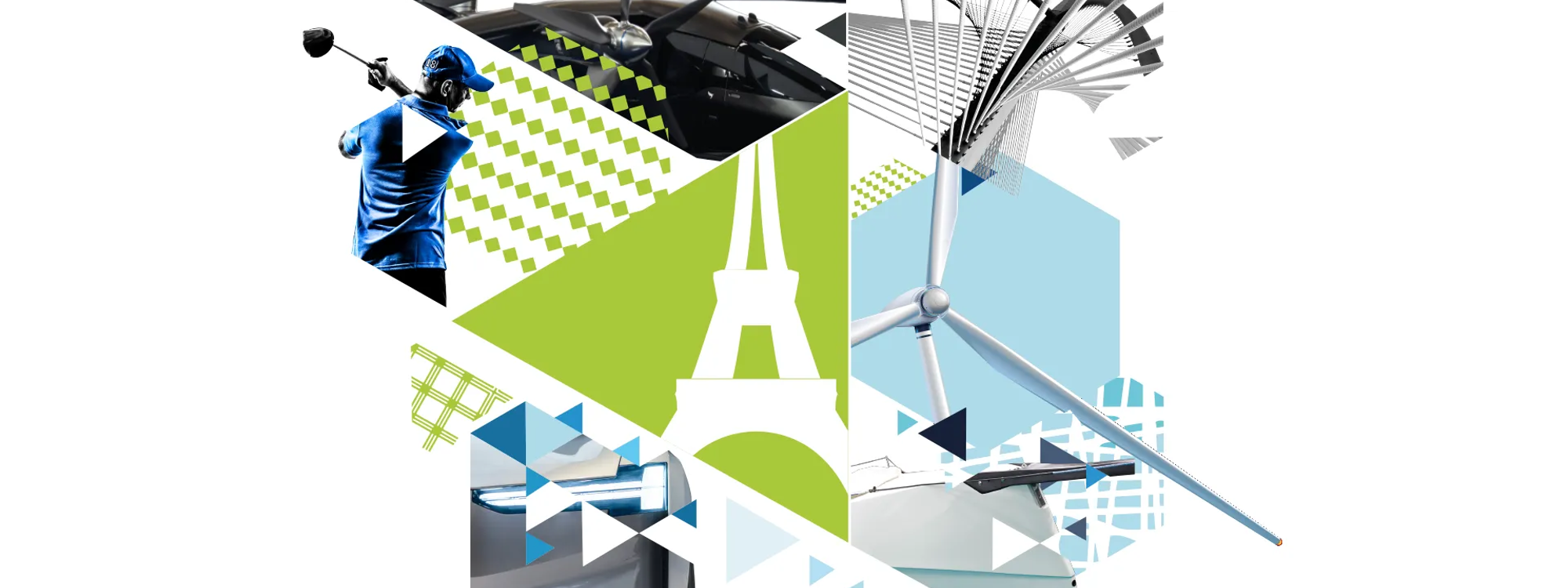
JEC World 2024 at Paris
The National Composites Centre (NCC), part of the High Value Manufacturing Catapult, exhibited at JEC World 2024 - the global trade show for composite materials and their applications.
Showcasing the industrial transformation that composites can offer, our engineering experts shared how composites are unlocking innovation and enabling sustainable opportunities towards a net zero future. This year, we focused on solutions towards accelerating the hydrogen economy and exploiting the performance, efficiency, and sustainability benefits of advanced materials.
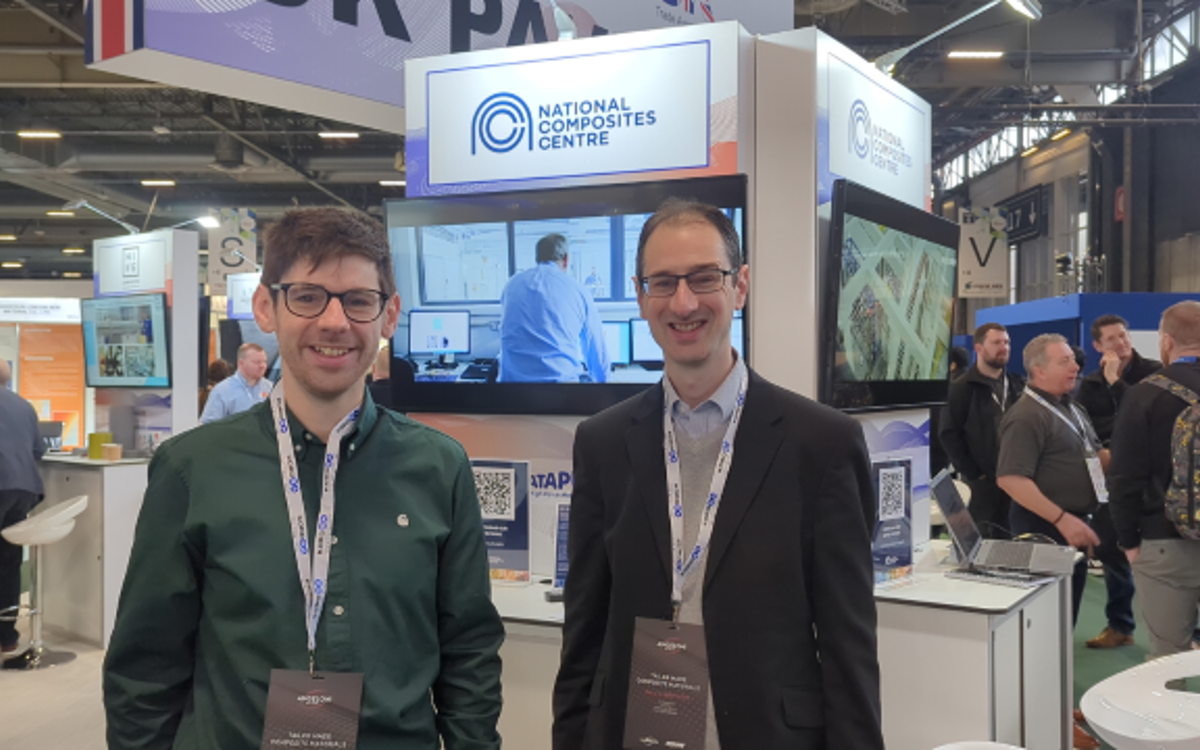
Announcement
NCC develops novel cryostat device and test method to advance UK capability for hydrogen
Hydrogen is set to play an important role in our future energy mix. There are challenges to accelerating the hydrogen economy – developing high-performing and sustainable hydrogen storage solutions is one of the technology barriers we need to overcome - and composites play an important role. Lightweight, strong, durable with significant design flexibility, they are the only practical solution to storing compressed hydrogen.
At the NCC, our specialist composites engineers are exploring innovation in the design and development of sustainable hydrogen pressure vessels, cryogenic tanks, and pipes. We have designed a novel cryostat device and test method that provides an ultrafast and cost-effective way to screen composite materials for conventional cryogenic testing.
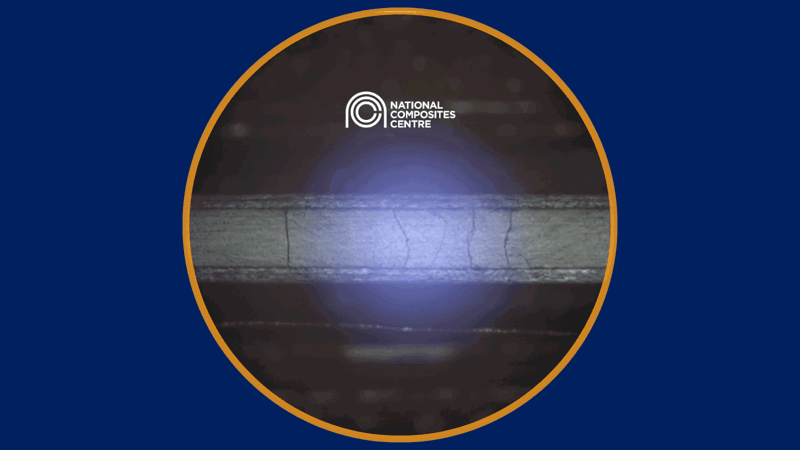
Our experts
Enrique Garcia, Chief Technology Officer at the National Composites Centre, participated in a panel session “Composites Manufacturing 4.0: Unlocking Efficiency and Sustainability Through Automation & Digitalization”.
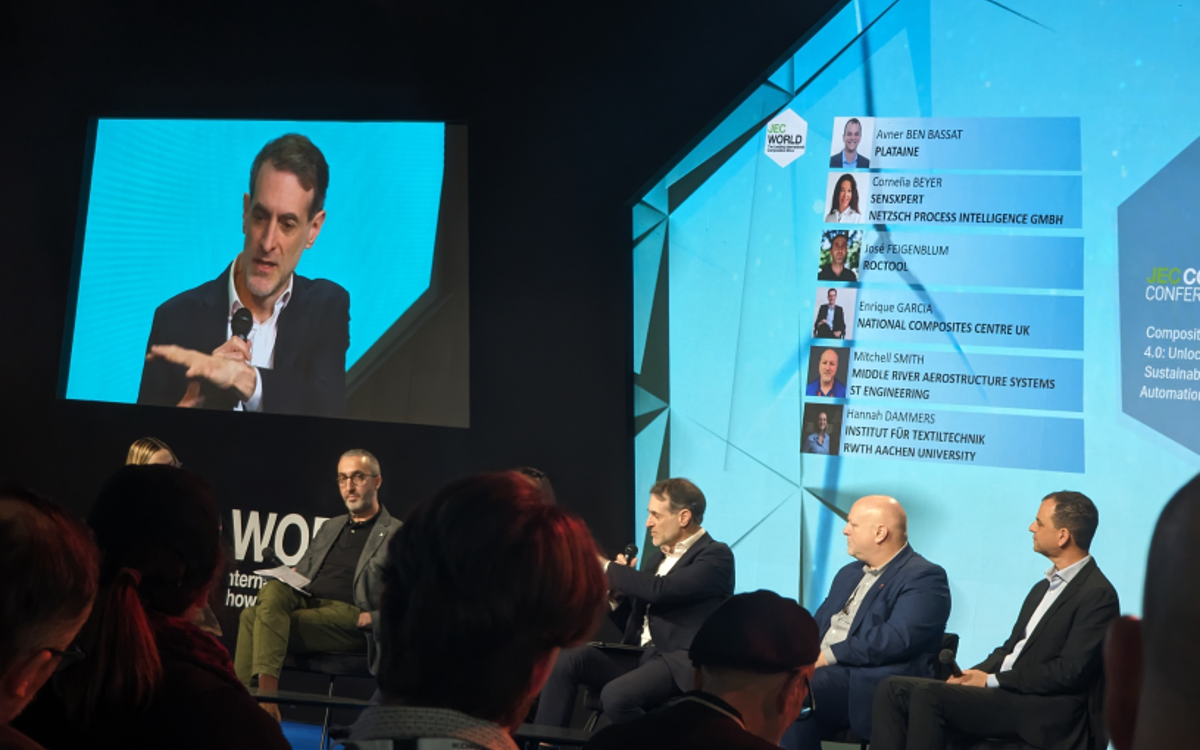
The following experts were also available throughout JEC World 2024 to share more about the NCC’s engineering capabilities and innovative solutions to meet your business needs:
- Sean Cooper, Chief Engineer for Defence & Space
- Daniel Galpin, Advanced Research Engineer for Hydrogen
- Dr David King, Engineering Capability Lead for Advanced Materials
- Alex Mathers, Technology Programme Manager for Defence & Space
- Hannah Swinbourne, Research Engineer
A closer look at our capabilities
The Filament Winder from Cygnet Texkimp is used to manufacture hydrogen pressure vessels, and is part of the NCC's state-of-the-art design, test and manufacturing facility for hydrogen.
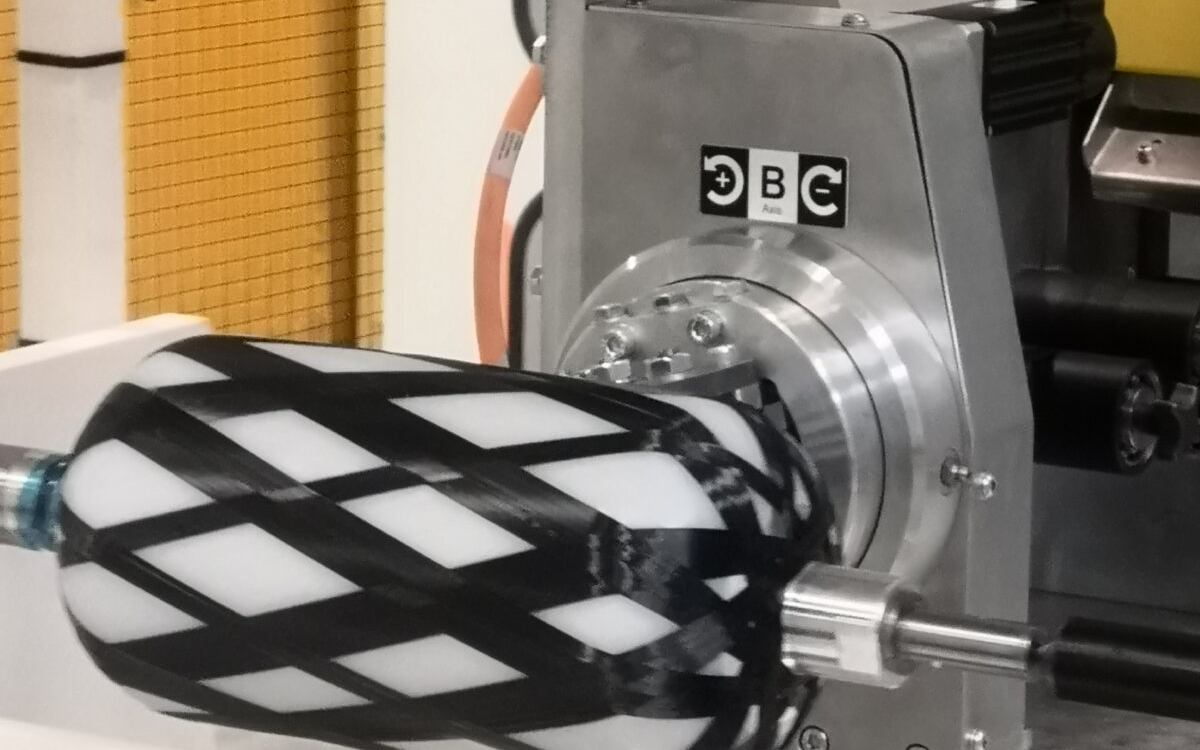
This is one of the state of the art Automated Fibre Placement- Automated Tape Layup (AFP-ATL) Capabilities at the UK's National Composites Centre. With a selection of heat sources and heads this fantastic piece of equipment is flexible for use for all sectors and available for use.
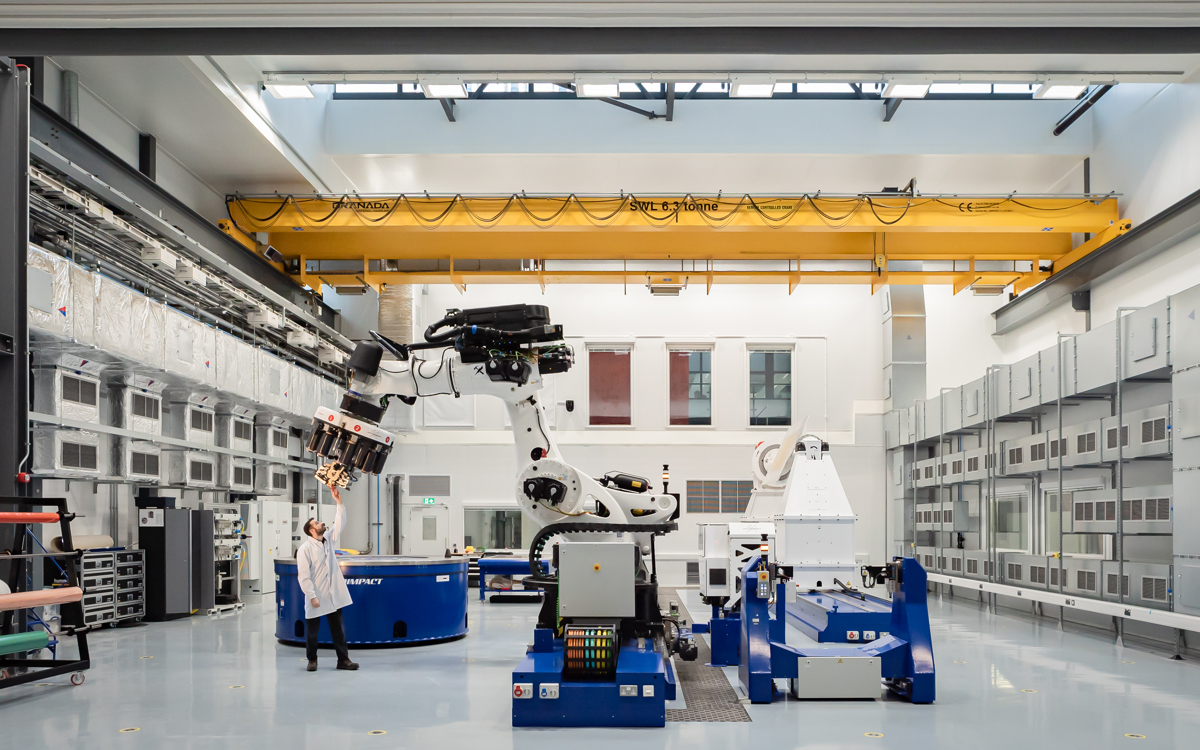
Comprising 288 and 192 spools, our braider is more than twice as flexible as a single ring braider. The two rings and a 10m long gantry enables us to braid complex circular, rectangular and convex sections, in the widest possible range from 50mm to 800mm equivalent diameter. The NCC braider is also capable of a very high deposition rate - up to 50 kg/h.
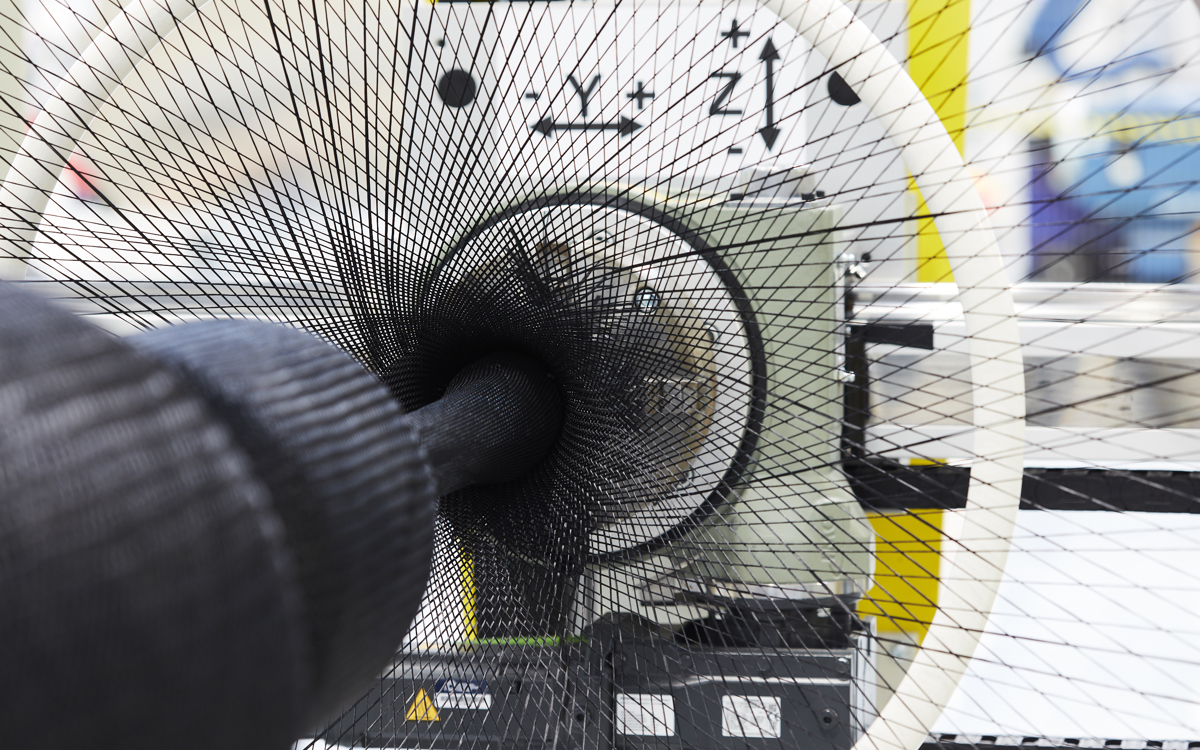
Tensioned Fibre Placement (TFP) technology enables multi-material layup capabilities enabled by multiple heat sources with interchangeable AFP and TFP end effectors. TFP allows the automated deposition of fibres in complex geometries. The equipment allows to mix filament winding and fibre placement into one single component.
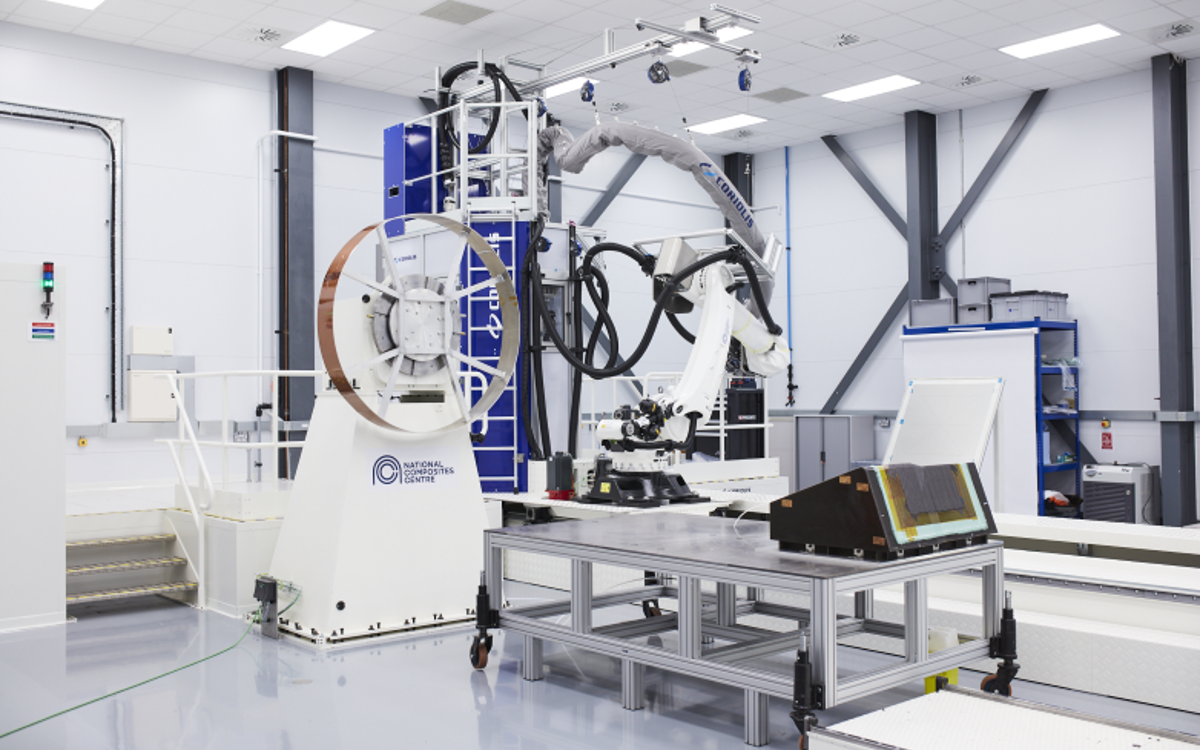
The Automated Preforming Cell (APC) enables the fabrication of parts using diverse processes and is capable of developing complex geometries in a fully automated process to create highly repeatable parts up to 1m x 3m.
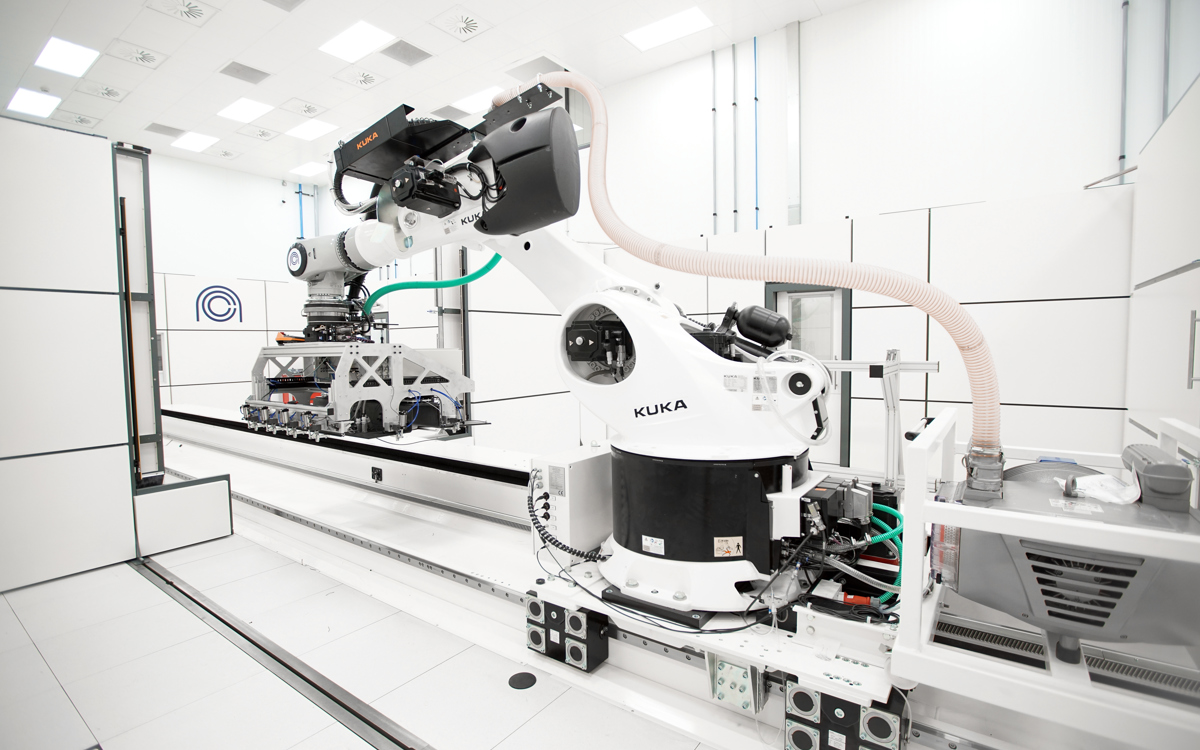
A composite sheet is melted and formed, and then thermoplastic polymer is injected over the surface in this highly automated process, that can achieve rapid cycle production of less than 5 minutes with potential for under 60 second cycle times for some parts.
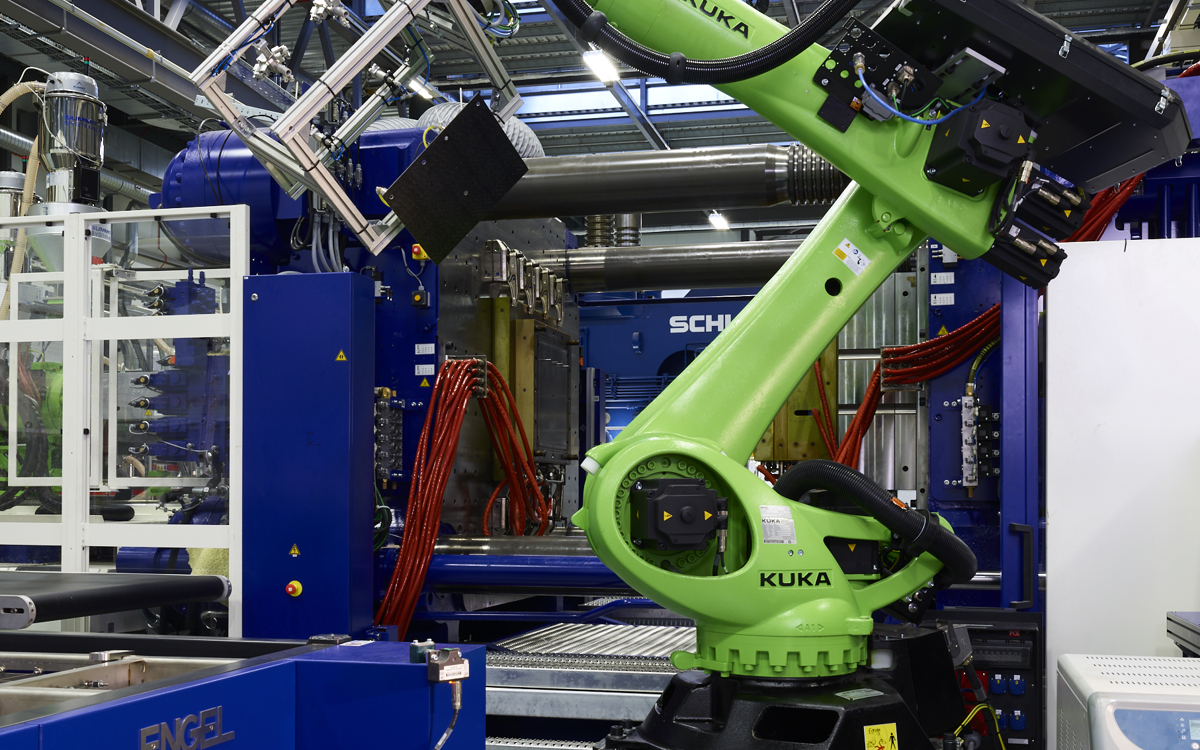