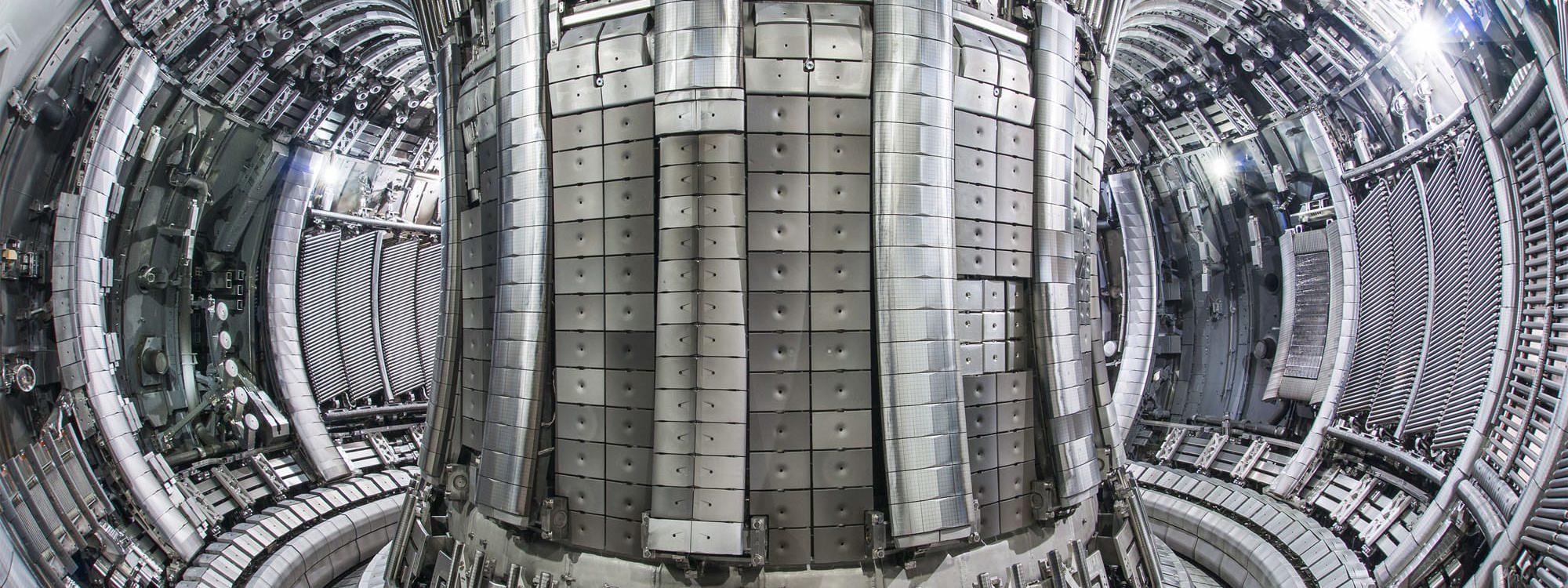
SiC/SiC composites enable twice the electricity from fusion-generated heat
- Radical reduction of cost and lead time for SiC/SiC composites could enable a transformation in demand high temperature applications.
- Together with the UK Atomic Energy Authority (UKAEA) the National Composites Centre (NCC) has identified a step change in SiC/SiC manufacturing that has transformative potential.
Fusion energy promises nearly boundless, sustainable power. In recent years, many advances have been made that have the potential to unlock this almost limitless source of low carbon energy. The only problem is that harnessing the energy created by searing heat and unimaginable pressure within the core of a fusion reactor is probably the most complicated scientific challenge on earth. Throughout the history of fusion research, finding materials capable of withstanding these conditions has been at the core of taking fusion from a scientific challenge into a commercially viable power source.
The use of silicon carbide composite (SiC/SiC) components within fusion reactors has the potential to double the electricity generated from every gigawatt of thermal energy produced compared with advanced steel designs.
This incredible improvement comes from increasing the maximum allowable temperature of the coolant used to extract energy from the reactor within the breeder blanket component. In SiC/SiC breeder blankets, the temperature could be increased to 900C or even 1000C, allowing more efficient generator approaches to be used.
This increased temperature, compared with steel blanket designs where temperature is limited to around 550C, is what makes SiC/SiC so attractive as a fusion material, together with their ability to maintain structural strength in the presence of severe radiation exposure and their excellent chemical stability.
Realising SiC/SiC breeder blankets would create billions of pounds in value of additional electricity generation over the life of a commercial fusion plant. However, there are technical, commercial and industrial barriers to be overcome to improve today’s SiC/SiC materials and the processing methods by which components are manufactured.
Together with the UK Atomic Energy Authority (UKAEA) the National Composites Centre (NCC) have identified a step change in SiC/SiC manufacturing that has transformative potential:
- 1/5th the cost compared with chemical vapour infiltration (CVI)
- Achieves 95% density as opposed to 75% with CVI
- Unlocks component geometries and thicknesses not possible with current techniques in contrast to other candidate methods.
This material innovation has the potential to revolutionise the profitability of fusion-powered energy. As the cost and uncertainty reduces, ultra-high temperature silicon carbide composites have the potential to support decarbonisation of steel and other process industries as well as improving performance of critical defence systems.
The journey to realising an industrialised supply chain for SiC/SiC components will be long, but there is real opportunity for forward-looking businesses to be part of shaping the industry that will serve the demand for SiC/SiC materials. The NCC is aiming to convene collaborations across the value chain to shorten the timescales to develop and deploy commercially viable and industrialised solutions.
It's rare to see an opportunity to architect an industry that could have a measurable impact on the race to decarbonise power generation. The application of SiC/SiC composite materials opens up new and exciting opportunities to improve our everyday lives, helping us to address the urgent societal challenges of energy security and Net Zero. Please get in touch to find your place in the effort to do just that by making high-volume high-performance SiC/SiC composites a reality.
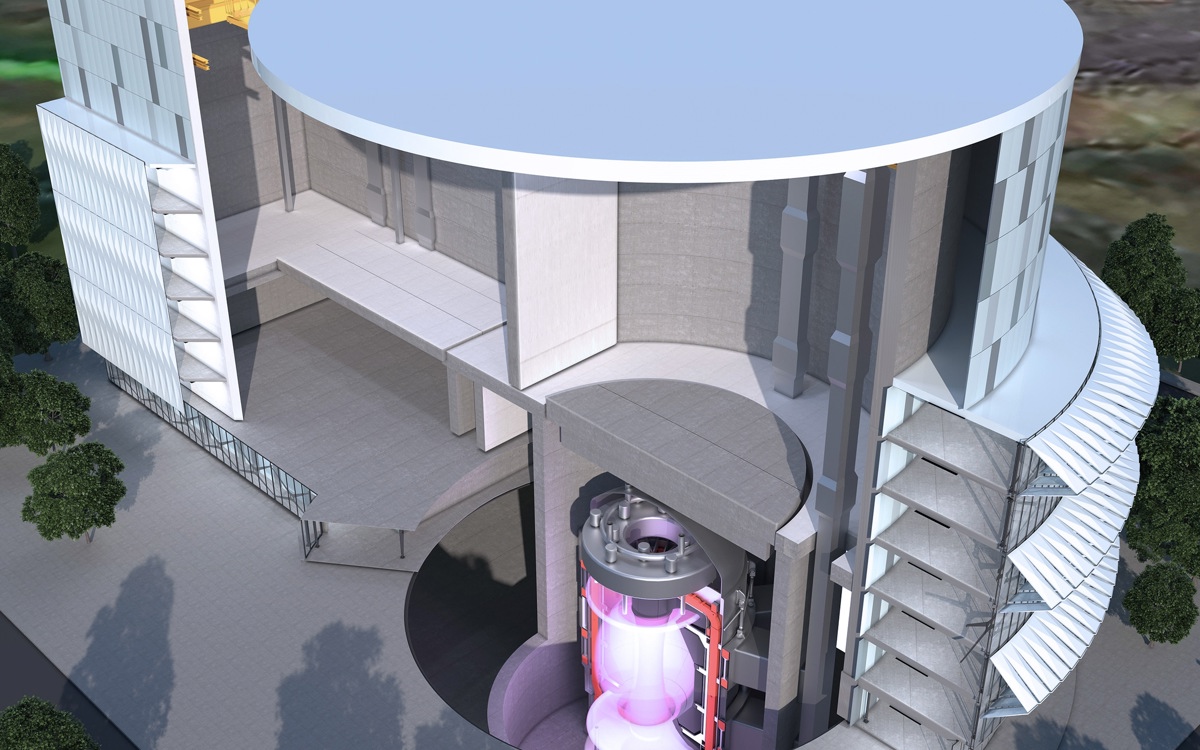