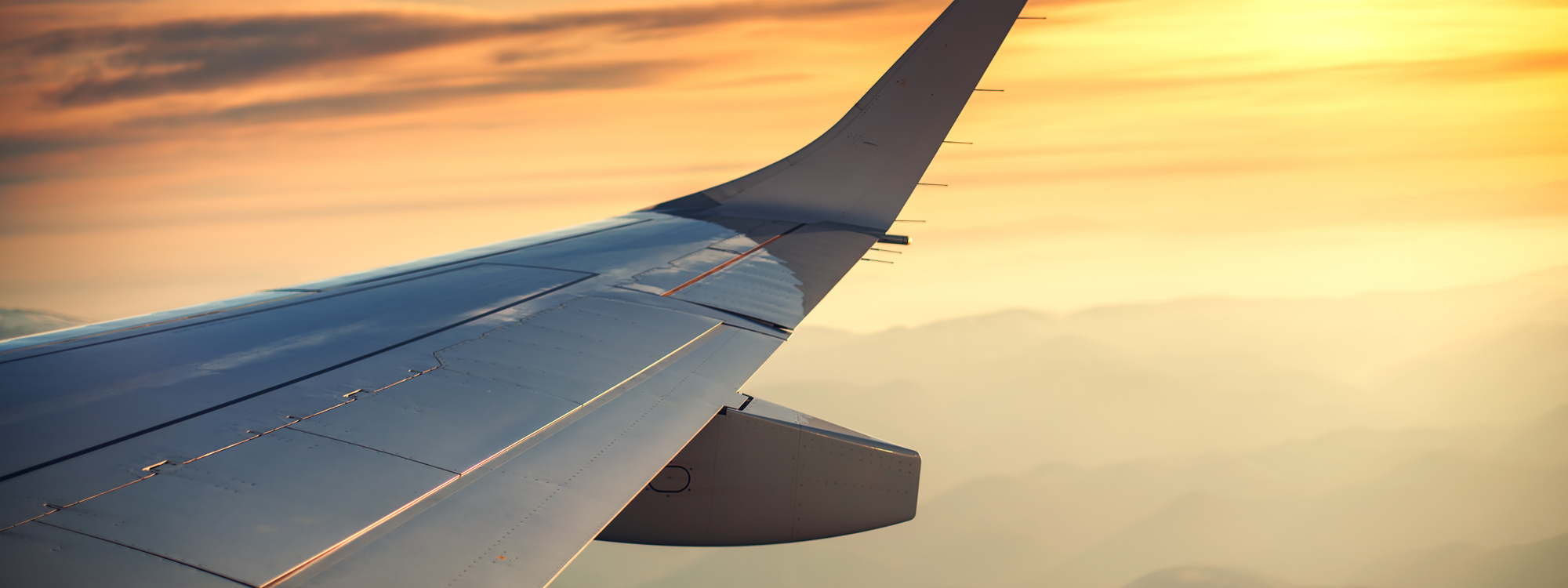
New Large Scale Resin Infusion Capabilities at the NCC
20 February 2019
New Large Scale Resin Infusion capabilities at the NCC enable full-scale demonstration of wind, aerospace and infrastructure manufacturing.
The National Composites Centre (NCC) and Composite Integration Ltd today celebrate the successful completion of a year-long project to design and deliver a state-of-the-art, first of its kind, Large Scale Resin Infusion (LSRI) technology. This innovative system has been designed to meet the R&D demands of both aerospace and wind industry manufacturing where components can range from 17m up to 120m in length.
Liquid Composite Moulding (LCM) is one of the core competencies of the NCC and High-Value manufacturing in the UK. It is used to produce high integrity composite parts, without the need for an autoclave (an industrial pressure cooker). Using Liquid Composite Moulding, fibres are first assembled ‘dry’ into a mould, resin is then pumped into the fibres and drawn through under vacuum prior to being cured in an oven.
The NCC identified the need to procure a Large Scale Resin Infusion (LSRI) capability as part of its iCAP Programme, a £36.7m investment in ten digital manufacturing technologies being installed at the NCC to directly stimulate and support composites innovation, manufacturing and research development programmes across a range of sectors.
The acquisition of the LSRI equipment from South West -based SME, Composite Integration Ltd, who are experts in this field, will enable the NCC to widen the applicability of LCM processes to a wider range of components.
The experienced team of NCC engineers, combined with rich process-data from the new equipment, will reduce risk and improve outcomes of high value infusions. The first application of this exciting technology will be to enable infusion of complete wing components as part of next generation wing technology developments.
The new capability, now available to companies across the UK, offers a robust means of LSRI and is capable of injecting high resin volumes into a variety of preforms - primarily, but not limited to, using a vacuum bagged set up.
This modular machine has additional flexibility to process both single or two-part resin systems and will be teamed with a 20m oven to enable cure of those resins. Together they will create a step change in the production of high quality, high fibre volume fraction composite parts.
The wealth of data collected by the machine is a key component in the NCC driving forwards innovation in technology and techniques to deliver ‘Industry 4.0’ for composites. The system can already react to this data in real-time to intelligently adapt the infusion parameters and ensure the mould is filled. As the NCC capability develops it will allow for machine learning to recommend infusion cycle improvements based on data acquired from previous infusion cycles.
Peter Giddings, Chief Engineer, iCAP at the National Composites Centre said:
“Our Large Scale Resin Infusion equipment is game-changing for large infusion projects and as part of the iCAP programme takes us significantly closer to achieving our ambition of automating the infusion process to help reduce costs and production cycle times.
“Whether you are manufacturing 18m long composite wings, boat hulls or bridges, the equipment and our team of experts is here to help you drive forward your emerging technology to industrial application.”
Simon Vincent, Design and Engineering Manager at Composite Integration said:
“Processing aerospace grade epoxy resin systems at elevated temperatures brings with it a number of challenges. Although equipment exists on the market for processing smaller quantities of these resin systems, as the scale of Aerospace parts being manufactured using Liquid Resin Infusion has increased, there was an evident need to develop machinery capable of processing up to 400Kg of high temperature epoxy resin. This is the first machine of its kind that can process this type of resin in batches larger than 50kg.
“Composite Integration has utilised experience gained through on-going work with the marine and renewable energy markets relating to serial production of ‘large scale’ composite structures as well as research and development carried out on smaller aerospace components to develop a piece of equipment that can accurately monitor and control a wide variety of process variables.
“The LSRI machine has allowed us to further develop new state-of-the-art technologies, which when combined with years of practical processing experience, puts us firmly at the forefront of Out of Autoclave process development.”