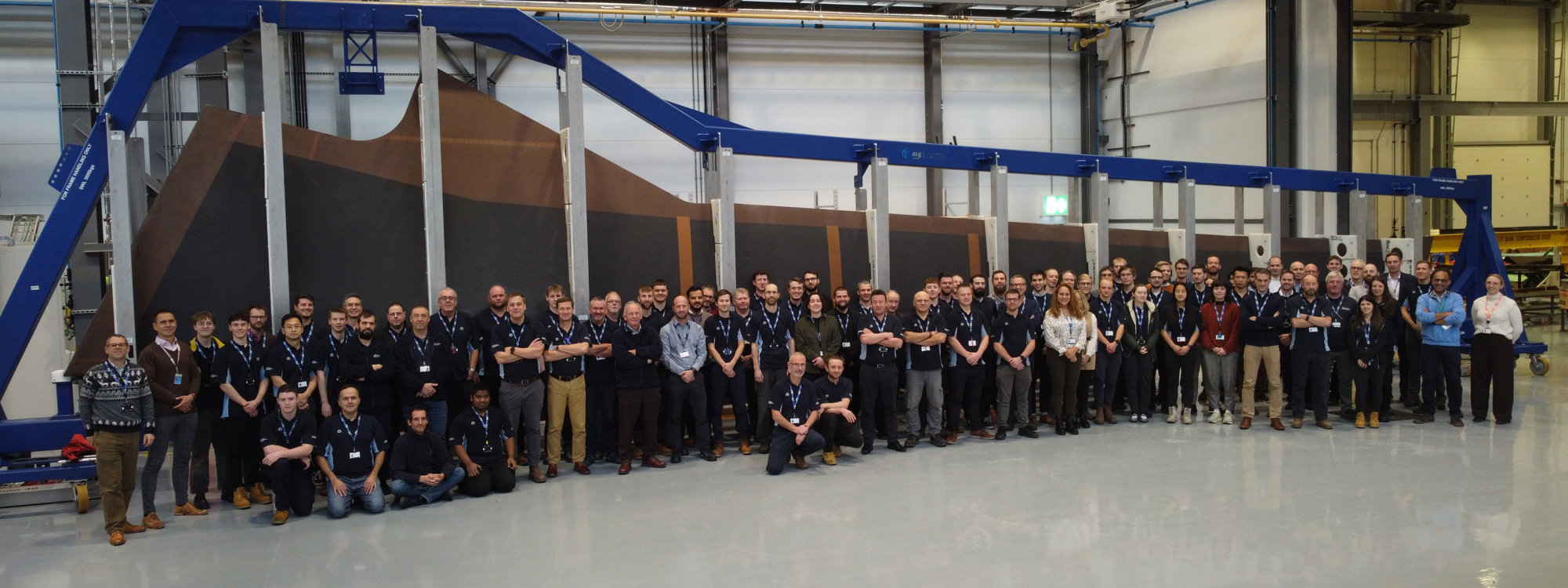
Wing of Tomorrow
- New composites deposition process developed: wing skin lay-up, fully automated using novel high-rate deposition technologies
- Team achieves world-first full scale 17-metre integrated wing skin infused in one step
To meet the growing performance and production demands of the next generation of fuel-efficient, low-emission aircraft, the aerospace industry must simultaneously decrease aircraft weight, lower costs, and increase production rates by a factor of ten beyond today's state-of-the-art capabilities. To address this challenge and to explore innovative new approaches to manufacture aircraft wings, Airbus created the Wing of Tomorrow programme.
Starting back in 2018, a collaborative team of engineers at NCC investigated materials, manufacturing, and component sub-assembly techniques for the upper wing cover utilising a pyramid of development which led to the ultimate delivery of three full-scale, 17 metre wing demonstrators.
Composites for aircraft wings
Composites enable wing components to be fully weight optimised and produced with significantly reduced or eliminated sub-assembly and post-manufacturing costs. They also enable faster production cycles.
Today, this is mainly achieved through the use of pre-preg composite materials – and developing the technology to realise the potential rate increase with dry fibre composites is a significant opportunity. To pursue this, NCC has been working with Airbus to drive dry fibre composites innovation for future wing components and assemblies.
NCC was tasked with developing technologies and processes to produce three, full-scale, wing cover demonstrators in support of the next generation single-aisle aircraft. In order to decrease the final assembly duration, the target for this program was that the wing cover should also include high levels of component integration, saving assembly time and weight.
Transforming wing cover manufacture
To automate the dry fibre fabric ply lay-up of the skin at such a large scale, NCC applied the latest digital design tools to simultaneously evaluate different configurations of cutting and layout. This new design philosophy demanded new technical manufacturing capabilities, with the Wing of Tomorrow team driving innovation in automated lay-up and full-scale dry fibre infusion of the wing upper cover.
Automated high-rate deposition
As part of their core composites research and development mandate, utilising the High Value Manufacturing Catapult and Aerospace Technology Institute (ATI) funding, NCC has developed a world-first high-rate deposition technology – which was designed to specification and supplied by UK manufacturer Loop Technology with collaboration from Güdel and Coriolis. It comprises two bridges, weighing 45 tonnes and 24 tonnes, 7 metres high by 13 metres wide, running along a 26-metre track. These bridges position automated end-effectors to enable cutting and deposition of dry fibre materials to high levels of quality and speed.
The automated process begins at a 20 metre table positioned inside the cell where an ultrasonic cutter profiles the carbon fabric to shape. An algorithm then selects the correct end-effector to pick the material up and then lay it onto the tool. Once lay-up of all the plies, processing and integration is complete, the component can then be infused with resin and cured.
Through Wing of Tomorrow trials, NCC's team has pushed the capabilities of dry fibre deposition technology and successfully demonstrated that automation can be achieved, with the potential to significantly increase production rate. For Wing Cover 3, the complete ply stack of dry fibre piece parts (approximately 170 individual dry fibre pieces) was deposited using NCC's Ultra High Rate Composite Deposition, with no manual intervention. During this production process, different rates of deposition were trialled and some of the full 17 metre length plies were deposited at close to maximum rate (0.8m/s). This equates to approximately 30 seconds for an individual 17 metre ply.
Large-scale resin infusion
In parallel, the team has achieved a world first in large-scale, highly complex single shot integrated structure resin infusion. Traditionally, sub-components are supplied separately, which are bonded or mechanically fastened to the upper wing cover during manufacture and/or assembly. For the Wing of Tomorrow demonstrators, the team cut the need for this stage by creating a large-scale infusion capability and using novel methodology. Due to the complex geometry of the wing and the size of the component, NCC and Airbus engineers had to devise a new infusion strategy – ensuring a sophisticated resin delivery system infused each sub-component at exactly the right time, avoiding defects that would affect part integrity from being generated.
Results
NCC has delivered the final of the three wing covers. This demonstrator was built to show the rate capabilities of automated deposition technology. Wing Cover 1 proved to Airbus they could successfully manufacture and assemble the new integrated wing cover with the other wing components from across their supply chain. The second cover was sent for mechanical testing. As part of the programme trials, NCC demonstrated that the rates achieved, when extrapolated, will lead to deposition volumes reaching in excess of 350kg per hour, with material being deposited from the head onto a complex double curvature tool.
Next steps
NCC, alongside Airbus, successfully demonstrated the technical feasibility of full-scale, complex, dry fibre infused wing covers and were able to define the rate potential of this methodology. This is what NCC was created to do – to take calculated risks, to make bold ideas happen, make it viable and make it commercially available, and then target the ways of minimising the risks for customers in investing in this kind of technology. Over the course of the programme, NCC has gained a new foundation of technical knowledge and offerings which will underpin future rate capability programmes.
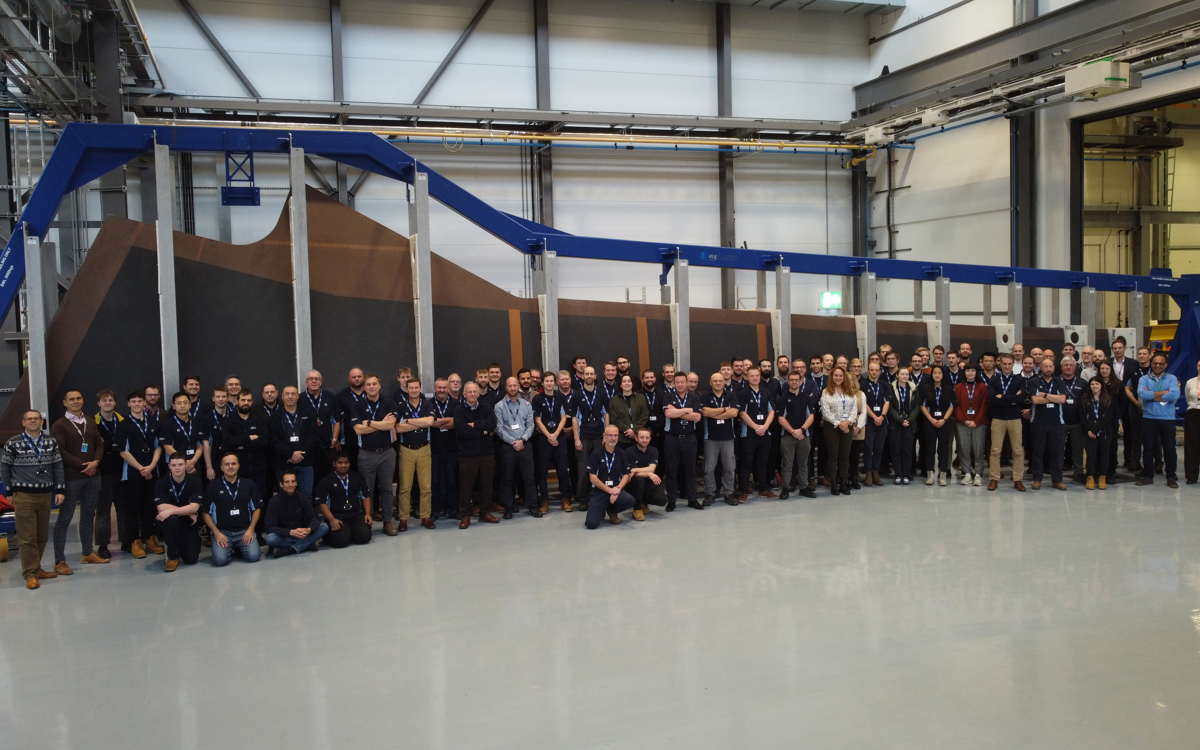