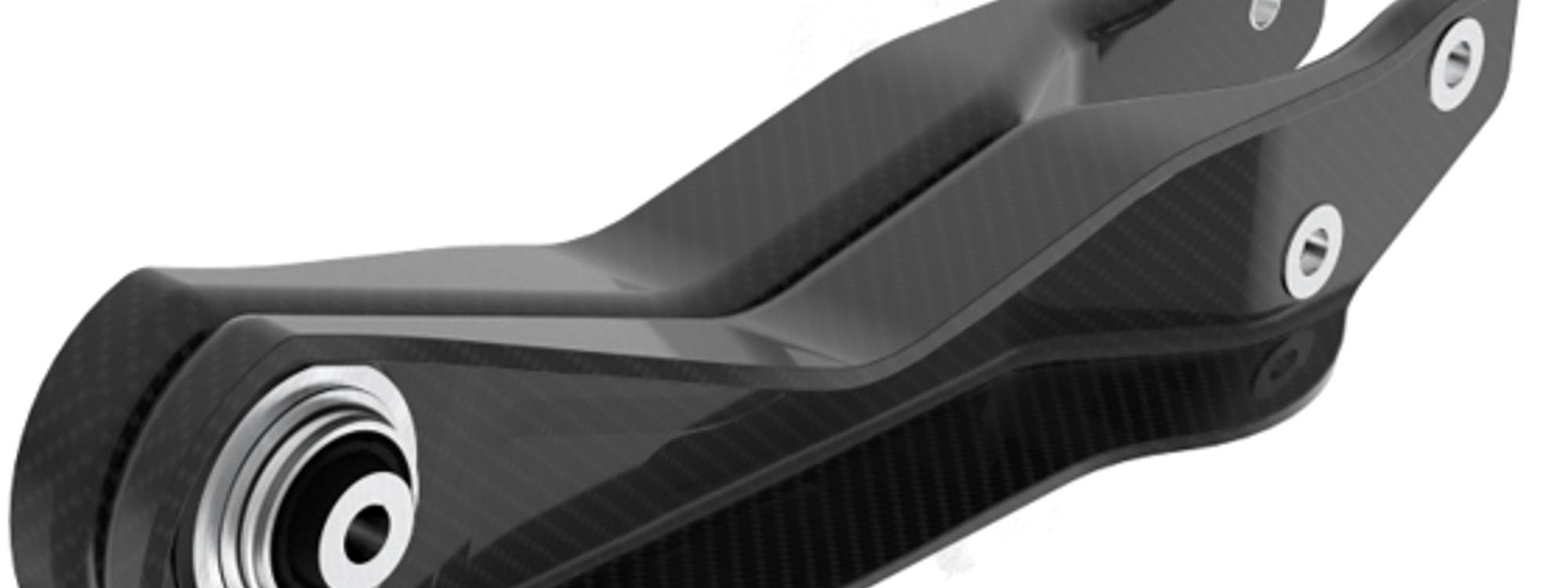
Project Century
Global imperatives to reduce emissions are driving the shift to green modes of transport, in particular, electric vehicles.
Putting aside issues of national power generation, in terms of electric vehicles themselves, there are two major technological challenges: the need for better batteries, primarily to increase range and speed up recharging; and reducing vehicle mass without compromising on strength to further boost efficiency.
Whilst improvements in powertrains have delivered CO2 reductions, beyond 2020, the automotive industry will require truly disruptive approaches in order to meet the UK’s stated goal that all new cars and vans should be ‘zero emission’ by 2040.
For decades the automotive sector has turned to composite materials to provide strong but lightweight structures for specific applications such as bodywork and propshafts, yet uptake has tended to remain in these niche, low volume markets such as Formula racing. The more widespread use of composites has been hampered by the lack of a robust supply chain.
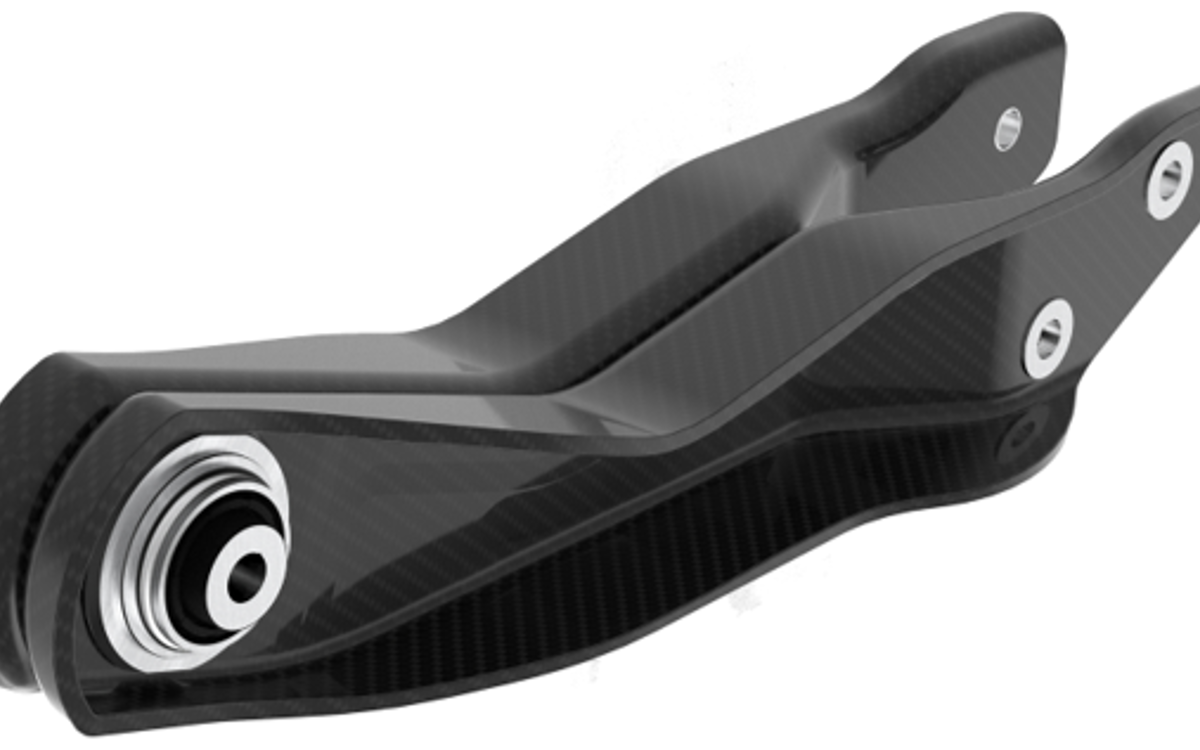
Project Century was a £4.9m initiative investigating whether a manufacturing process for a composite component could meet automotive industry targets of a 60 second production cycle time, equating to a vehicle production rate of 50,000 a year. Allied to this was the goal of delivering a comparative component weight reduction in the region of 30% compared to metallic counterparts.
Led by GKN, the project consortium also included Far Composites, Hexcel, The Welding Institute and the University of Nottingham, supported by an Advisory Board comprising Jaguar Land Rover, Bentley, Nissan and McLaren.
The National Composites Centre (NCC) was tasked with taking an existing component and developing a composite manufacturing process that would deliver a lightweight, structural and commercially viable composite alternative at scale. A lower control arm connecting the wheel hub to the chassis and weighing 1.5kg, was selected as the baseline component.
After a 30-month long process, the team at the NCC was able to deliver a composite control arm 20% lighter than its metal equivalent, in a manufacturing time of under sixty seconds using the dynamic fluid compression moulding process (DFCM).
The NCC supported GKN in developing and extending their toolkit on composites design, analysis and costing, demonstrating how they could take an existing component, redesign for composite and take it through to manufacturing production.
Project Century was funded by Innovate UK with additional funding from the industry partners and ran from September 2016 to August 2019.
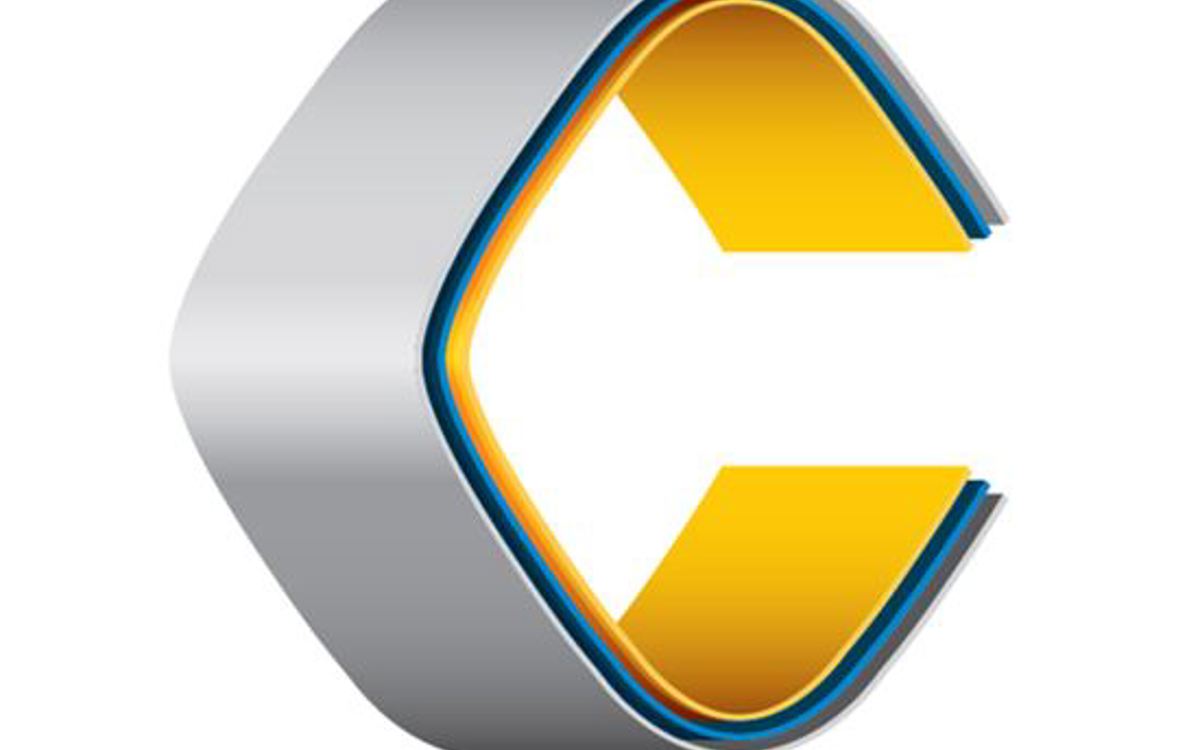