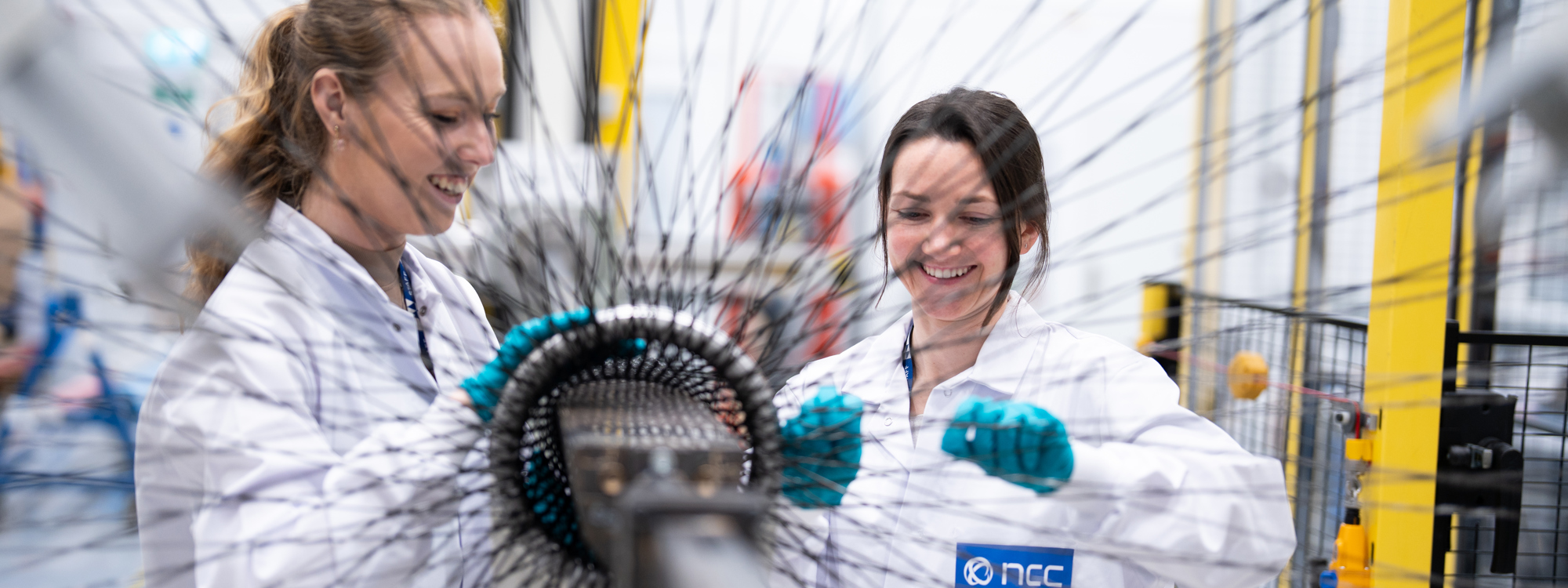
New braided blades to take on advanced air mobility market
NCC is working with UK SME Carbon ThreeSixty to develop new braided composite rotor blades suitable for an electric vertical take-off and landing (eVTOL) aircraft. The scalable, high volume manufacture rotor blades aim to capitalise on the rising momentum of the Advanced Air Mobility (AAM) market, and strengthen the UK eVTOL supply chain.
Challenge
The rapidly evolving Advanced Air Mobility market represents a unique event for the Aerospace industry, with a new breed of emission free, lower cost, more accessible, quieter, inter and intra-city travel possibilities. The demand of this new breed of aircraft requires a completely fresh approach to both the design and manufacture rotor blades and propellers, with most of these craft requiring up to 40 blades each, creating a vastly different cost/volume challenge and structure to that of traditional aerospace.
Advanced structural composites specialist Carbon ThreeSixty was keen to investigate a new eVTOL blade that was more affordable and structurally stable, delivered at a fast rate of manufacture. With funding support from the National Aerospace Technology Exploitation Programme (NATEP), the SME Affiliate Member leveraged NCC expertise for the analysis support, and key aspects of the manufacturing development for a viable prototype.
Results
Focused on high volume, low-cost alternatives, the collaboration between Carbon ThreeSixty and NCC delivered a scalable manufacturing process solution with the potential to supply up to 100,000 rotor blades per annum – and proposed production savings of 50% per blade. The high-volume cost-saving prototype leverages Carbon ThreeSixty’s ability to design and manufacture key aerospace structures and strengthens their capability in key composite manufacturing technologies like fast Resin Transfer Moulding (RTM) and Tailored Fibre Placement. Additionally, HALOS leveraged NCC’s capabilities in braid deposition methodology and core competencies in eVTOL technology. The latter includes eVTOL blade and landing gear design, prototype, demonstration and supply chain industrialisation.
As a current drawback to the emerging nature of AAM is the lack of regulatory and certification standards, a key scope of the NCC’s work included a deep dive into the best applicable practices from VTOL and rotor aircrafts to ensure this new class of vehicle meets aerospace safety standards. Additionally, Carbon ThreeSixty conducted an extensive testing programme to validate the technology robustness and place Carbon ThreeSixty in a closer place to regulation and certification.
NCC’s suite of design and analysis services delivered an early stage model of bird impact strikes, this was then transferred to Carbon Threesixty to analyse the full bird strike load cases; reviewing challenges unique to an eVTOL flight environment; as well as defining optimal core design and selection. With eVTOL blades required for both vertical and horizontal deployment, the prototype underwent vigorous non-destructive testing (NDT) with CT scanning being used to verify its quality and performance across all stages of product and process development. Further bird-strike testing was carried out externally validation.

Innovation
Conventional blades rely on expensive foam cores. As an alternative, the Carbon ThreeSixty and NCC team devised an optimised tailored fibre placement (TFP) internal skeletal structure with a thermoformed multi-part foam core enabling the best compromise between performance, weight and cost.
Where standard manufacturing practices rely on manual layup processes, NCC’s in-house braider enabled the team to overbraid an entire skin directly onto the core. This automated braiding technique eliminates a manual step, to facilitate faster production times and local fibre tailoring. This was taken a step further, by Carbon ThreeSixty’s use of TFP to optimise the spar stiffness along the length of the blade while enhancing fibre deposition rate and enabling scope for automation. The combination of these techniques allowed Carbon ThreeSixty to explore additive manufacturing processes for quick prototyping and testing of different manufacturing approaches.
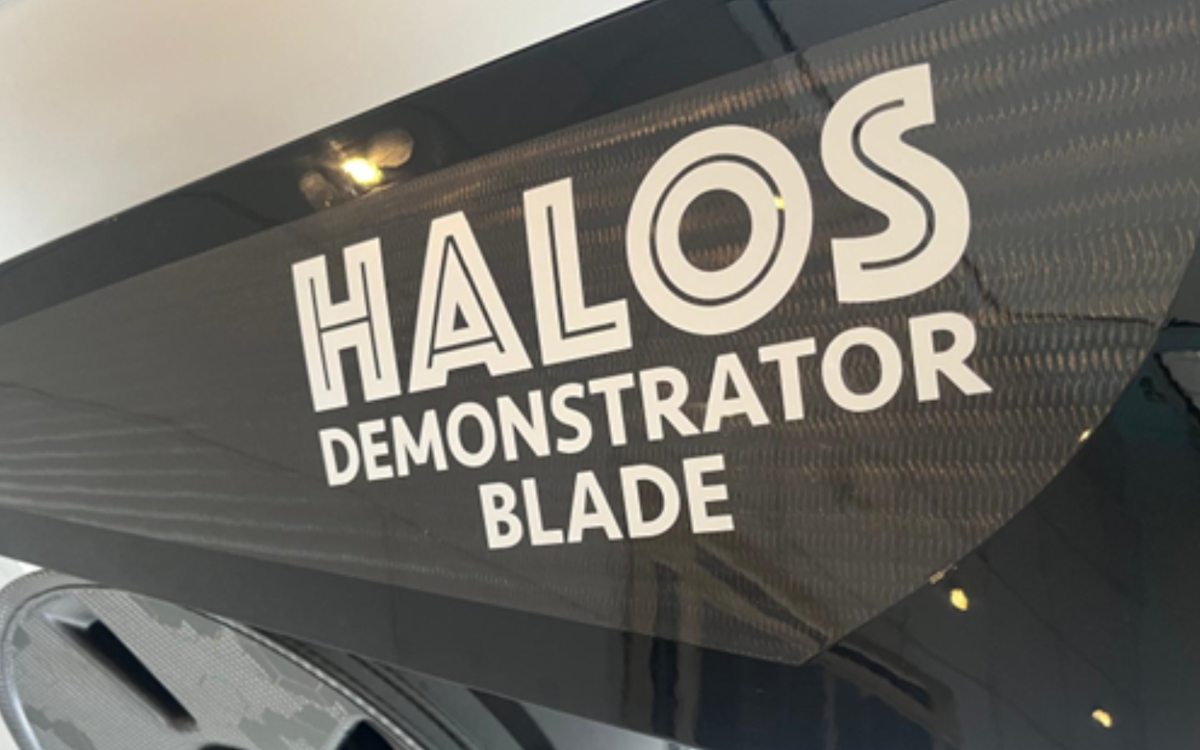
Impact & Next steps
The initial 18-month project enabled Carbon ThreeSixty to access knowledge of braider technology. With NCC’s guidance, this included exploring the braider’s direct tow-to-preform deposition and near-net form capabilities, enabling high-rate production with low waste, high quality and repeatability and post-braiding shaping.
The next phase of the project is seeking to further develop high-rate technologies for the aerospace sector and mature the combination of technologies and assembly of the structure. It will also involve working with supply chain manufacturers to expedite a competitive route to market and progress the technology and manufacturing readiness levels.
Gonçalo Valente, Lead Engineer for Research & Development, Carbon ThreeSixty says:
“Carbon ThreeSixty and NCC worked very well through the HALOS rotor blade project, having closely worked together to achieve the required results through regular technical meetings and clear specific goals and timelines.”
Adrian Tayler, Head of Aerospace, NCC says:
“NCC is focused on helping businesses of all sizes drive industrial transformation through innovation. With support from NATEP, the HALOS rotor blade project with Carbon ThreeSixty explores new design and manufacturing capabilities using high-rate, lower-cost manufacturing methods of blades.
"Our expertise in composite technologies and their application for high-rate manufacture across all aerospace platforms is helping ensure the UK supply chain has a competitive advantage in next generation propulsion solutions across the eVTOL, AAM and heavy lift drone application. The project’s methodology will also feed powerfully into other aerospace applications and cross sector applications which are facing similar challenges.”
For more information on how we can support your next innovation, reach out to [email protected]
To learn about our SME member, reach out to [email protected]
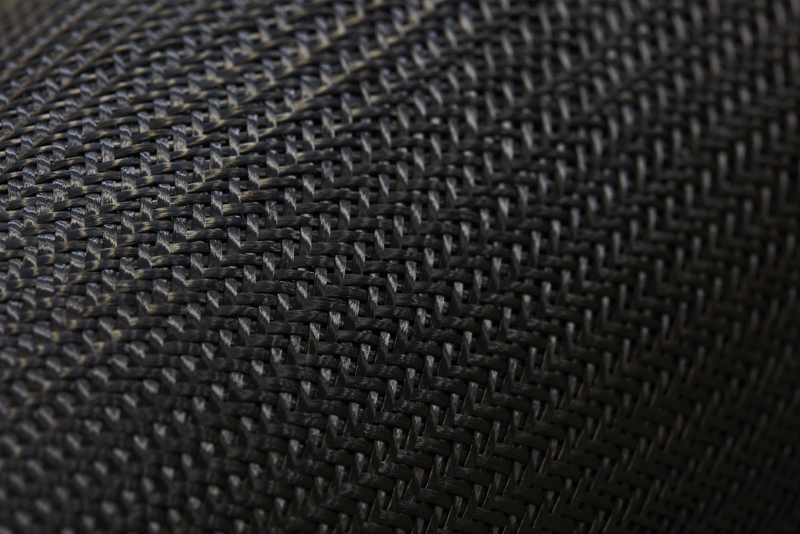