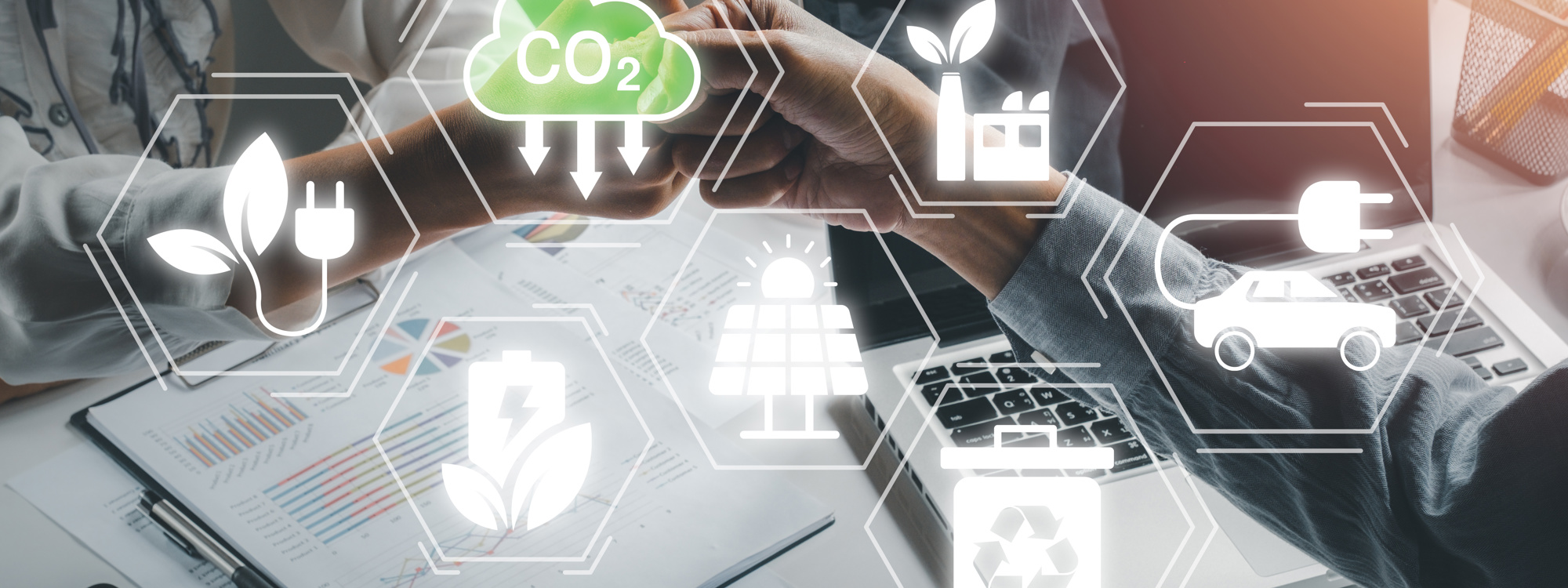
National Composites Centre announces results for Life Cycle Assessment Tools for Construction
The National Composites Centre has completed an assessment of the composites data referenced in software and tools for Life Cycle Assessments (LCA) used within the Construction sector.
Decarbonisation of industries and the requirement for reducing carbon emissions to meet Net Zero have prompted a need to ensure robust and accurate assessment of carbon footprint to minimise greenhouse gas emissions. As the construction industry looks to capitalise on the benefits that composite materials might bring to projects, there is an increasing need to account appropriately for composite materials in the assessment tools for carbon accounting.
Software and tools for LCA range from specific software with comprehensive life cycle inventory databases, through to tools specific to the construction sector or other applications that use composite materials.
In the study undertaken by the NCC, it was found that the carbon footprint of a glass fibre composite output from one tool could be almost double for the same assessment used in a different tool. The result is that when applied in a decision-making process in early design stages, these diverse values can force a different outcome depending on the tool used.
For example, when comparing a Glass Fibre Reinforced Plastic (GFRP) composite component to galvanised steel with a requirement to select the design with the lowest carbon footprint, the value from LCA tool 1 would indicate a lower carbon footprint and the value from LCA tool 2 would indicate a higher carbon footprint [1]. The NCC undertake a data quality assessment to determine applicability of data values, and in this case found that the value from ‘LCA tool 1’ to be more valid.
Figure 1 Global warming potential in kg CO2 eq for 1kg of glass fibre reinforced composite material
Ffion Martin, Engineering Capability Lead for Sustainability at the National Composites Centre, said: “It is crucial for users of LCA software to understand the background data referenced by these tools, in order for them to have confidence in their decisions driven by the output of assessments, and to mitigate business risk.”
Malcolm Forsyth, Sustainability Manager, Composites UK and Lee Canning, Chair of the Construction Sector Sustainability Subteam, Composites UK said: “The use of carbon emission data is now well-established as a key criteria for material selection in Construction and other major sectors, and therefore it is vital that widely-used carbon databases have up-to-date and accurate data for all materials to ensure valid and appropriate decision-making. This NCC project is helping to ensure that designers and engineers have access to the best available data for composite materials and is therefore fully supported by Composites UK and all its members from across multiple end-use sectors.”
The NCC, together with the researchers at the University of Bath through the Innovation Centre for Applied Sustainable Technologies (ICAST) are establishing and applying methods for data quality assessment and presentation of uncertainty, as part of the ICAST Core Research Programme that focuses on using sustainable materials engineering to inform design and product development for decarbonisation. The ICAST project will continue the LCA assessment work undertaken by NCC, and further develop LCA data for construction and infrastructure (C&I), with a focus on bio-materials and other sustainable advanced material options (e.g. glass, basalt). Phase 1 of the project will complete in March 2023, which will review and implement approaches to enable users of environmental impact data to have confidence in the numbers driving carbon footprint assessment and ultimately driving design choices.
If you are interested in finding out more about LCA through the National Composites Centre, email: [email protected]
[1] Assessment based on the embodied carbon of world average hot dip galvanised steel in the ICE db v3.0 and ~50% mass estimate of an equivalent GFRP to steel structure (higher specific strength of GFRP to steel).