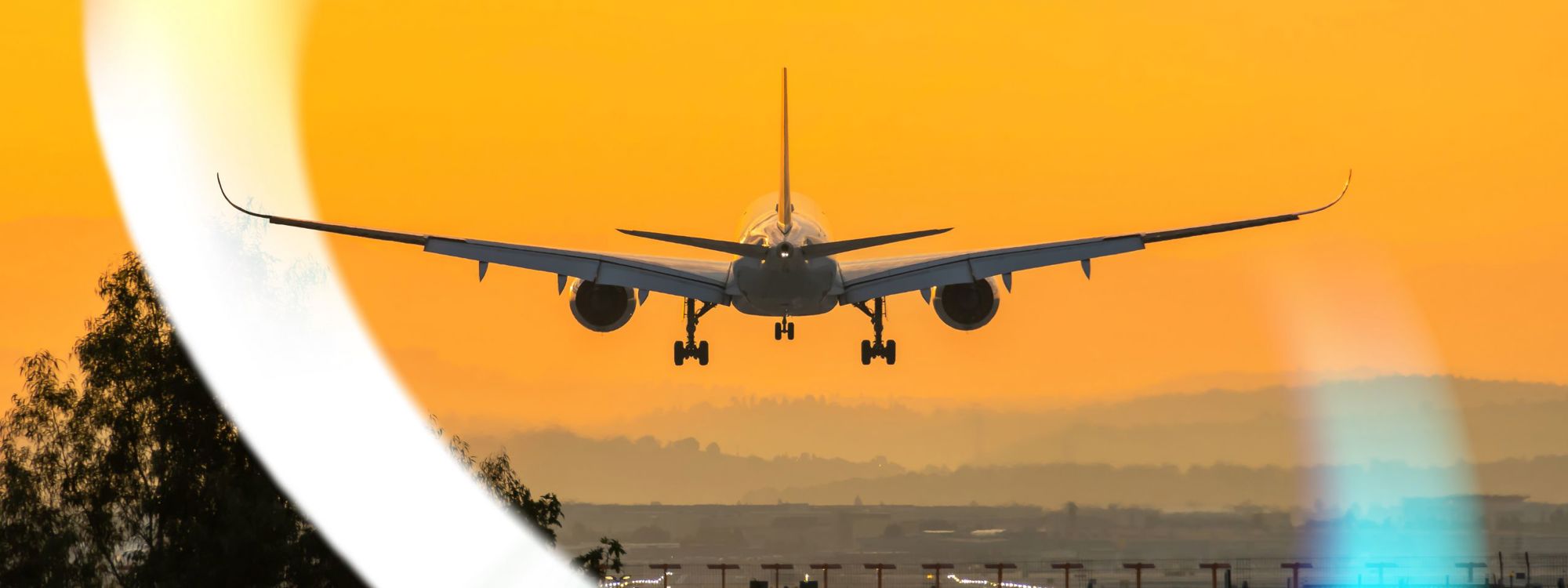
Positioning the UK in a leading role on future civil platforms
Delivering truly sustainable aviation is a huge technology and innovation challenge. NCC is working in partnership with global leaders in the aerospace industry to meet this challenge, developing the future materials, products and processes that will transform aircraft for generations to come.
The UK’s leading centre of excellence for composite technology, NCC is home to world-leading capabilities and has deep expertise and experience in working across the sector. This includes working in partnership with the UK’s Aerospace Technology Institute (ATI) to deliver long-term capability and innovation for the UK’s aerospace sector.
NCC is anchoring future UK aerospace composite component manufacturing through high-rate, sustainable processes and technologies. Deploying capabilities from material characterisation to manufacturing flying parts, we deliver industrialised, certifiable solutions for future flight.
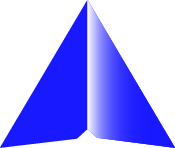
Get In Touch
Connect with our Aerospace Specialists at NCC to find out more about our world-leading innovation capabilities and how we can support your business.
Civil aerospace focus areas across the technology and product life cycle
Major Programmes
We connect technology strategy to real-world delivery through our end-to-end engineering services