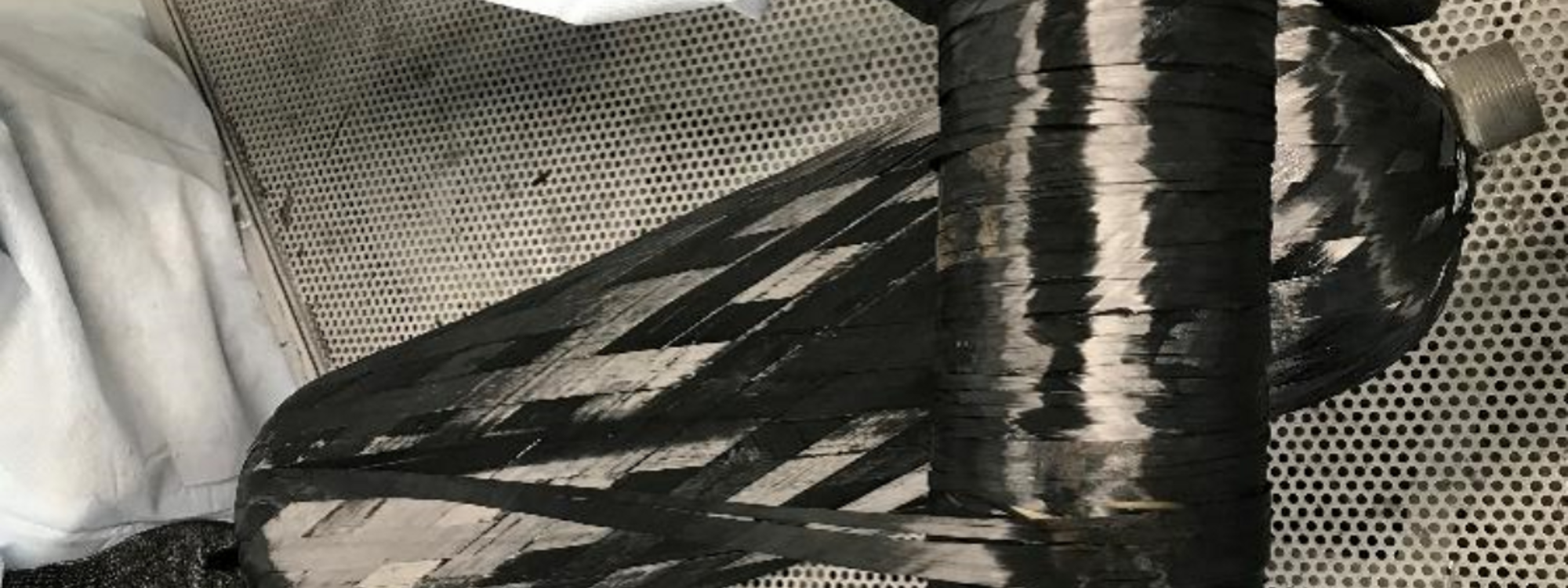
UK team successfully recycles reclaimed continuous carbon fibres from composite pressure tanks
- The UK’s National Composites Centre with partners B&M Longworth and Cygnet Texkimp achieve continuous carbon fibre recovery.
- Successful trial marks significant first step in ambitious hydrogen innovation programme to deliver sustainable composite pressure vessels.
- The team is ready to industrialise process with companies looking to expand pressure vessel manufacturing capabilities.
Engineers at the National Composites Centre, the UK’s centre of excellence for advanced composite applications, along with British SME partners B&M Longworth Ltd and Cygnet Texkimp, have successfully reclaimed continuous carbon fibres from a whole pressure vessel and re-used them to manufacture a new pressure vessel. This is the first time this process has been achieved in the UK and represents a significant milestone in the development of Britain’s hydrogen capability.
As the gas has low energy density it needs to be compressed and stored at very high pressures, between 350 to 700 bar (5,076 – 10,152 psi). This makes high-strength, lower-weight carbon fibre the material of choice, especially for hydrogen pressure vessels in vehicles such as cars or aircraft, where power-to-weight is critical. Demand for carbon-fibre is expected to grow five-fold between 2025 and 2030, exceeding global manufacturing capacity. Creating viable, low cost recovery processes, that retain the inherent strength of continuous carbon fibres for recycling, is therefore key to the development of the hydrogen economy.
Until recently, recycling processes for composite components such as aircraft wings and wind turbine blades has resulted in short fibres with lower mechanical properties than virgin fibre. Whilst there are applications for this material, it is not suitable for re-use in high performing products.
Partnering with Lancashire-based B&M Longworth Ltd, the National Composites Centre team successfully reclaimed continuous carbon fibre, from end-of-life composite pressure tanks, using the company’s revolutionary DEECOM® process. Originally designed to remove waste polymers from filters and production equipment, the process uses superheated steam, under compression, to penetrate microscopic fissures in the composite’s polymer, where it then condenses. On decompression, it boils and expands, cracking the polymer and carrying away broken particles. This pressure swing cycle is then repeated until all the matrix (the material suspended in the polymer) has been separated from the fibre, allowing the monomers to also be reclaimed for possible reprocessing.
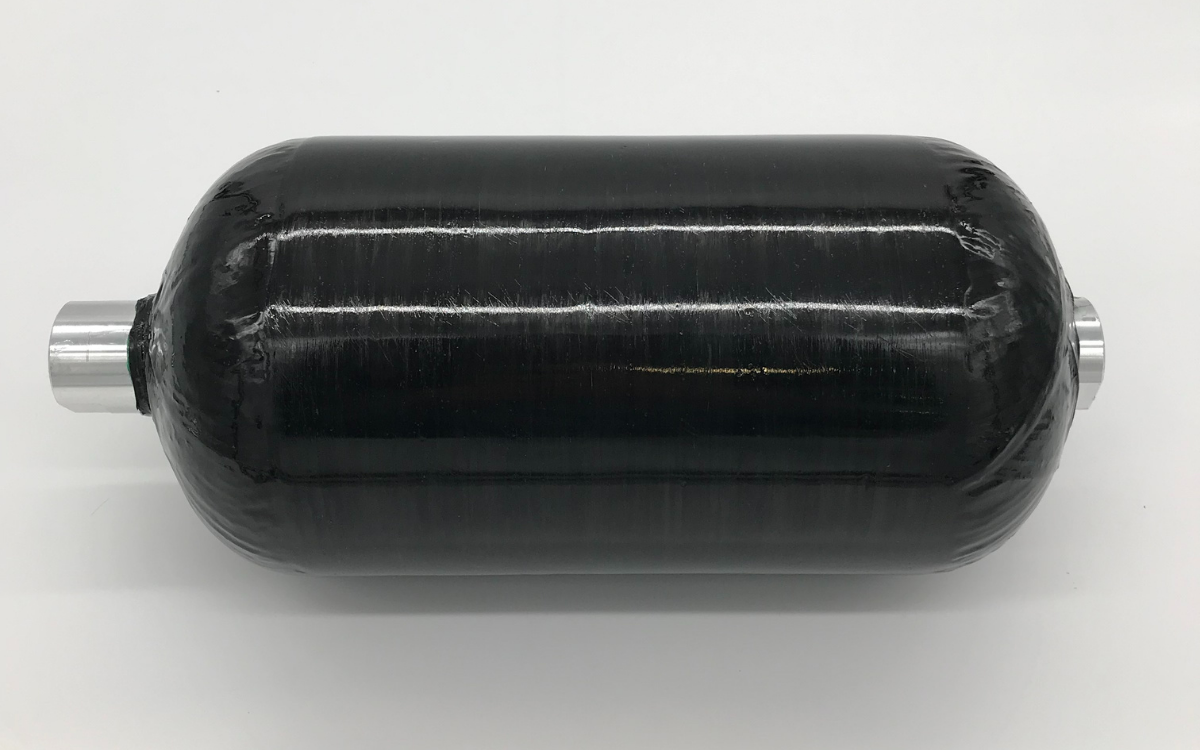
Crucially, the DEECOM® process leaves the primary component material intact and undamaged, allowing for any length to be retained. As a result, National Composites Centre engineers working with Cygnet Texkimp Ltd, a Cheshire-based, global leader of fibre handling and conversion technology, could use the reclaimed continuous carbon fibre to make a new pressure vessel using filament winding.
The partnership is now looking to work with manufacturers to scale and industrialise this process, sharing the knowledge of recent recycling trials. The next step is to undertake fibre characterisation analysis of the reclaimed material and recycled vessel, as the team works towards their ultimate goal: developing the disruptive technologies that enable sustainable hydrogen storage solutions.
The fibre recovery and recycling project, forms part of the National Composites Centre’s Hydrogen programme, developing and sharing the technical knowledge, cross-sector composite expertise and state of the art technology that businesses need to achieve their hydrogen ambitions.
As part of this programme, National Composite Centre engineers have worked to refine composite pressure vessel designs, producing detailed design and analysis to minimise waste and trial the tools and manufacturing processes industry will use to reclaim and recycle continuous carbon fibres. They have also delivered composite design specification for cryogenic pressure vessels and are working on a certification pathway for composite pressure pipes, including those to be used offshore.
Announcing the project results at JEC World, Marcus Walls-Bruck, Chief Engineer for Hydrogen at the National Composites Centre, says: “Achieving continuous fibre recovery is a significant step towards our goal of a fully recyclable certified tank – the critical technology barrier we need to address, if we are to embed hydrogen in our energy mix and meet net zero targets. We are at the stage of being able to share this expertise in fibre recovery and our extensive design exploration work for composite pressure vessels. We want to hear from companies interested in joining us on this journey to sustainable pressure vessels as we accelerate UK capabilities.”
Jen Hill, Director of B&M Longworth Ltd, says: “Following intensive R&D into the use of DEECOM® for composite reclamation and circularity, we’re excited to see successful reclamation and remanufacture of a pressure tank. Recent projects have seen success in a range of composite panels and automotive parts, so a move towards hydrogen tanks was the next logical challenge. Thanks to insight from experts at the National Composites Centre along with the expertise of our partners at Cygnet Texkimp, we’ve achieved what several said was impossible and are already progressing to the testing stage and looking for the next challenge.”
“Our dream is for the UK composites industry to succeed, through collaboration and true partnership. By pulling together we can onshore advanced material production, optimise reuse, reduce import and supply chain issues and improve the UK’s export potential, all while leading on sustainability in composites.”
Luke Vardy, CEO of Cygnet Texkimp, says: “One of the most exciting aspects of this collaboration and the technologies it is built around is the way in which we are able to maximise the value and integrity of the fibre at every stage in the process. Not only does this technology have the potential to transform end-of-life outcomes for composites, but it also shows how we can do so without compromising the essential properties of the fibre. That commitment to fibre integrity is extremely significant because it allows us to reclaim and repurpose carbon fibre in a way that is reliable and sustainable, while creating end products of the highest quality and consistency.”
Visit the National Composites Centre at JEC World in Hall 6, Stand R52 to see the recycled pressure vessel using reclaimed continuous carbon fibre, learn more about the innovation project and find out how the UK’s National Composites Centre can help you accelerate your composites for hydrogen ambitions.
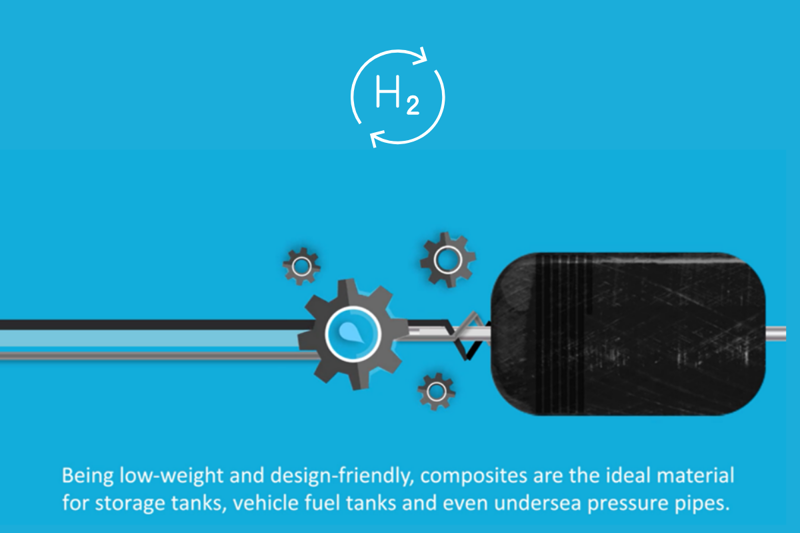