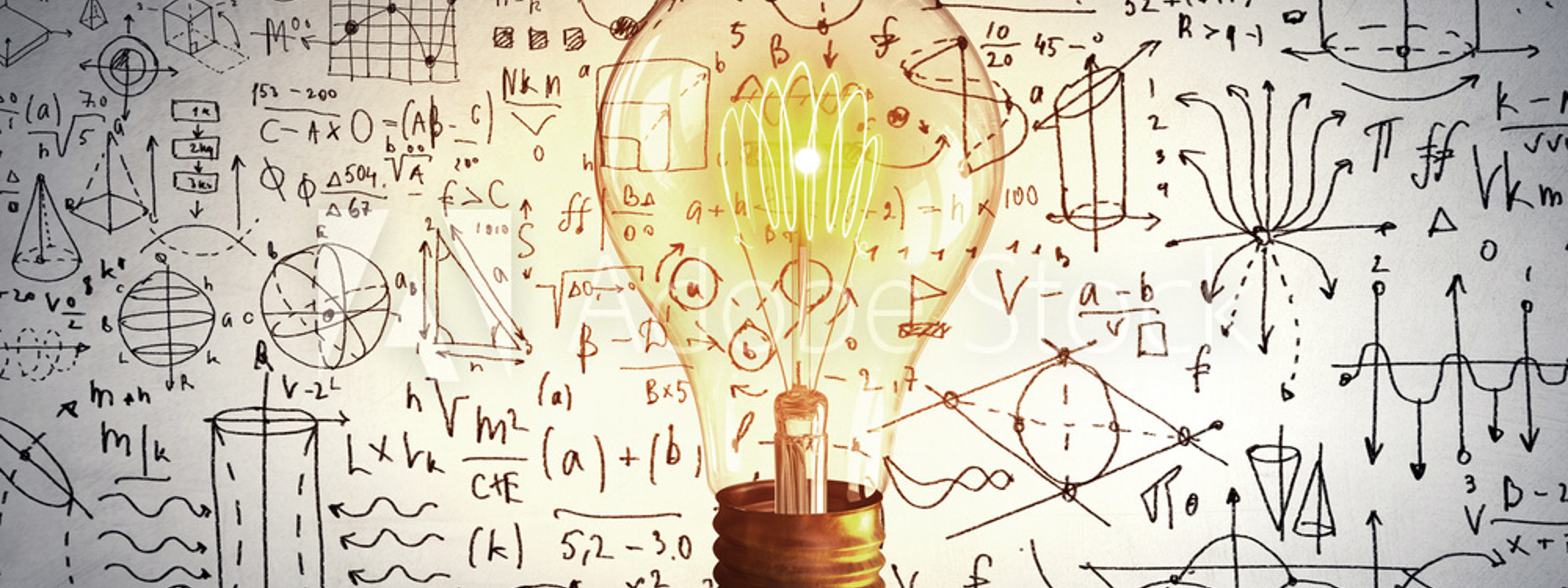
NCC partners with Drive System Design on new Electric Vehicle project
The NCC is partnering with British engineering specialist, Drive System Design (DSD), on a new project that seeks to improve the efficiency of the integrated electric drive unit (EDU) of electric vehicles (EVs).
The 12-month project, part-funded by Innovate UK, will investigate the use of composites to enable increased power density and reduced unit size, offering vehicle manufacturers further packaging and efficiency benefits.
“Vehicle range at reasonable cost is still one of the biggest barriers to widespread adoption of EVs, so technology that can increase this through efficiency gains – without adding significantly to unit cost – are crucial,” says Markus Hose, DSD Head of Mechanical Engineering. “Vehicle manufacturers are facing increasing packaging challenges as they seek to incorporate higher performance EDUs into latest designs, so power density improvements will offer a key competitive advantage.
“NVH and efficiency have traditionally been at odds during vehicle powertrain development, but through this project DSD aims to overcome this challenge,” adds Hose. “Historically, attributes have been managed independently. For example, efficient designs can be created, but iterative work is typically required to overcome the resulting NVH (noise, vibration and harshness) challenges. This project considers NVH from the outset and is central to any decision making, resulting in an EDU optimised for real-world operation.”
The project addresses the challenge of effectively balancing NVH and efficiency in two parallel work streams. The first will look to increase the EDU efficiency through targeted use of composite material. For example, if the NVH dampening properties of composites can be harnessed, the EDU will be more tolerant to NVH inputs for the motor and transmission. With NVH and efficiency often being in competition with each other, this increased NVH tolerance would provide design engineers with greater freedom to increase efficiency. The second work stream utilises composite sleeves to enclose a rotor in a way that is scalable for high volume manufacture, enabling higher power density eMotors, which in turn helps to reduce unit mass and size.
Aliya Valiyff, Technology Programme Manager for Automotive at the NCC, says: “The NCC is looking forward to working with DSD to develop the tools and processes that enable efficient integrated drive units through targeted application of composite materials. As the country moves towards an all-electric future transport system by 2040 – with similar targets in other countries – there is a major market opportunity for both the domestic market and for exports. The NCC, in partnership with DSD and IUK, will be contributing to enhancing UK skills in power electronics, machines and drives by cementing existing skills and developing new technology.”
Image copyright Drive System Design Ltd.
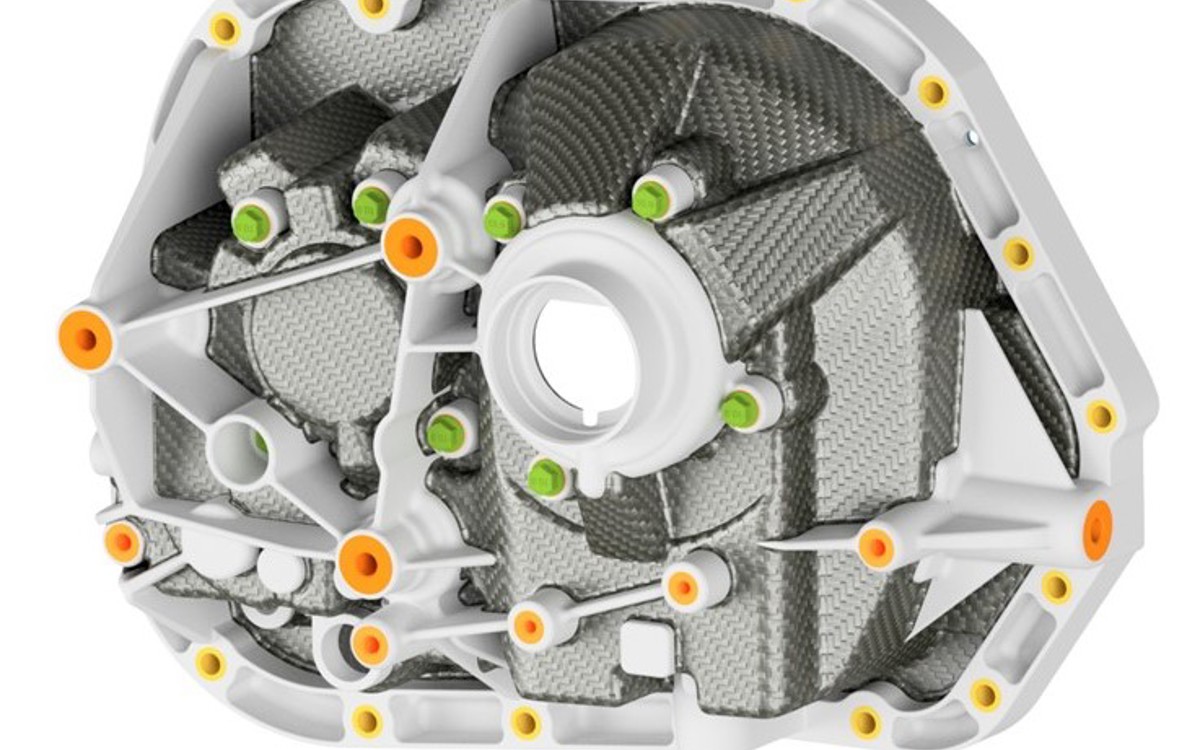