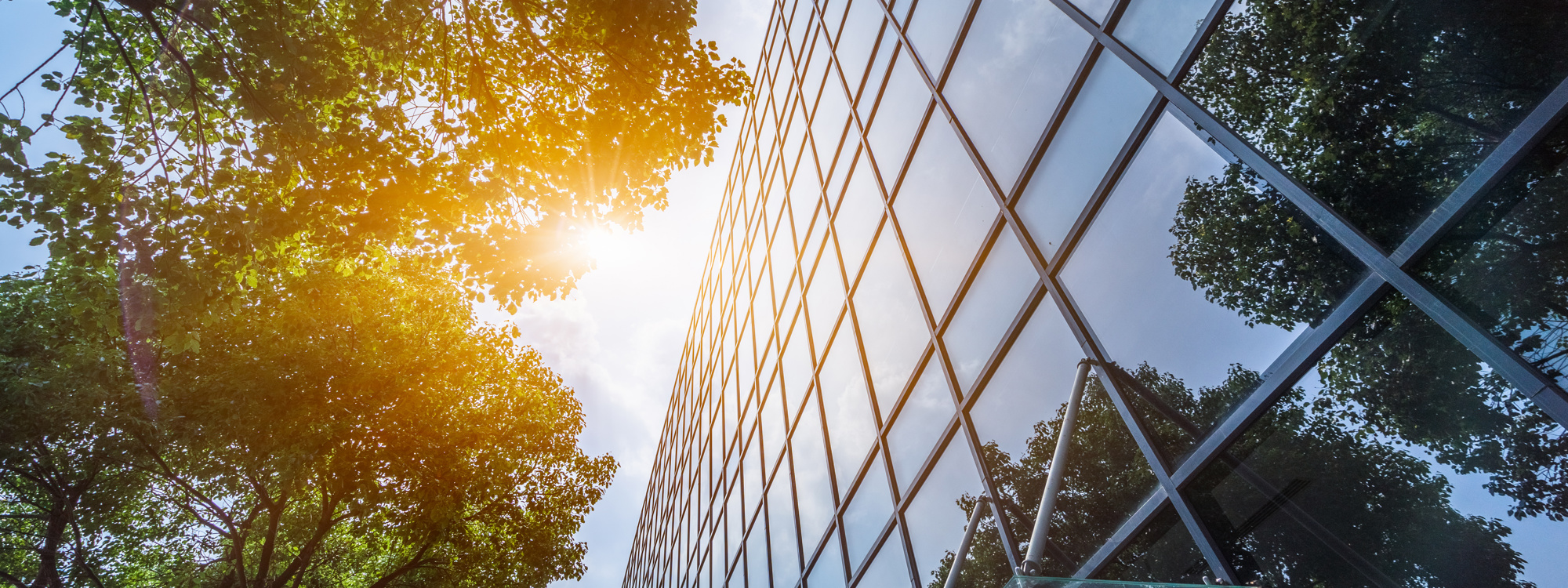
New platform-based approach to construction unveiled
- Seismic excels against traditional construction methods: 75% faster, 70% lower in carbon (both embodied and operational), and 47% better value.
- Delivered by a consortium of seven companies, including MMC experts, manufacturers, and consultants.
- Demonstrator building combines components from three manufacturers and two systems in one.
- Seismic is one of the case studies included in the pending Platform Rulebook from the Construction Innovation Hub.
With the UK government pushing for platform-based construction solutions, a new demonstrator building offers a glimpse of the future.
The Seismic demonstrator is the culmination of a four-year project developed by a consortium comprising consultancy blacc, offsite manufacturers Elliott Group and the McAvoy, Tata Steel, the Manufacturing Technology Centre (MTC), the National Composite Centre (NCC) and Specific (part of Swansea University).
Designed in line with the government’s Construction 2025 targets, it exceeds them in every way, delivering a building that is 75% faster to complete, 70% lower in carbon impact and 47% better value than traditional construction.
One of the unique aspects of the project is the combination of three manufacturers working independently on the same building. The demonstrator shows this to good effect incorporating systems from McAvoy, Elliott Group and Tata Steel.
Richard Crosby, director at blacc, said: “Seismic was developed to help drive a shift towards Modern Methods of Construction (MMC) in the industry. What the consortium has achieved demonstrates the value of a standardised, platform-based approach to construction. It is faster at every stage, from design through to manufacturing, assembly and fitout, and offers better quality and value, alongside a dramatically lower carbon impact.
“Seismic sets the template for a platform-based approach to construction and proves that it can be done now. This offers a huge opportunity for unlocking development, providing a solution for a range of sectors, including education, healthcare, workplace, leisure and residential.”
Seismic has been worked on in two stages. Phase one was developed in response to work with the Department for Education (DfE) to improve the delivery of schools. It focused on the design of a standardised, lightweight steel frame and connector and was completed in 2020.
Because of its success, a second stage was commissioned. The objective was to design and construct core components that would work with the frame system, including wall, floor, ceiling and roof cassettes, offering an “all-in-one” solution for clients.
Sam Stacey, Challenge Director for Transforming Construction, said: “Most modular construction relies on bespoke systems created by individual manufacturers. A lack of standardisation means that different systems are incompatible, which adds risk for clients, especially once they take on responsibility for the building’s operation and maintenance.
“What Seismic shows is that if everyone works to one system it is possible to deliver buildings much more effectively, whether compared with existing modular techniques or traditional construction.”
The ambition is that Seismic provides a blueprint for the modular market to grow. Other work packages within the project included the development of a framework to analyse a manufacturer’s ‘MMC readiness’. Led by the Manufacturing Technology Centre (MTC), it also includes a methodology to set up the most effective production processes within factories.
There has also been extensive testing and analysis of the materials and components used within Seismic, with over half-a-million pounds spent on analysing fire, thermal, acoustic and structural performance. The latter included extensive vibration testing which has opened a new avenue of research into the link between floor movement and occupant wellbeing.
The National Composites Centre (NCC) was appointed to analyse and recommend the best materials to be used for the platform. It also developed a window shroud which was used within the demonstrator building.
This supported a wider package of work led by Specific, part of Swansea University, to assess the carbon impacts of Seismic. This looked at the whole process including design, materials, manufacturing, component performance and logistics.
The analysis showed that a standard Seismic module comprises 581.3 kgCO2e per m2, well below Construction 2025’s target of 1,300 kgCO2e per m2. And, because Seismic can be reused, either by relocating modules to other sites or by refurbishing individual components and cassettes, it adds a 234 kgCO2e per m2 clawback. This brings Seismic well beyond even the lowest stretch targets being discussed in construction today.
Keith Waller, Programme Director, Construction Innovation Hub, added: “A project like Seismic can bring significant learnings to the construction industry, clients and end users, meaning projects can be delivered faster, with lower carbon impact and better value.
“Seismic is platform-based, meaning it is future proofed and as manufacturing becomes more efficient and new technology comes to market, better solutions can be switched in as and when appropriate.”
Seismic was part funded by the Transforming Construction Challenge, part of UK Research and Innovation (UKRI). The project team worked closely with the Construction Innovation Hub supporting the work on the Hub’s Platform Rulebook.
People can visit the demonstrator building at BRE Watford until the end of the year.
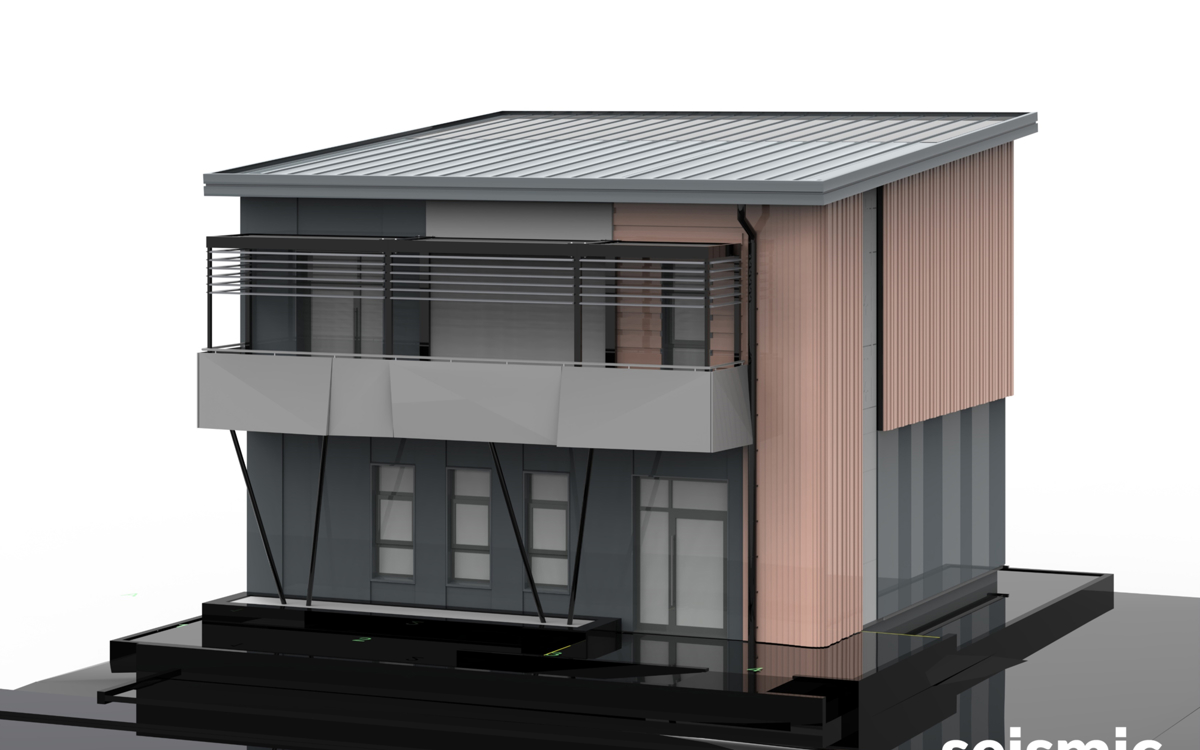