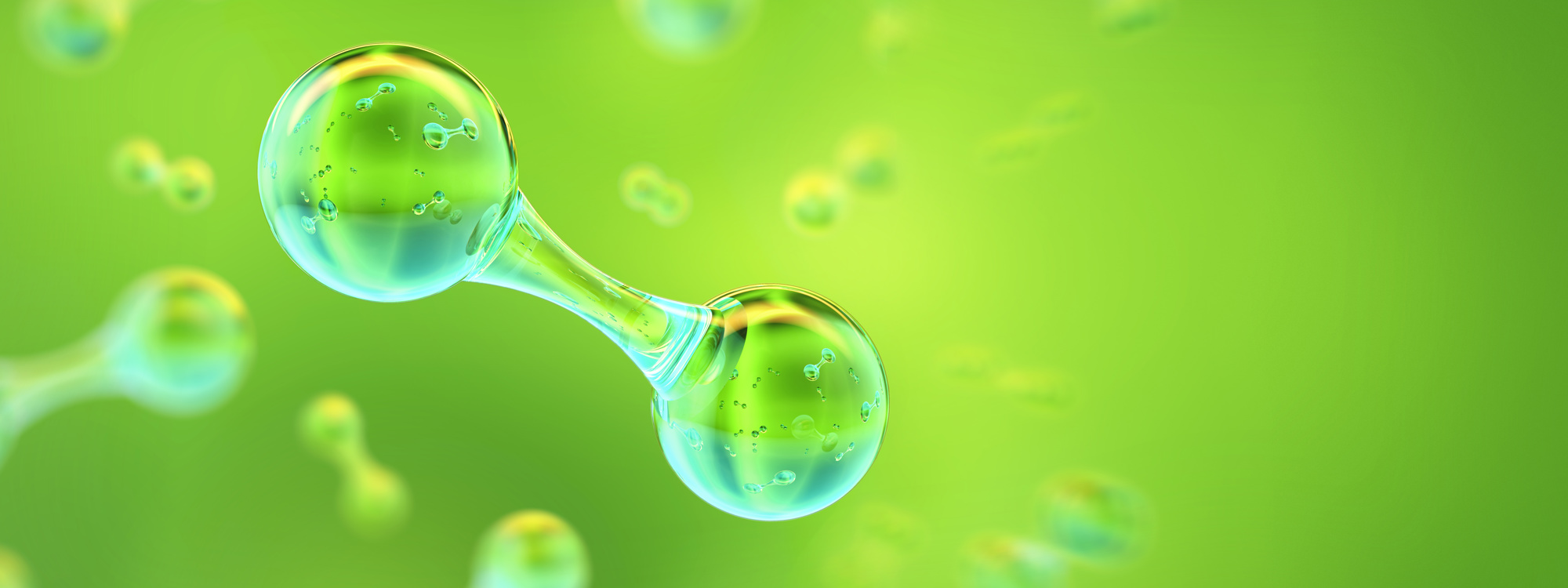
Establishing rapid testing for cryogenic composite applications
By Marcus Wall-Bruck, Head of Hydrogen Technologies, and Matt Kay, Principal Research Engineer, Hydrogen
Interest in cryogenics is booming, aerospace and energy companies recognise the importance of hydrogen as we race towards Net Zero.
Whether to improve aircraft performance or simplify the deployment process, composites can play a key role in liquid hydrogen systems.
Beyond lightweighting, they also offer the potential for improved integration via reduced thermal expansion and electromagnetic interference.
The NCC has been working both with our customers and independently to establish expertise in testing and designing composites for use in cryogenic systems.
We all know that cryogenics posses a significant challenge regardless of the materials used in making the system.
Composites are no different and have their own unique set of challenges.
Key among these is microcracking.
The fundamental problem for any composite cryogenic containment vessel is thermal and mechanical stresses combining to form microcracking in the matrix.
Regardless of the potential mechanical properties, if the microcracking forms a network through the thickness allowing the hydrogen to leak, the part will not be fit for purpose.
There are a range of possible solutions for improving microcracking performance, importantly these go beyond modification of the matrix.
Our liquid hydrogen tank design, build, and test program has highlighted the importance of ply design both in reduced ply thickness and adjacent ply angle.
In some senses this makes the design challenge more difficult as we have more options to choose from.
Further, as we reduce ply thickness, we also face increased deposition time and material cost.
However, work at the NCC has shown that the potential of design in this area is critical to achieving long life cryogenic containers and overcome some of the potential downsides of niche cryo-resin formulations.
Improved understanding and the ability to quickly optimise in this area is essential.
This is why we are developing a unique approach to testing at cryogenic temperatures which focuses on microcrack formation without the need to use time consuming and expensive cyclic testing.
This type of testing can simplify material selection and informs modelling such that designs can be appropriately stressed without inducing microcrack leakage.
Understanding the behaviour at this fundamental level allows the NCC to benefit as wide a range of industries as possible as each face their own separate but overlapping set of challenges.
The NCC’s role is to work closely with our members and customers to solve difficult challenges. By bringing together our industrial focus, testing expertise, and world class facilities we can make progress that benefits everyone involved.
We’re already working hard on the solutions to material selection and characterisation, if you’re interested in being involved then please get in touch.
For more information about accessing the NCC composite cryogenic tank testing, concepting and design tools, contact: [email protected]
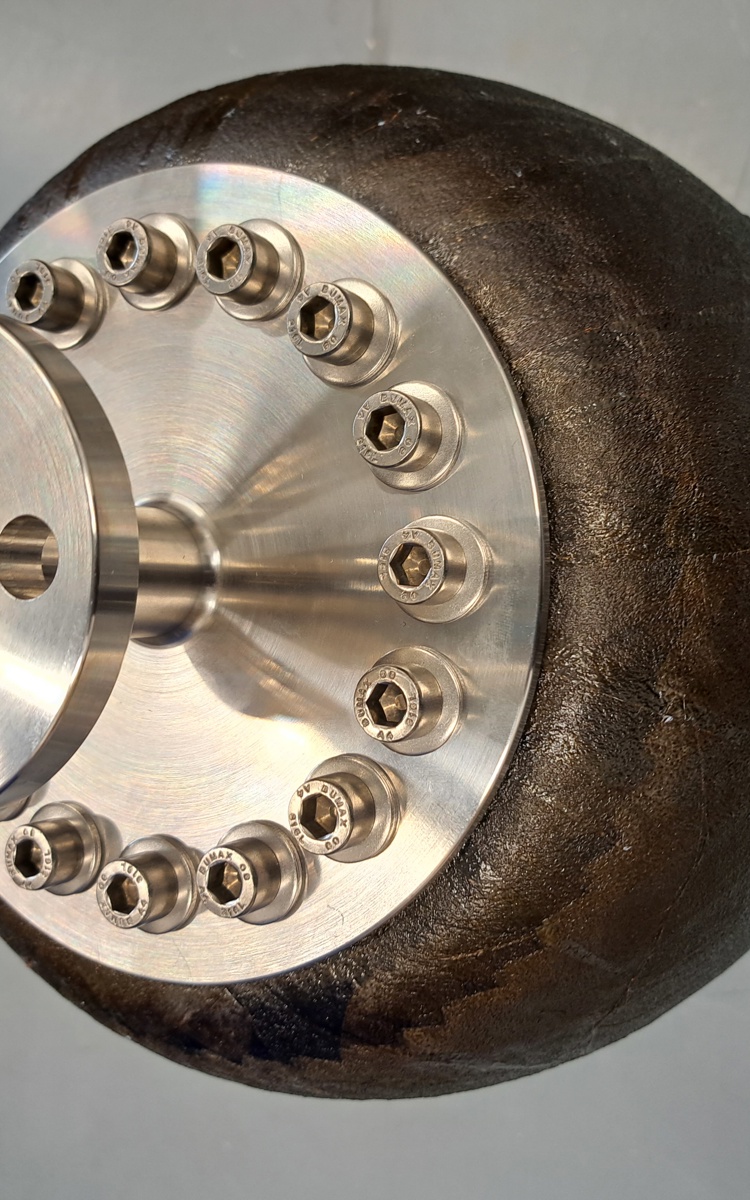