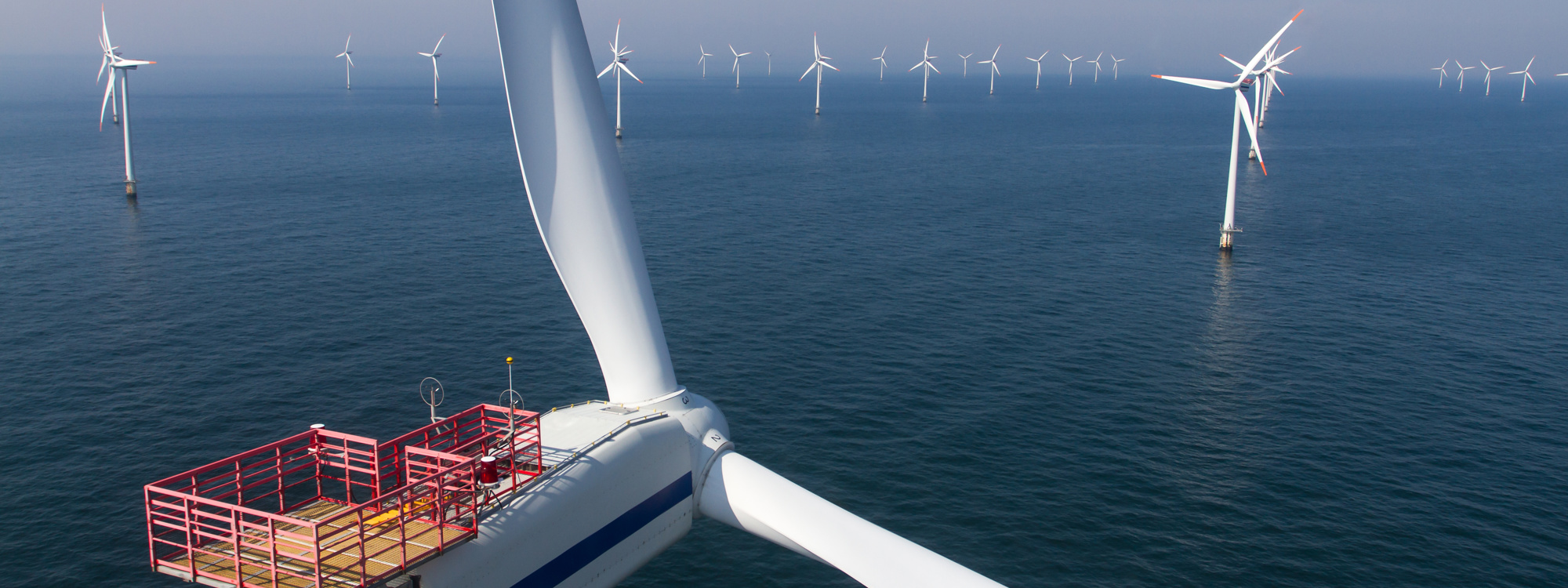
Towards turbine blade production with zero waste - TURBO
NCC is pleased to announce its participation in TURBO.
A new Horizon Europe project to improve the sustainability of wind turbine blade production by reducing defect formation and improving repair strategies in composites and coatings.
Image courtesy of Siemens Gamesa Renewable Energy A/S.
Technical University of Denmark (DTU) is the Coordinator of TURBO, which started on 01-Oct-2022. The project will combine several new developments from different disciplines to improve the sustainability of wind turbine blade (WTB) production by reducing defect formation and improving repair strategies in composites and coatings.
Wind turbines are already part of everyday European life and are an essential element of the strategy to meet the Green Deal targets. WTB size is steadily increasing with the largest new offshore blades >100 m in length. Composite blades are manufactured using resin infusion and coating processes. Even using modern manufacturing methods, these are subject to defects, which result in re-work, scrap, and repair. TURBO will reduce defect formation through better process simulation, monitoring and control, improve defect identification with new methods of non-destructive testing (NDT) and introduce novel repair strategies in composites and coatings.
- Simulation: The project will develop highly accurate simulations of the production process to minimise defect formation by combining the latest multi-physics process modelling with reduced order models to improve understanding of the composite manufacturing process.
- NDT: TURBO will investigate both in-line NDT to monitor WTB composite infusion and post-manufacture sub-surface WTB coating inspection, combining ultrasound and mid-infrared optical coherence tomography.
- Process control: The production equipment, monitoring sensor and in-line NDT data will be combined to establish a digital twin for real-time analysis and production control including the application of machine learning.
James Lightfoot, Senior Technology Programme Manager for the NCC’s Energy Sector said: “Digital engineering technologies, such as self-adaptive manufacturing processes, have the potential to significantly increase the efficiency of wind turbine blade manufacturing. TURBO will develop emerging digital technologies including process simulation, sensorisation and machine learning to reduce the cost of non-quality associated with blade manufacturing. NCC will play a key role across the programme and is excited to contribute to a crucial outcome for Siemens Gamesa Renewable Energy.”
The project will demonstrate its results in the fabrication of full size WTB sections at the Siemens Gamesa Renewable Energy factory in Aalborg, Denmark. The workplan also includes full lifecycle analysis, environmental assessments and production efficiency analysis to quantify the project benefits.
More information is available from the project website: https://turboproject.eu
Partners in the Project
Beneficiaries:
- DANMARKS TEKNISKE UNIVERSITET - DK
- SIEMENS GAMESEA RENEWABLE ENERGY AS - DK
- HUBERS VERFAHRENSTECHNIK MASCHINENBAU GMBH - de
- ESI GROUP - FR
- UNIVERSITAT POLITECNICA DE VALENCIA - ES
- SYNTHESITES - BE
- NORBLIS APS - DK
- VIVID COMPONENTS GERMANY UG - DE
- ARDITEC - FR
Associated Partners:
10. NATIONAL COMPOSITES CENTRE - UK
11. SMARTIA LTD - UK
12. CENTRE FOR PROCESS INNOVATION LIMITED - UK
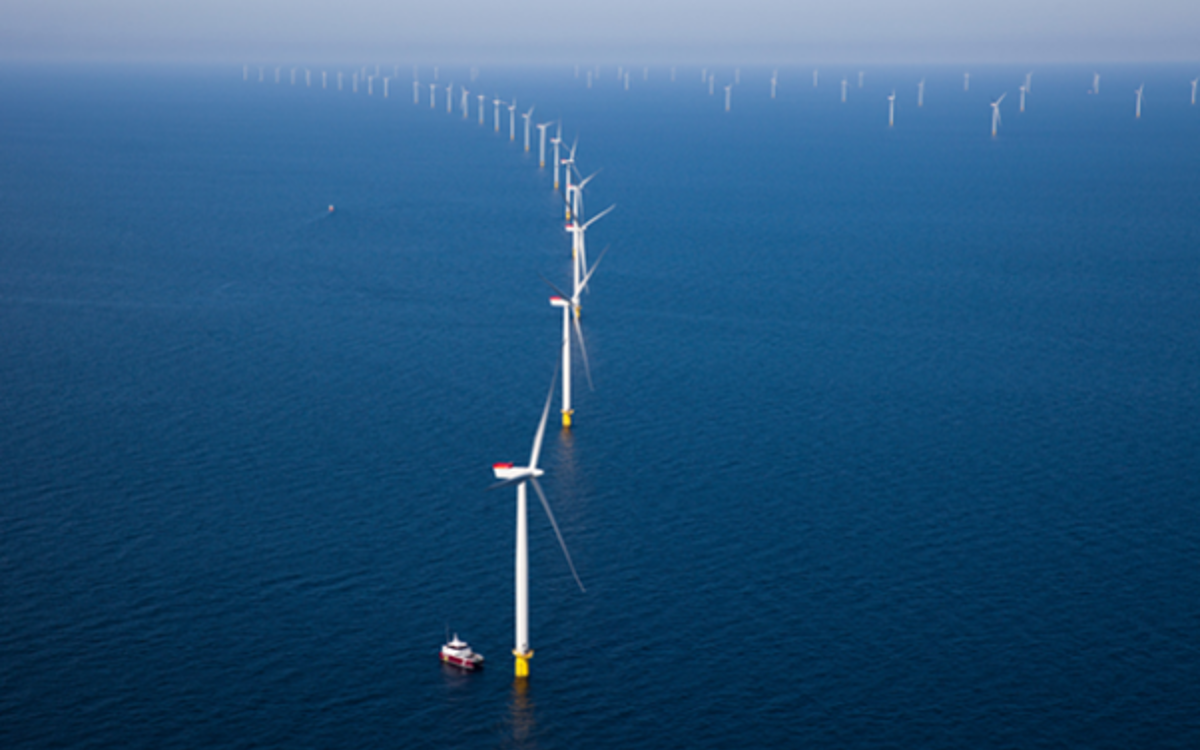