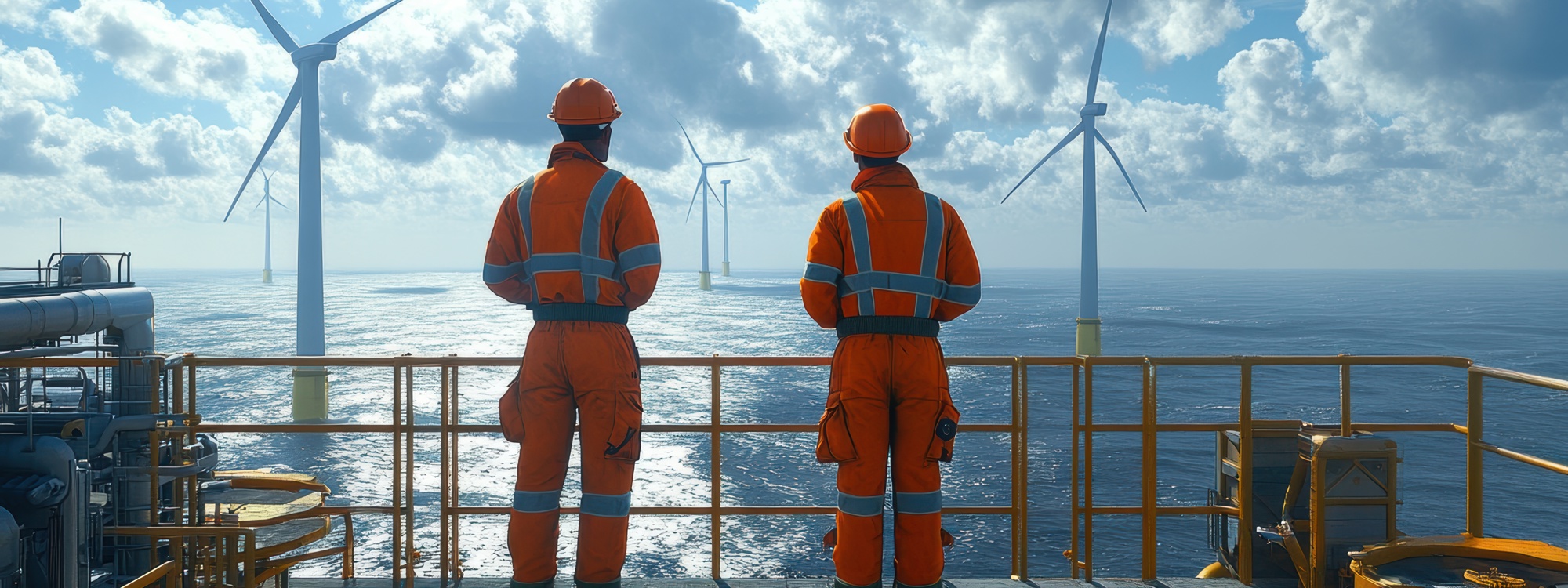
Sectors
Driving innovation across multiple technologies and growth driving sectors
We drive innovation across multiple technologies and growth-driving sectors – working with businesses of all sizes, academia and government to solve complex challenges. Our unique approach combines deep technical expertise with end-to-end engineering to unlock value and accelerate progress.
From addressing short-term market failures to seizing long-term strategic opportunities, we apply our capabilities where they’re needed most, focusing on impact, resilience and growth.
By extending our reach from industrial sectors into adjacent markets, we continue to deliver benefits across the UK economy and support national priorities. Find out more about our lead growth sectors below.
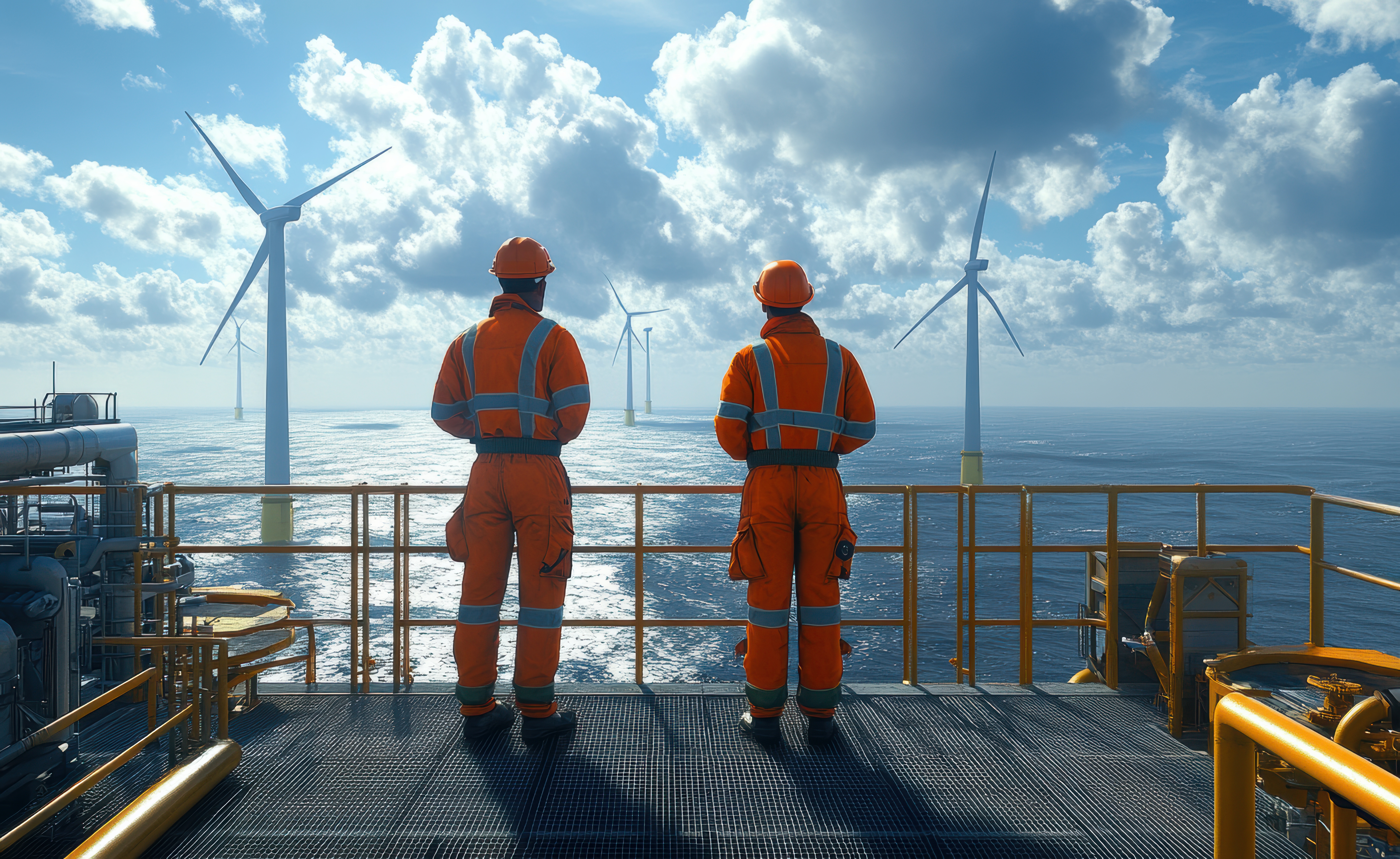
Get In Touch
Connect with our Sector Specialists at NCC to find out more about our world-leading innovation capabilities and how we can support your business.
Lead growth sectors
We connect technology strategy to real-world delivery through our end-to-end engineering services