:
- The automation element enables benefits such as labour cost savings and reduced process risk, each moving the LRI process in the direction of ‘right first time’ manufacturing
- Insight into the LRI process is gained, resulting from the data collected and visualised. The enhanced data capture was leveraged for data driven decision making, which led to shortened timeframes to ‘cure’ the composite, resulting in a reduction in energy usage
- Overall cost savings and an improved environmental impact of the LRI composite manufacturing process
A detailed report about using and implementing SAMP in manufacturing environments is available from [email protected]
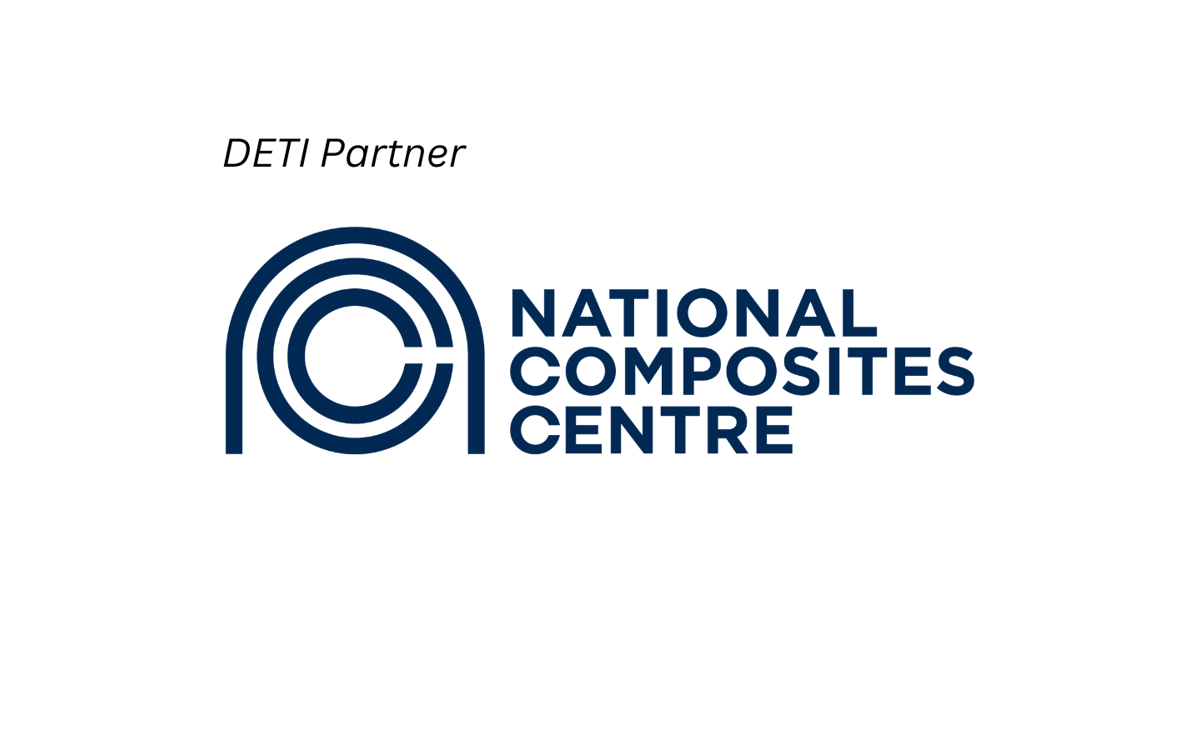