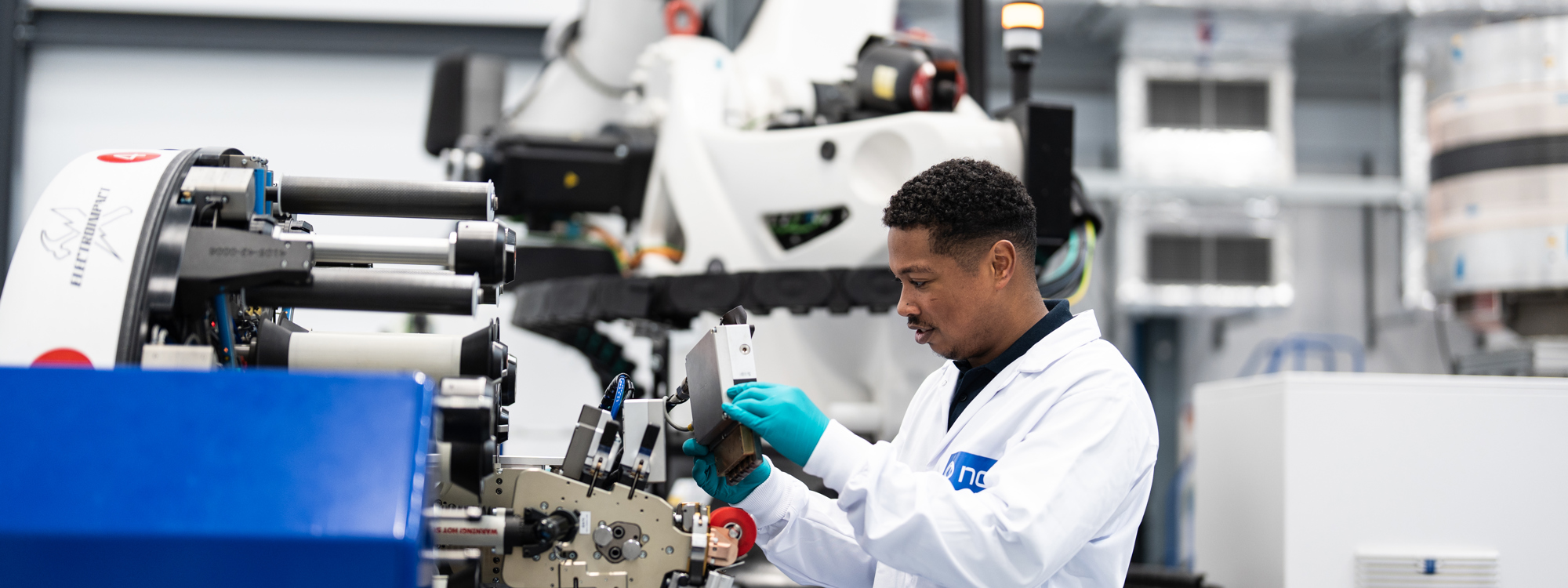
Focus areas across the technology and product lifecycle
Technology – Advanced Materials
Materials are the basis of all manufactured products and make up much of their value. Capturing more of that value in the UK is a critical enabler of economic growth and national resilience.
We are working at the forefront of advanced materials innovation, creating material solutions that address the full life cycle – from new materials development to end-of-life solutions. This underpins our ability to deliver product leadership for industry and secure the competitiveness of the sectors we serve.
In addition to excellence in composite material processing and application, we are:
- Developing the UK’s first carbon fibre development line to secure sovereign capability
- Pioneering work in next-generation high-performance materials, including ceramic matrix composites (CMCs)
- Leading industry sustainability and recycling initiatives
- developing other high-performance materials and processes (non-composite)
Our Future in Advanced Materials
To support the UK’s high-performance materials sector, we are:
- Expanding our partnerships across academia, RTOs and industry to accelerate the development and application of advanced materials in critical sectors
- Growing UK capability in material development and production, integrating digital tools to improve performance, traceability and speed to market
- Delivering unique activities focused on sustainability, recycling and circularity – reducing environmental impact and securing resilient supply chains for our industrial sectors
Focus Areas Across the Technology and Product Life Cycle
We are continually exploring opportunities to pull through advanced and emerging materials research excellence and to explore applications across growth-driving sectors such as aerospace, defence and energy. This includes:
- Future fibres
- CMCs
- Other high-performance materials
- Improvements in existing materials (e.g. glass fibre)
- Circularity and recycling solutions
Technology – Digital Technologies and Artificial Intelligence
Digital technologies and artificial intelligence (AI) are transforming the way we design, make and deliver engineered products and processes – unlocking speed, precision and smarter decisions. NCC embeds high-performance computing, modelling and AI to deliver the most value today while building the capabilities needed for tomorrow.
By harnessing advanced digital technologies, we’re accelerating innovation, strengthening UK supply chains and shaping a high-value, digitally enabled manufacturing future.
Our Future in Digitalisation
As a national centre of excellence in digital engineering, we apply our expertise where sector and business demand is strong while exploring new frontiers to converge digital with deep technology and adjacent markets.
We work with industry to improve product development and manufacturing time, cost, quality, consistency, resilience and risk through AI-enabled engineering tools such as certified digital workflows, simulation and data analytics. Our focus includes:
- Adopting digital and AI products and processes internally, enabling our engineers to deliver the most advanced engineering techniques to our customers
- Providing UK companies with access to a package of digital and AI support through scalable, open-source digital platforms and high-performance compute (HPC) infrastructure